In Part One of our 700 horsepower small block Chevy build, Mr. Mavrigian got into prep of the Dart SHP block and Scat/Icon rotating assembly as well as installing the COMP Cams mechanical roller cam and Jesel belt drive. In this article, he’ll go over things like cam timing, the oiling system, installing the Trick Flow Ultra 18 cylinder heads and valvetrain, and the intake/carburetor selection.
***
Cam Timing
Advancing cam timing decreases intake valve-to-piston clearance and increases exhaust valve clearance. Retarding timing increases intake clearance and decreases exhaust clearance. During our valve-to-piston clearance check, we had 0.210 inch intake (excessive) and 0.080 inch exhaust clearance (too tight). The centerline for our COMP Cams roller cam came in at 108 degrees, exactly matching our cam card. We advanced the cam two degrees to move the intake centerline to 104 degrees, reducing intake clearance to 0.146 inch and increasing exhaust clearance to 0.125 inch. The change should improve low- and mid-range torque.
Oil Pan
Our Moroso Street/Strip oil pan has a seven-quart capacity. It’s designed for racing applications where hard cornering and braking are anticipated. The sump has side kickouts for additional capacity and features angled walls that reduce the potential for oil to rise up out of the sump during hard turns. A lightly spring-loaded trap door at the front of the 8.250 inch deep sump allows easy oil drainback into the sump, and the one-way trap door eliminates oil from being thrown out of the sump under hard braking.
Oil Pump
As with the majority of my builds, I used a Melling oil pump. In this case I chose the new high-pressure/standard volume “shark tooth” design that offers more consistent pressure and smoother operation. This pump has a “purple” high pressure spring and comes with a “yellow” spring that drops pressure about 10 PSI. Since Dart recommends avoiding high pressure/high volume pumps with their block’s ultra-efficient oiling system, I swapped to the yellow spring.
The Moroso oil pump pickup has a feed tube that press fits into the pump. It also features a bracket that shares two of the oil pump cover screws. We tack-welded the tube to the pump body for added insurance and installed an ARP oil pump driveshaft.
Roller Lifters
Lifter bore clearance is critical in order to maintain proper operating clearance and lubrication. The lifter manufacturer will specify the correct oil clearance, but a general rule of thumb is to shoot for about 0.0015 inch of clearance. Our Dart SHP Pro iron block is designed for 0.904 inch diameter lifters. Our roller lifters measured 0.903 inch, so we had the lifter bores machined to 0.9045 inch to get the required 0.0015 inch of oil clearance.
Cylinder Heads
For this build, we chose Trick Flow Ultra 18 250 cylinder heads. Eighteen degree heads offer several advantages over traditional 23 degree heads. The shallower valve angle allows the use of a smaller combustion chamber. That lets you run higher compression ratios without the need for high-dome pistons.
Another advantage of 18 degree heads involves valve location. In a 23 degree head, the valves are located 0.275 inch from the cylinder bore centerline. When the valves are close to maximum lift, they are slightly shrouded by the combustion chamber and cylinder wall, which is detrimental to flow. Intake valves on 18 degree heads are located directly on the bore centerline with the exhaust valves slightly closer to the cylinder wall. This eliminates the shrouding effect and allows the use of larger intake valves.
You will need a compatible intake manifold, offset shaft-mounted rocker arms, a solid roller cam, and compatible exhaust headers to run 18 degree heads.
Trick Flow Ultra 18 250 Cylinder Head Specs:
- Intake Port Volume: 250cc with Competition CNC porting
- Exhaust Port Volume: 100cc with Competition CNC porting
- Combustion Chamber Volume: 56cc CNC-profiled
- Intake Valves: 2.150″ stainless steel
- Exhaust Valves: 1.600″ stainless steel
- Valve Springs: 1.560″ double with damper. 500 lbs./inch rate, 0.700″ max. valve lift
- Locks: 10° with recess for lash caps
- Retainers: 10° titanium
- Minimum Bore Diameter: 4.155″
Like most 18 degree heads, the Trick Flow Ultra 18s have a water crossover design with a small water crossover loop that lets you run coolant from between the two center cylinders back to the water pump. The heads have a threaded hole between the two center exhaust ports to plumb a 1/4 inch NPT male to -4 AN or -6 AN hose end and hose. If the engine is not going to be run in long endurance applications, this plumbing is not needed—simply thread a 1/4 inch NPT plug in the hole. You will also have to plug the 10-24 threaded hole on the exhaust side of the head just below the 1/4 inch NPT hole.
Rocker Arms
The Trick Flow heads require shaft-style rocker arms with 0.550″ intake offset and 0.220″ exhaust offset. We chose Jesel roller rockers fitted with heavy duty roller bearings and precision hardened pushrod cup adjusters. The standard small block Chevy rocker arm ratio is 1.5:1. We increased lift by going to a 1.6:1 rocker arm. That resulted in 0.691-inch intake and 0.688-inch exhaust lift, well within the 0.700 inch lift rating of the Trick Flow valve springs.
COMP Cams suggests setting exhaust lash at 0.020 inch and intake lash at 0.016 inch. Once valve lash is set, Jesel recommends torquing the adjuster nuts to 25 ft.-lb. with oil or 20 ft.-lb. with ARP lube.
Pushrods
It’s always a good idea to measure for pushrod length. Our pushrod length was 8.650 inch. In order to reduce pushrod deflection under stress, we went with 3/8 inch pushrods from Trend. When using offset lifters and rockers, it’s important to check pushrod clearance where they pass through the cylinder head. With the 0.550 inch offset of the intake lifter cups, 3/8 inch pushrods get a bit close to the upper lifter bodies where they join the link bar, but they do clear by 0.008 inch.
Intake Manifold & Carburetor
I selected a Dart single plane manifold. Using airflow technology developed on NASCAR and NHRA engines, this manifold flows up to 10% more air than many comparable manifolds. The air-gap intake has a raised water crossover to insulate incoming air, an optimized intake runner cross-section to maximize high mixture velocity, and extended runner dividers to equalize port lengths. We installed the manifold using Fel-Pro intake gaskets and ARP 12-point stainless steel bolts. Do not use bolts longer than one inch as they will protrude into the pushrod passages, potentially contacting the pushrods.
I plumbed the manifold with Earl’s -8 AN fittings and hose to move hot coolant from the rear of the heads to the water neck and return to the radiator. The manifold has two 1/2 inch NPT threaded at the front and two at the rear. We plugged the front holes as we would not be using them.
The carburetor I chose is an 850 CFM Holley Ultra XP. The all-aluminum carburetor weighs four pounds less than traditional Holley carbs and features mechanical secondaries, four-corner idle adjustment, integrated idle bypass for compatibility with radical camshaft profiles, and fuel bowls with 20% more capacity to avoid starvation issues.
***
In Part 3 of our 422 small block saga, Mike will button up the engine with MSD ignition parts, a vacuum pump, and other accessories before strapping it to the dyno and flogging it to within an inch of its life. You won’t want to miss it!
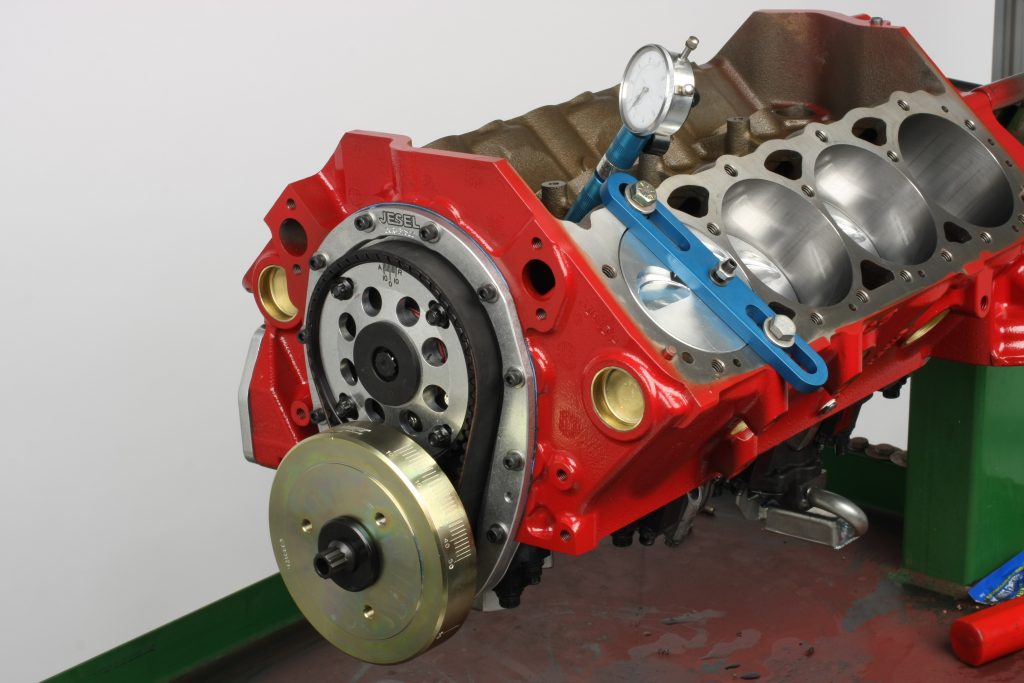
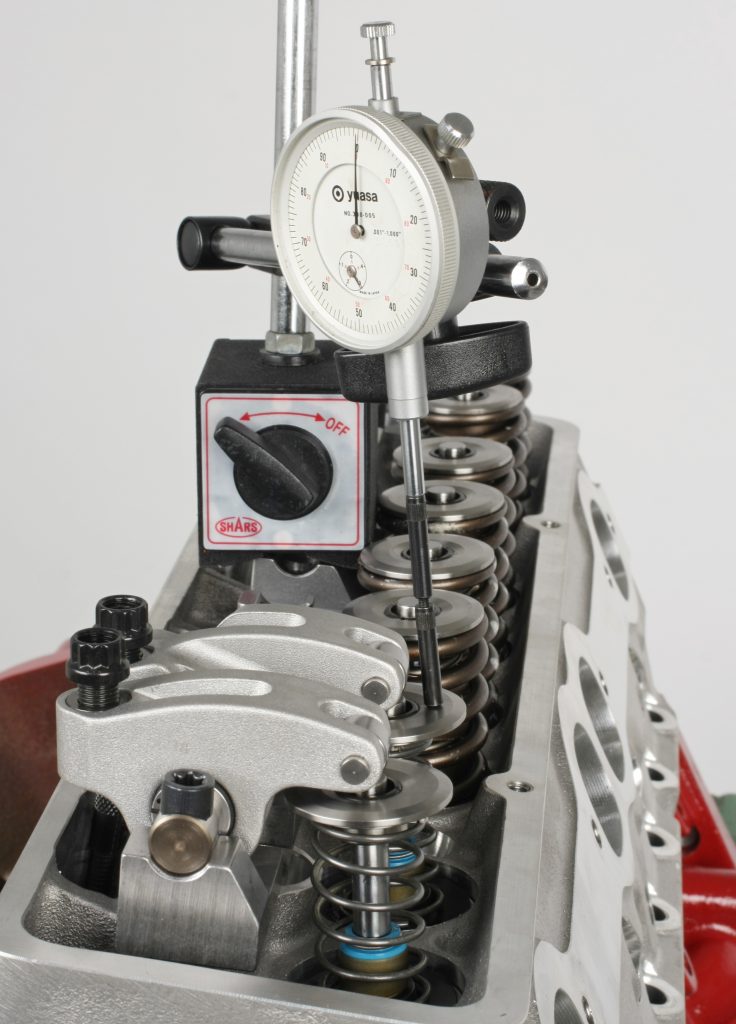
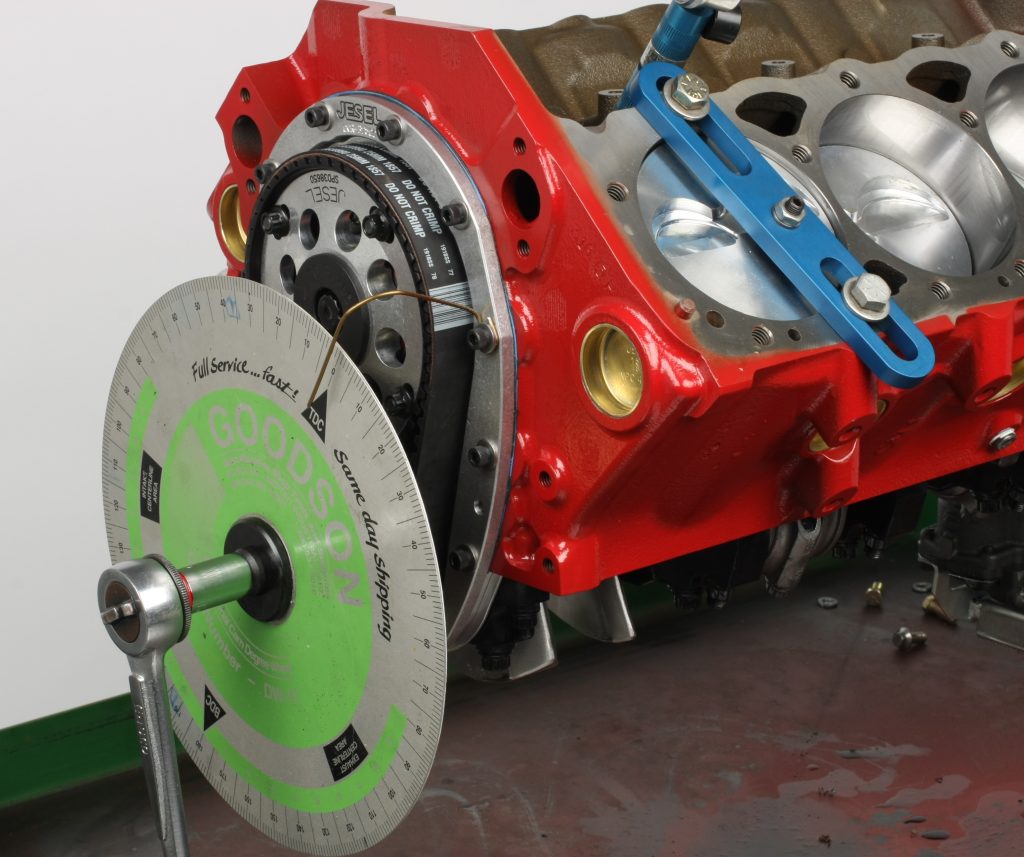
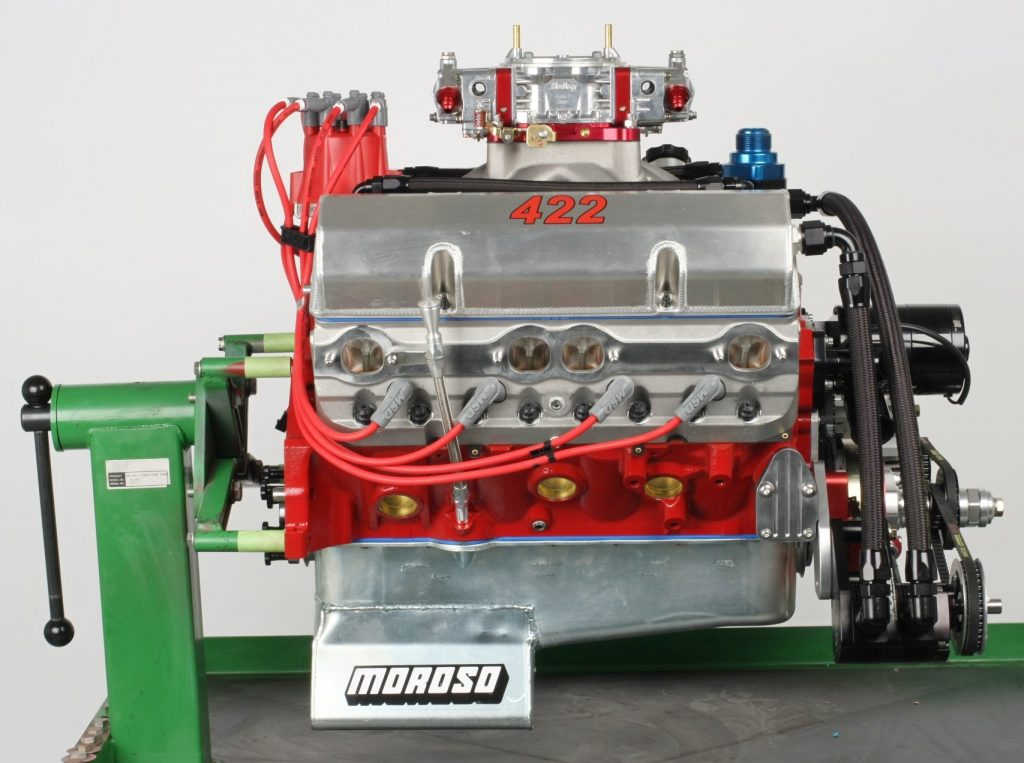
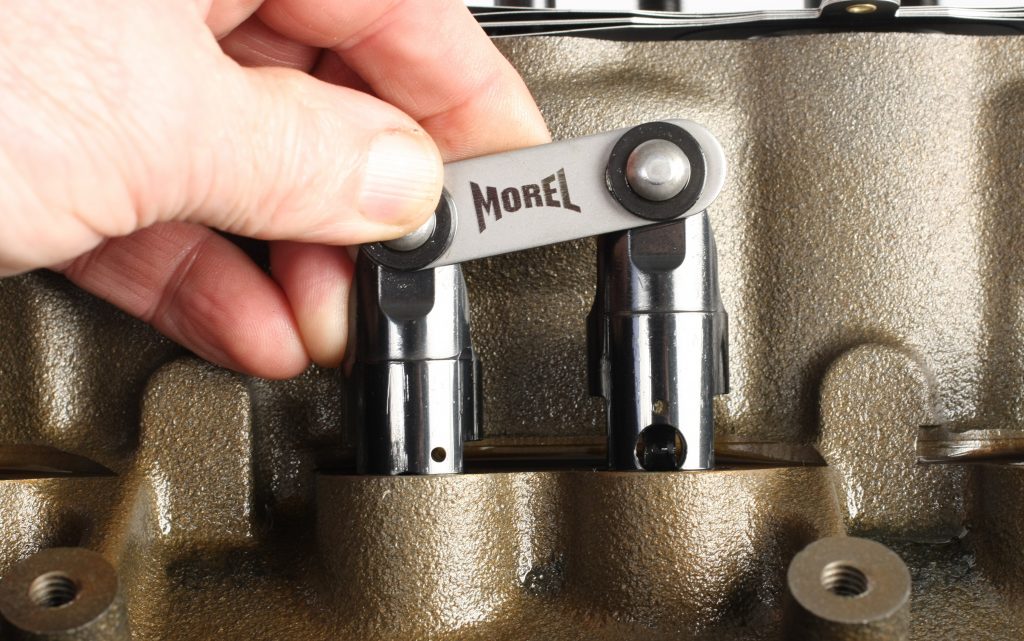
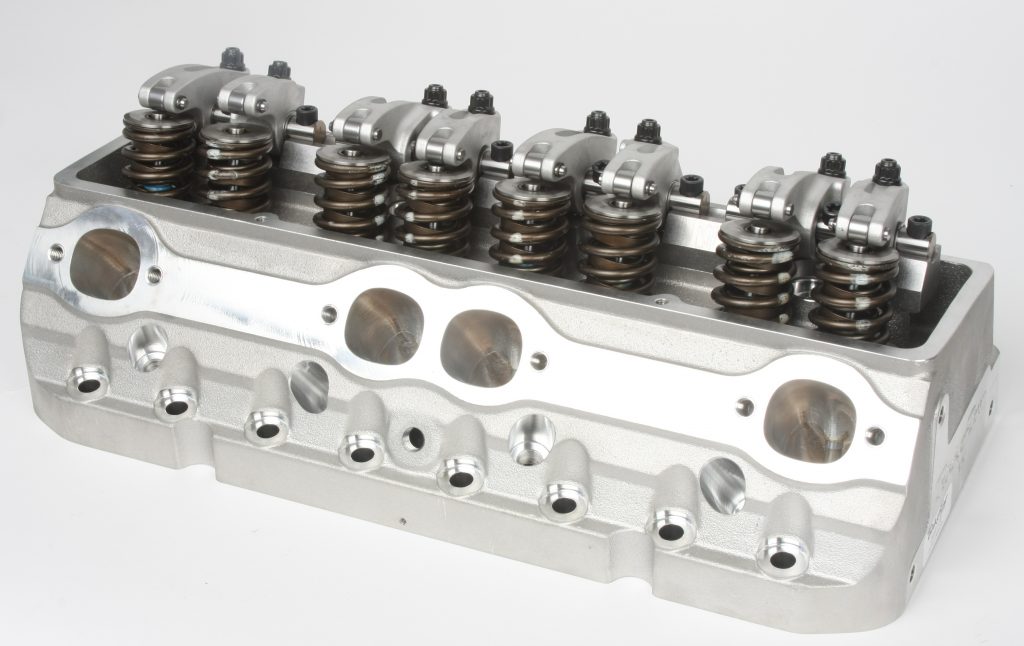
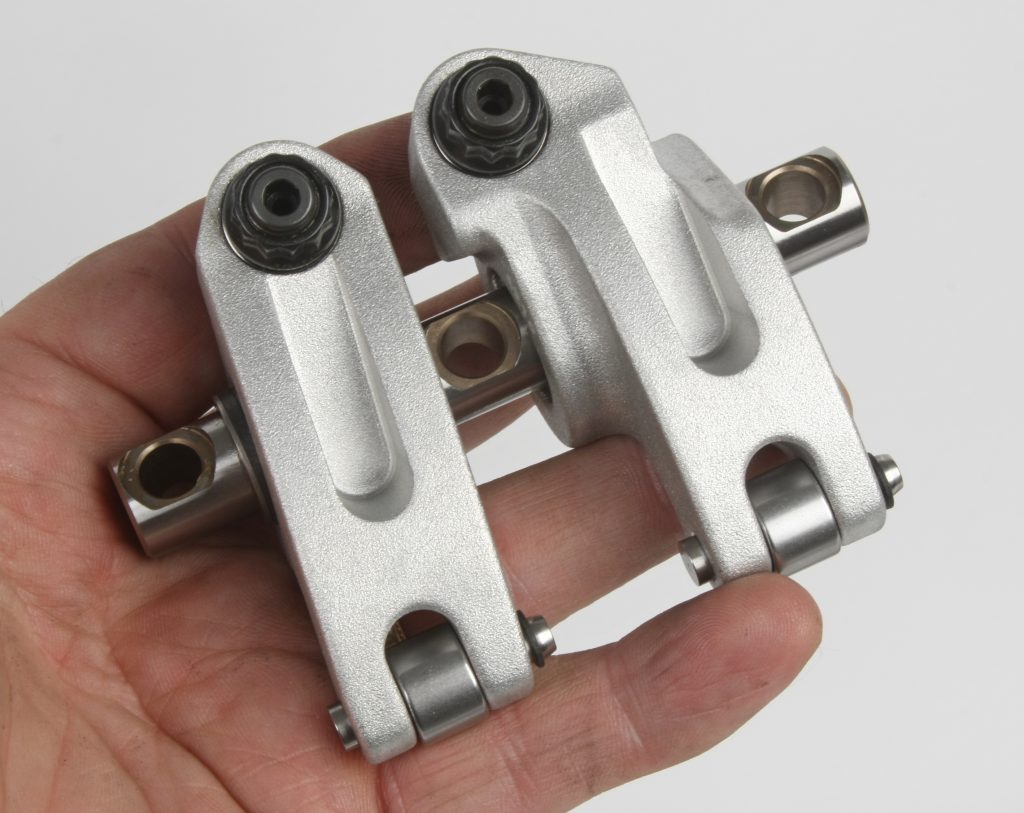
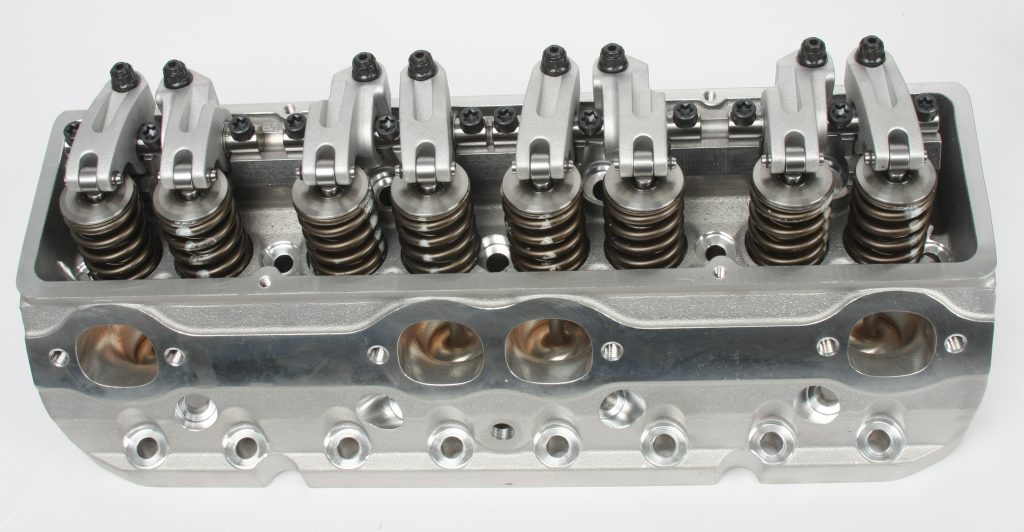
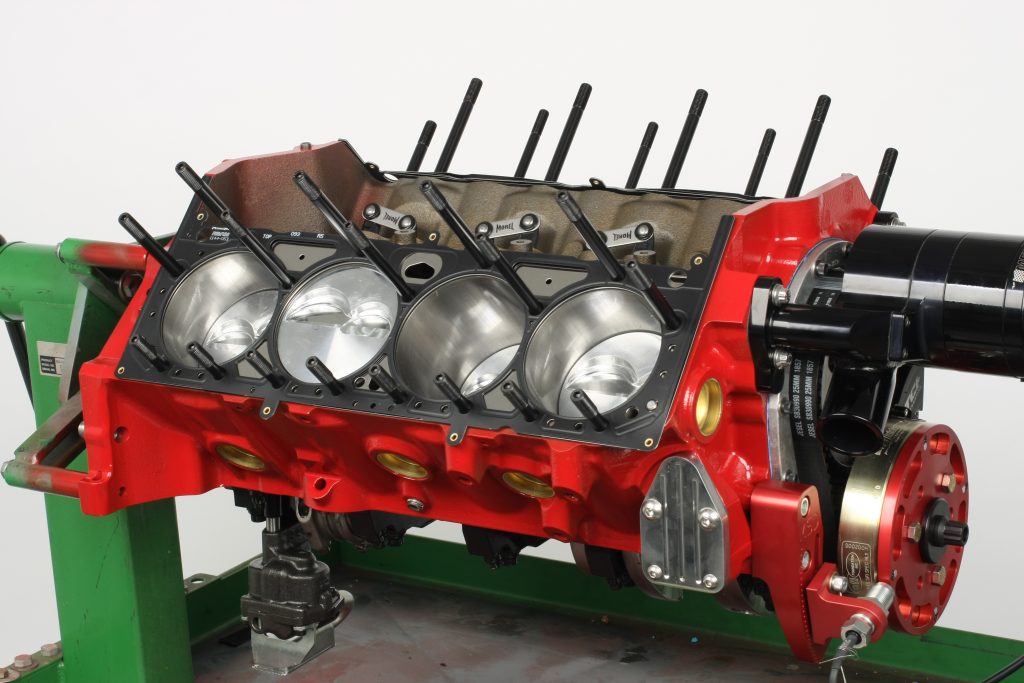
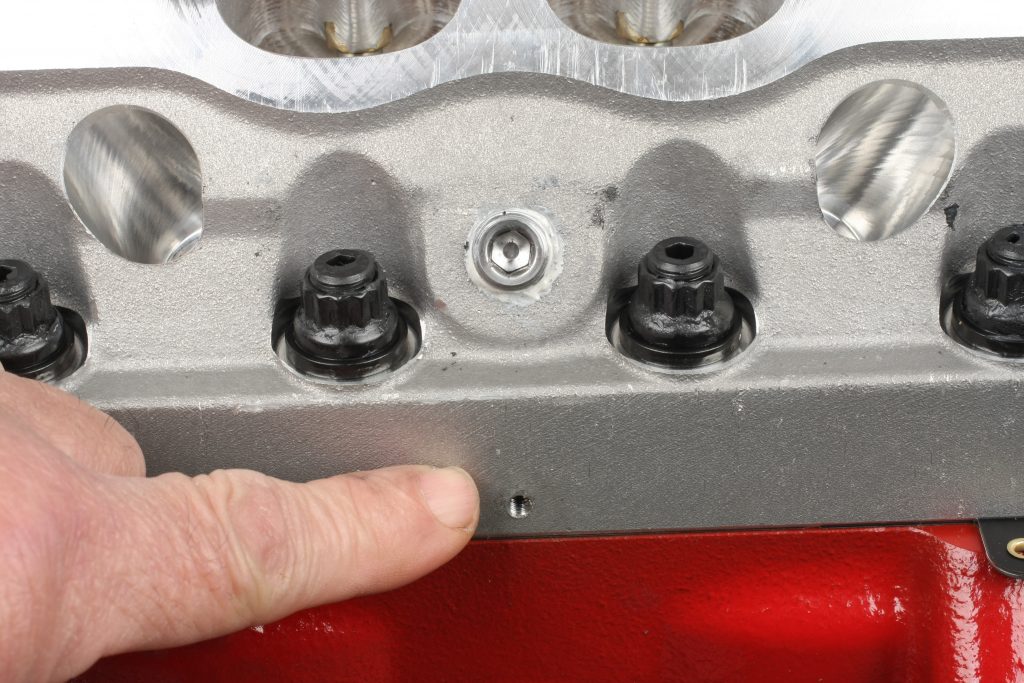
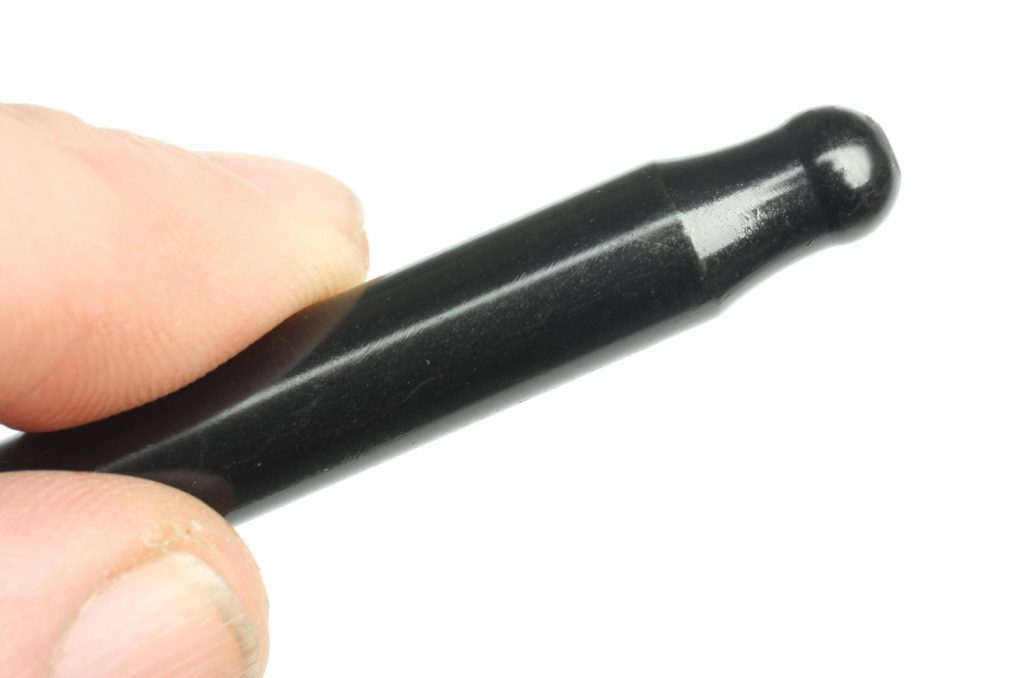
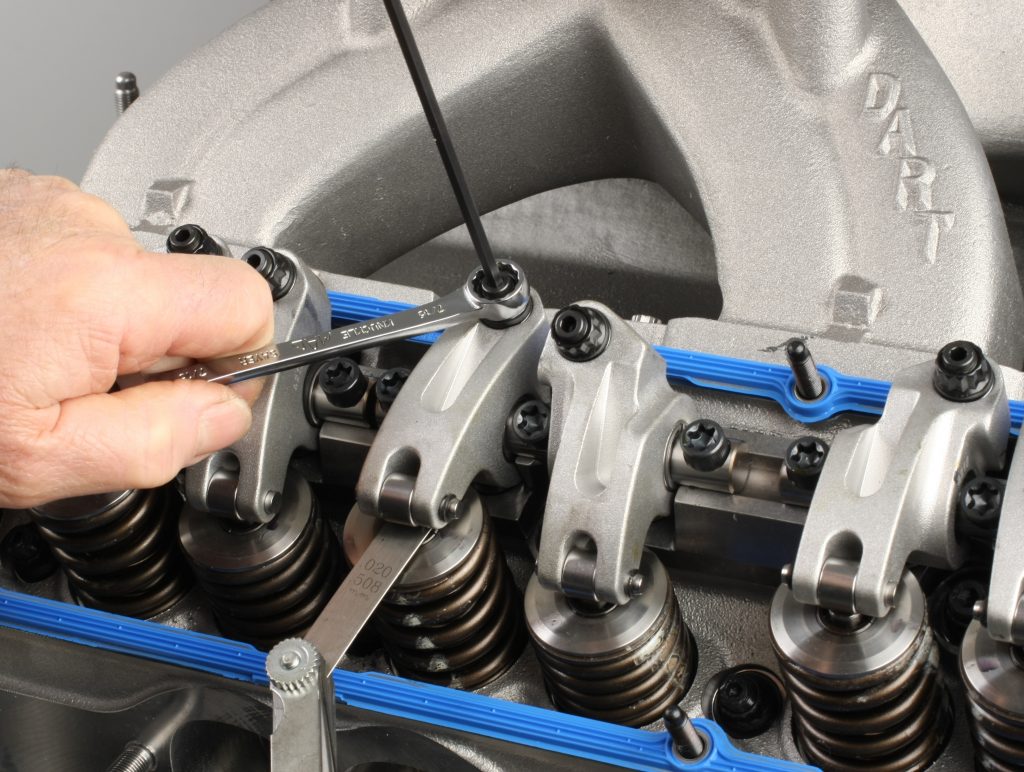
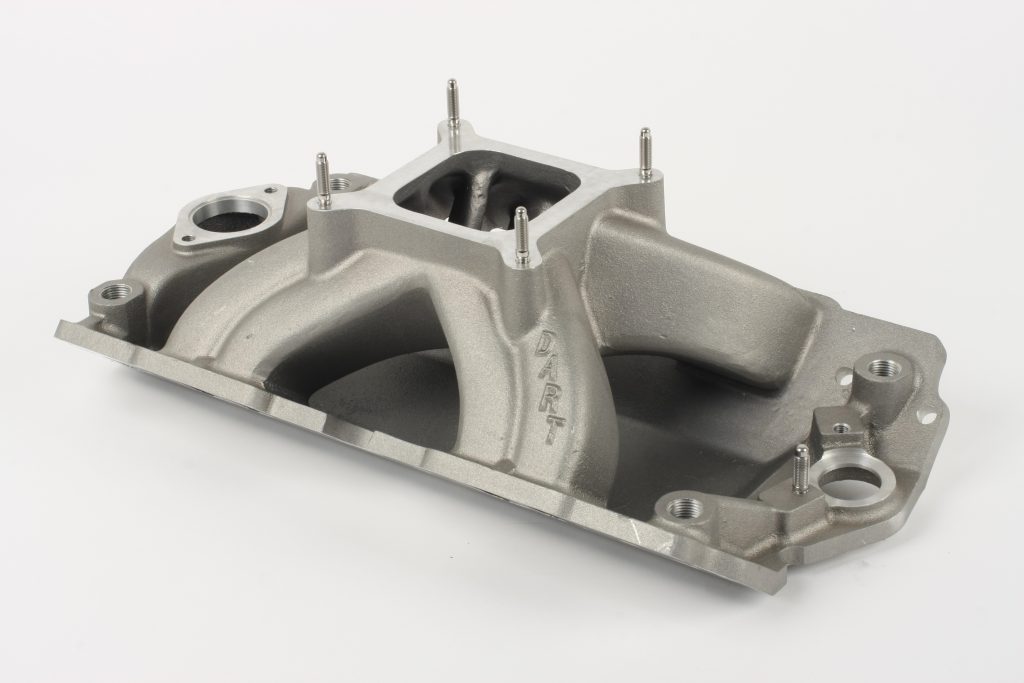
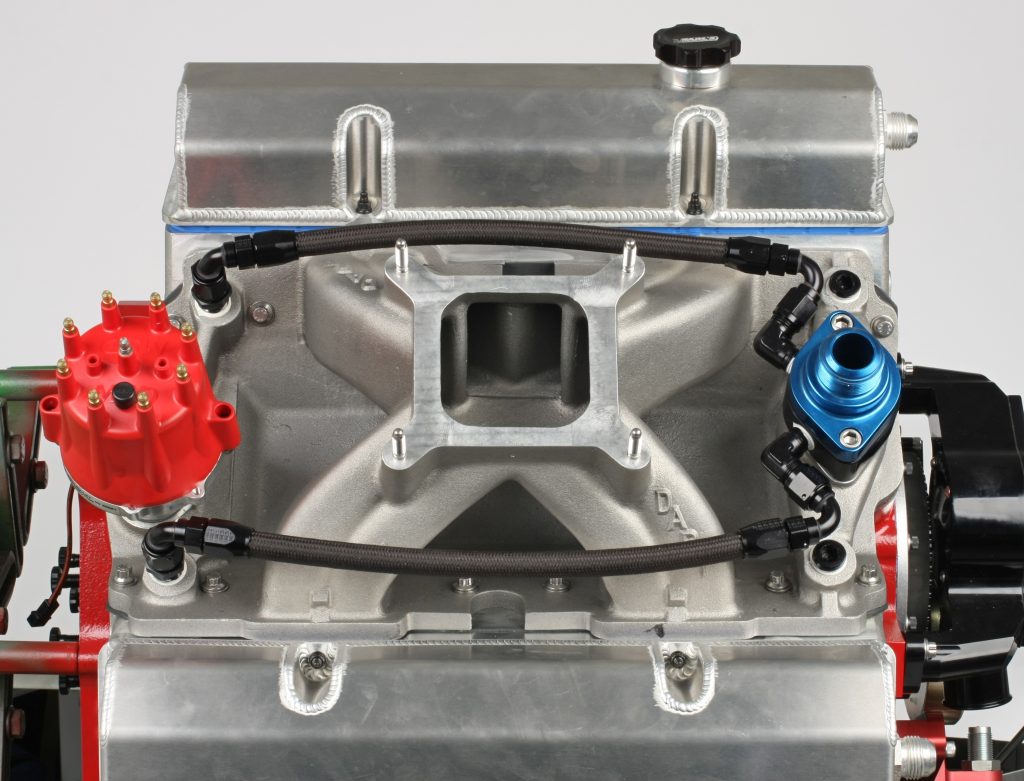
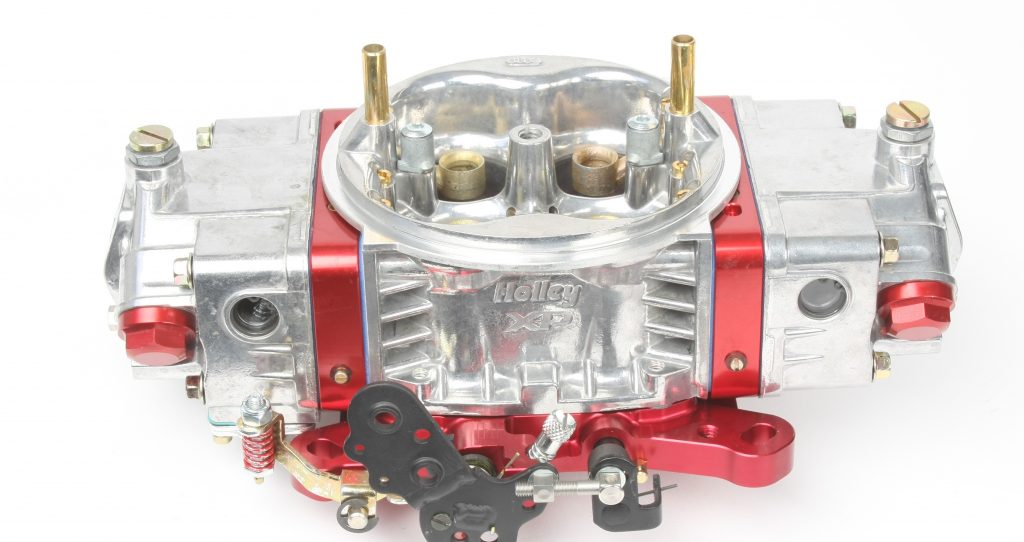
I wanna build an engine like this, Can you forward a copy of any information I need to do so. I am a rookie at building engines and I need someone to help me build this engine.
Sincerely,
David L Steinwinder II
Hey David, good news! We’ve got Part 3 of this 422 build coming up in a week or so. And when we post that story, we’ll include links to some carefully-crafted parts combos from the Summit Racing tech folks that’ll give you a nice head start on your own build–so stay tuned.