Spark plugs are a critical element of any internal combustion engine. They are the proverbial wizard’s wand that ignites the air/fuel mixture to create the glorious and mysterious magic we know as horsepower.
If we look around, there is an endless array of different plug offerings, different electrode styles, different heat ranges and even different material. To the list of different plug varieties, we can add changes in plug orientation, or more commonly known as indexing.
You may enjoy this article too: What Does Indexing Spark Plugs Mean?
Being performance enthusiasts, the question we want to know is, do these changes in spark plugs really make a difference in power?
After all, the goal of the spark plug is to ignite mixture and initiate the flame front, but can one of these changes do a better job than another? Can multiple electrodes provide multiple sparks to supercharge the ignition process? Can a wider plug gap provide greater spark energy to achieve the same result? What about plug indexing, does the direction of the spark change said result?
Well, after endless plug changes and dyno pulls, here is what we found out!
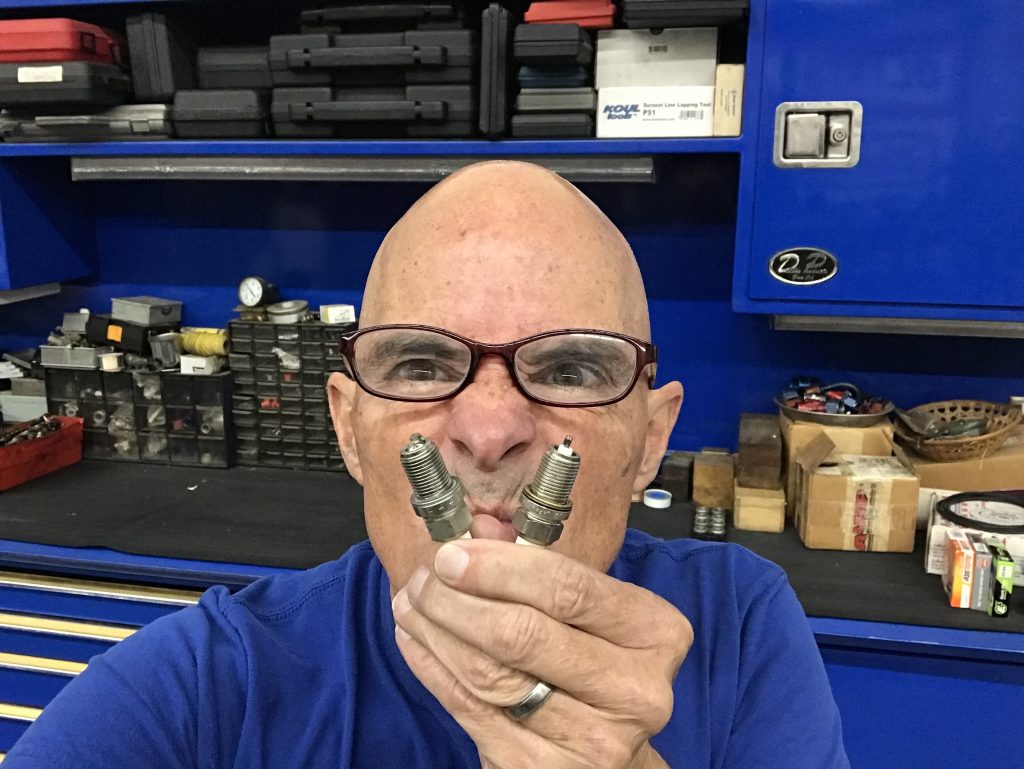
Test 1: Comparing Plug Types
In this test we ran a comparison of four different plug types on our junkyard 5.3L test motor.
The test motor was a tried and true 5.3L, but not your usual (for us) iron-block, run-of-the-mill base LM7. This test motor was of the all-aluminum variety, meaning in additional to the usual array of aluminum LS heads, this 5.3L was also sporting the very desirable aluminum block. The all-aluminum L33 5.3L was a big score from a local wrecking yard, and featured flat-top pistons (a la 4.8L), high-flow 799 heads and a slightly more aggressive cam than the base LM7 5.3L.
Over time, we had changed out the stock cam for a Red Hot cam and matching valve springs from Brian Tooley Racing, along with a FAST LSXR intake manifold and 102mm throttle body. Additional components included a set of 1-7/8 inch long-tube Hooker swap headers with collector tensions, 80-pound injectors and the Holley HP engine management system.
For this test, we ran the following spark plugs:
- Your typical Autolite copper core plugs
- A set of NGK Laser Platinum spark plugs
- E3 spark plugs with what E3 calls Diamond Fire Technology
The plugs offered changes in both material and electrode design, but all three were the same heat range. Run with these three (actually four) different plugs, there was very little difference in power (one to two hp variations). The Copper Core plugs showed a maximum difference of four horsepower in two spots, but this test showed that there is not big power to be had from changes in different styles of spark plugs.
We also ran the combination of used plugs (various heat ranges and manufacturers) that came from the wrecking yard—they produced the same power as the fancy new plugs.
Test 2: Plug Indexing & Heart Ranges
Starting with heat ranges, it should be noted that changes in the heat range of the plug are usually considered when running boost. We typically go to a colder plug when running a turbo, blower, or even nitrous, to help ward off detonation—but we did nonetheless, test the effect of heat ranges had on power on our naturally aspirated 5.3L.
In this test, we compared two sets of Denso Iridium plugs (hot heat range) Q16s to a set of (much colder) IQ31s. The IQ16s would be similar to stock heat range plugs for our NA 5.3L, while the colder IQ31s are plugs we normally run on high-boost turbo applications (like the 1,543 hp Big Bang 6.0L).
There was no significant difference in power between the two heat range plugs on our cammed 5.3L test motor.
While the motor was still on the dyno, we also tested the effect of indexing (electrode orientation) the plugs. The idea behind indexing was to aim the opening of the plug gap (and initiation point of ignition) toward a particular position in the chamber (i.e. intake valve, exhaust valve, dead space etc.). By marking the plugs externally to indicate the electrode opening and using washers, we oriented the plugs first toward the intake valve, then toward the exhaust valve, then randomly however they happen to tighten into the head with no washer. We also tried randomly moving the plugs to different cylinders.
In the end, regardless of the plug position of there was no significant (meaning measurable and repeatable) change in power.
Conclusion
Having also tested different plug gaps (reducing it down to just a 0.010 inch gap finally showed a slight change in power), we can say that on this test motor, there was not big power to be had from any of the plug changes. The winner, if any, were the cheap copper core plugs, but even that power gain would diminish over time as the copper core wore out.
The great thing about the premium plugs might not be power, but longevity, as the precious metal plugs will run for years. Some OEM recommend plug changes (with platinum) at ridiculous mileage intervals (like 100K). Copper plugs will definitely not last that long.
It should also be noted that our test motor had something many test motors do not, and that was an excellent (multi coil) ignition system. We even (as we always do) had the dwell cranked up to 4.0 ms, all but ensuring a hot (misfire free) spark. With a single coil/distributor, where misfire might be more common, curing or eliminating the misfire with one or more of these changes, could certainly yield more power, but the culprit would be the lack of power from misfire, and not the component or change itself.
The takeaway here is don’t go looking for big power gains with spark plugs unless you are curing misfire!
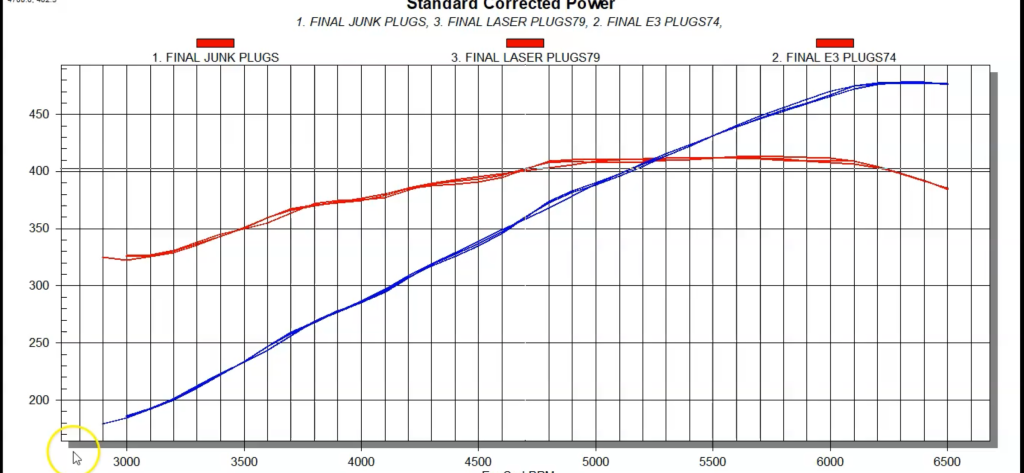
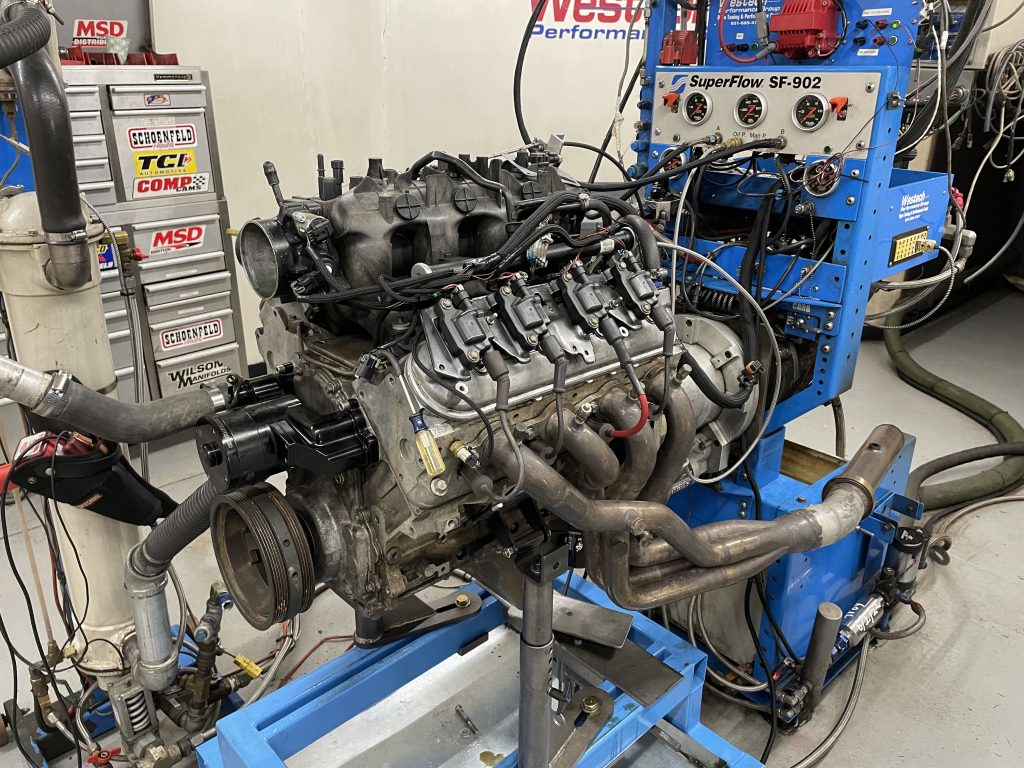
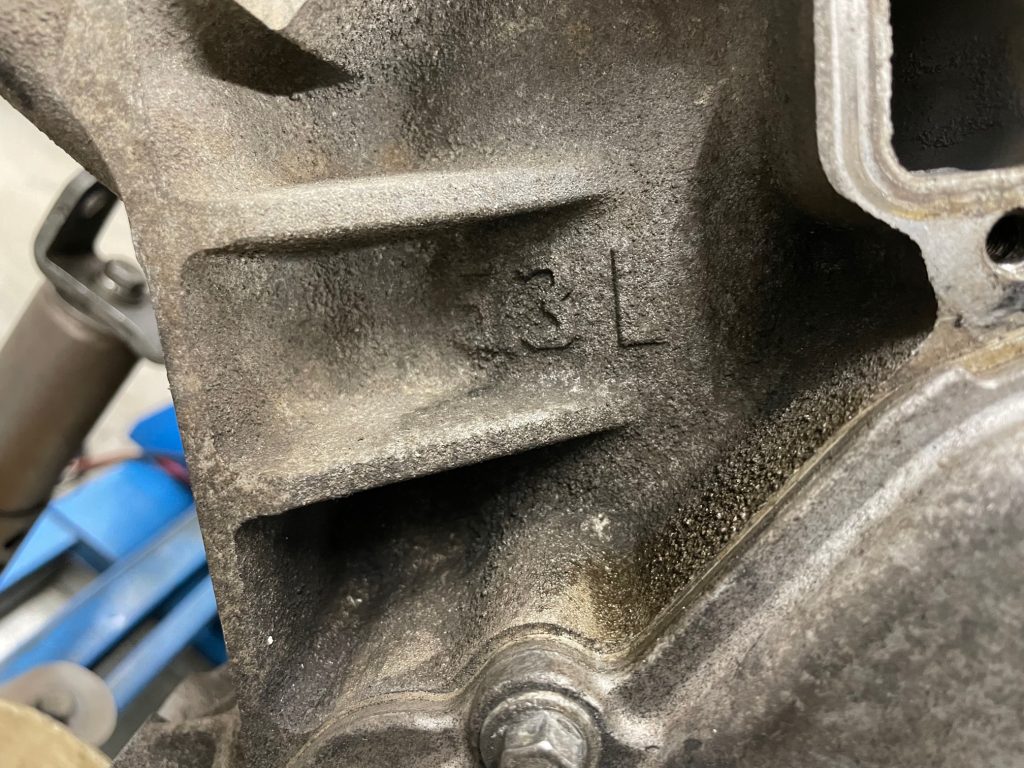
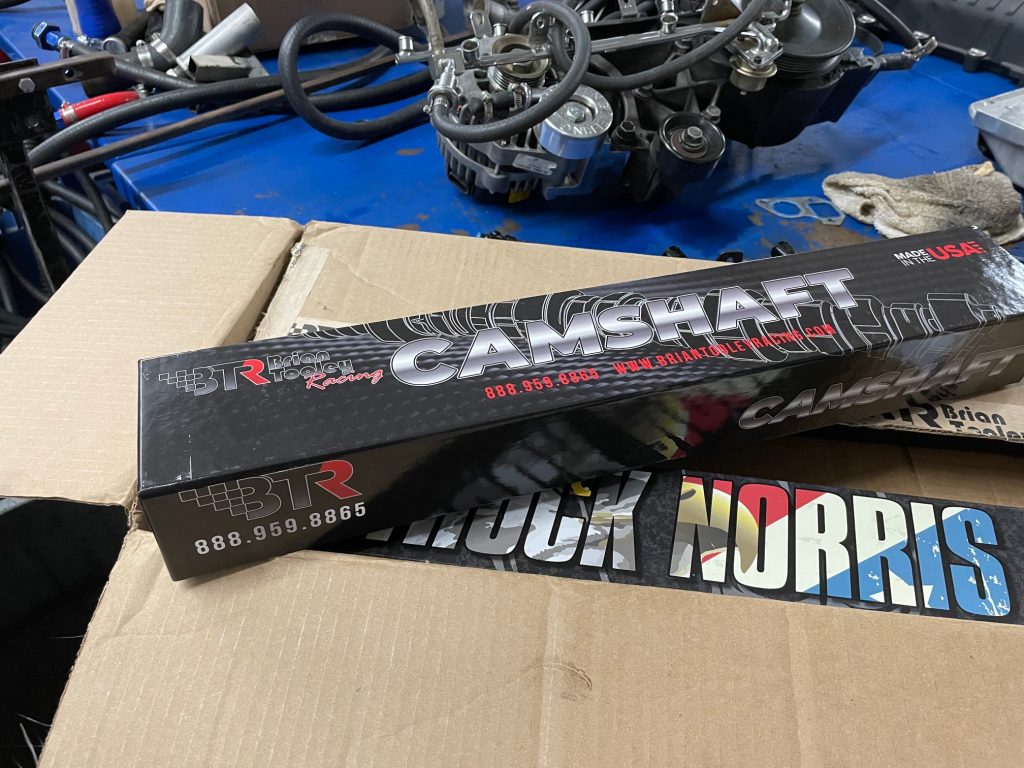
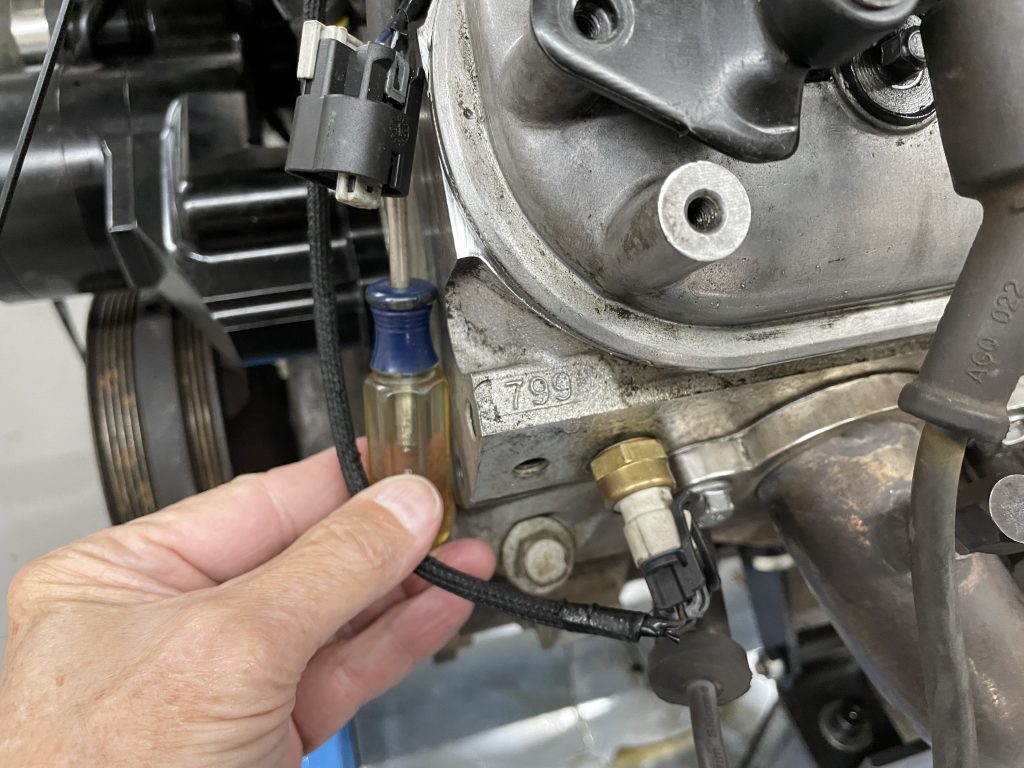
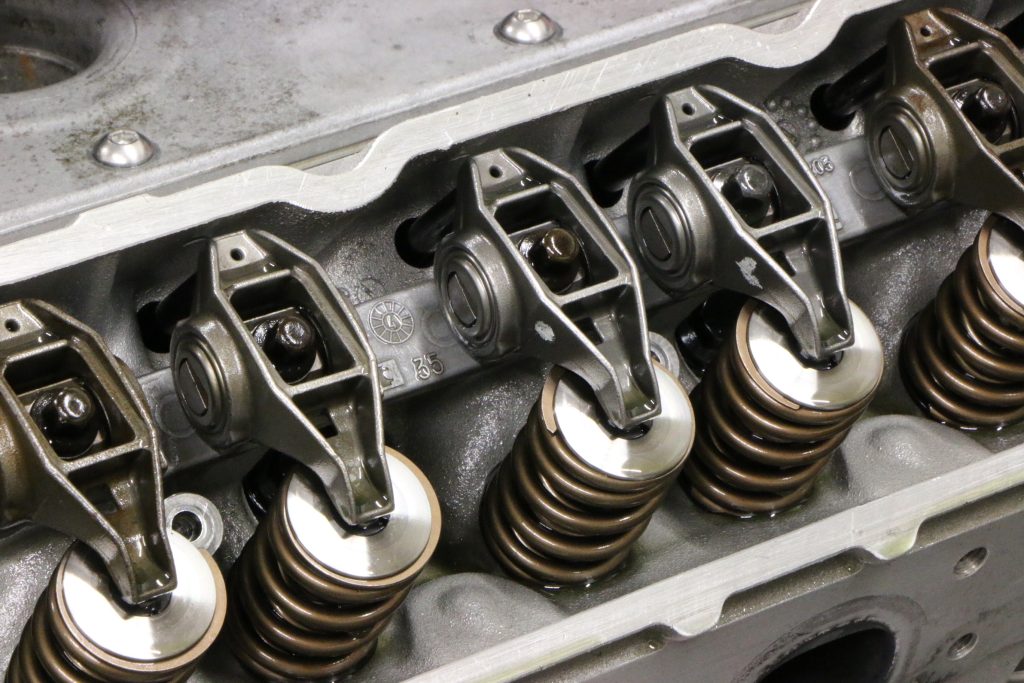
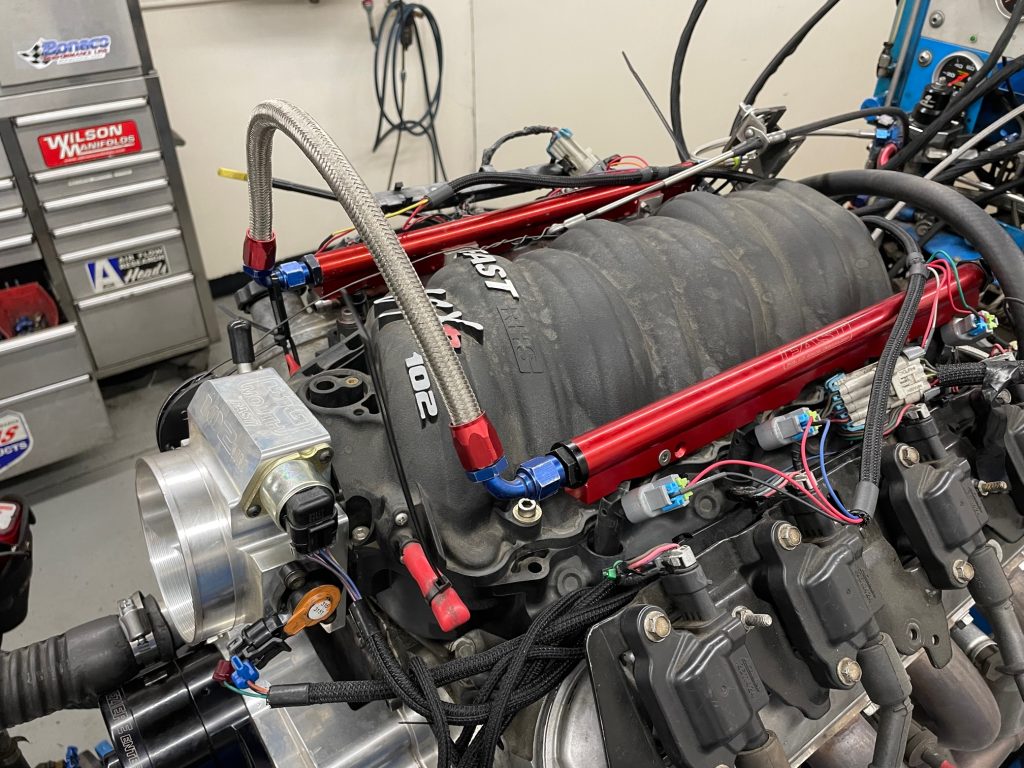
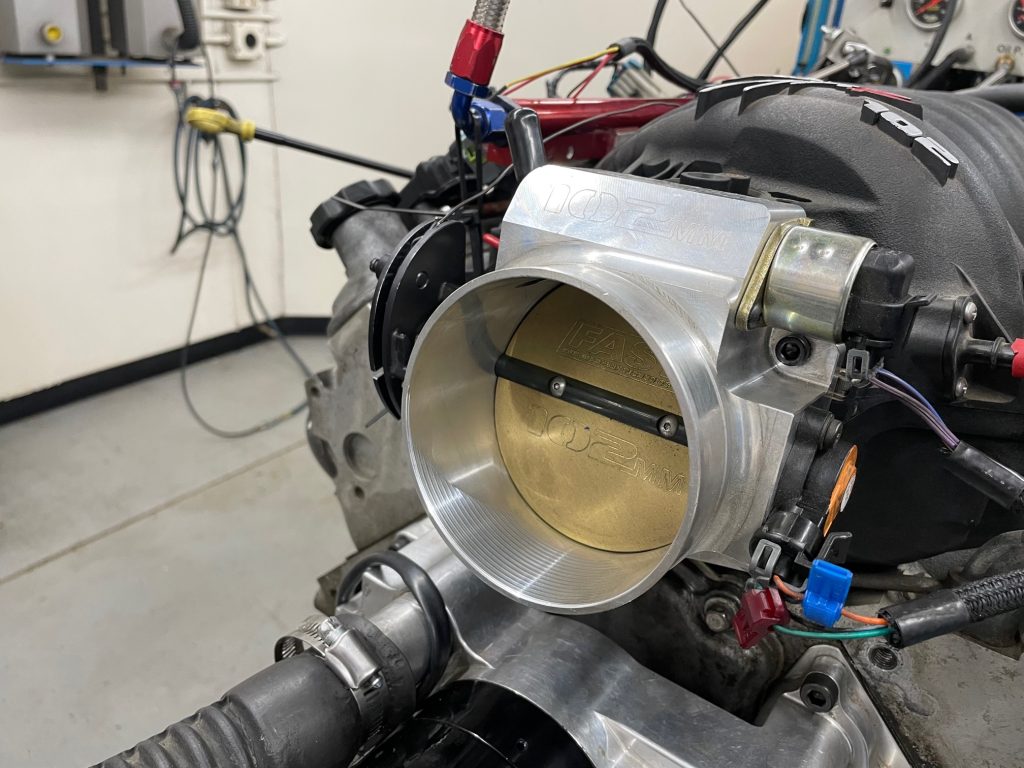
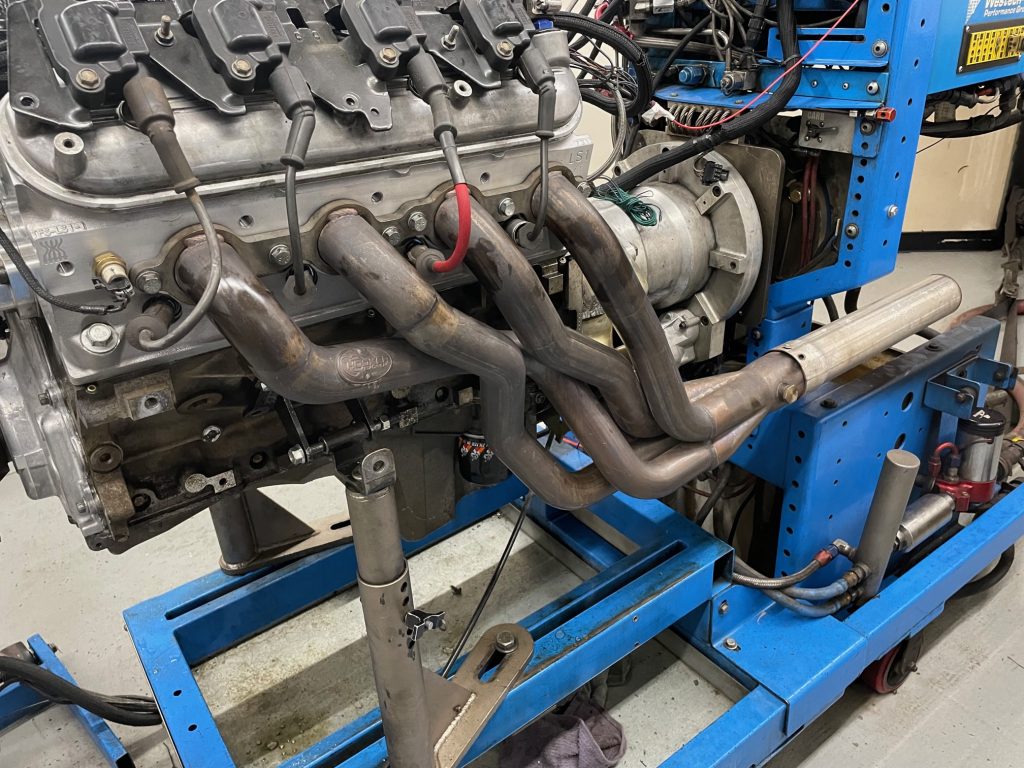
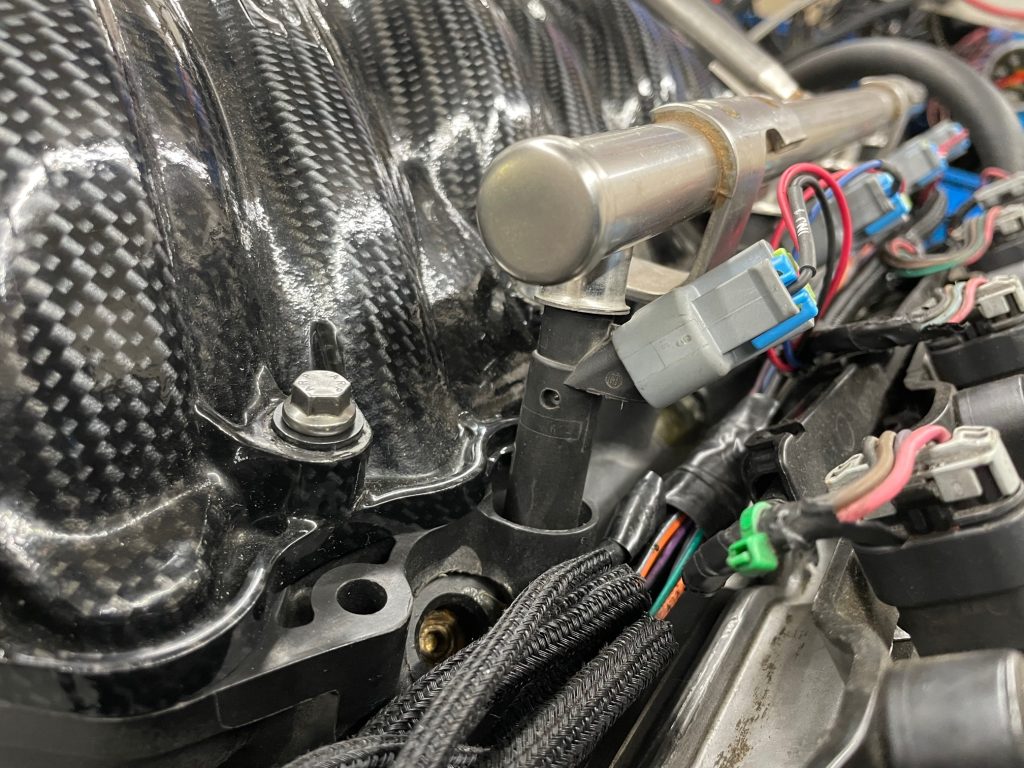
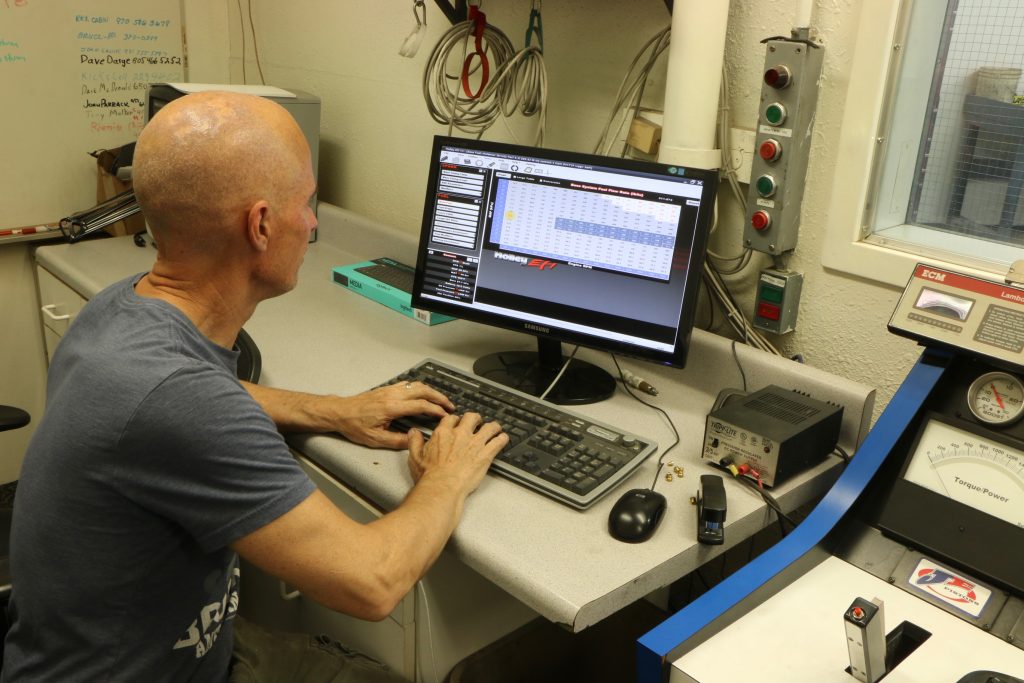
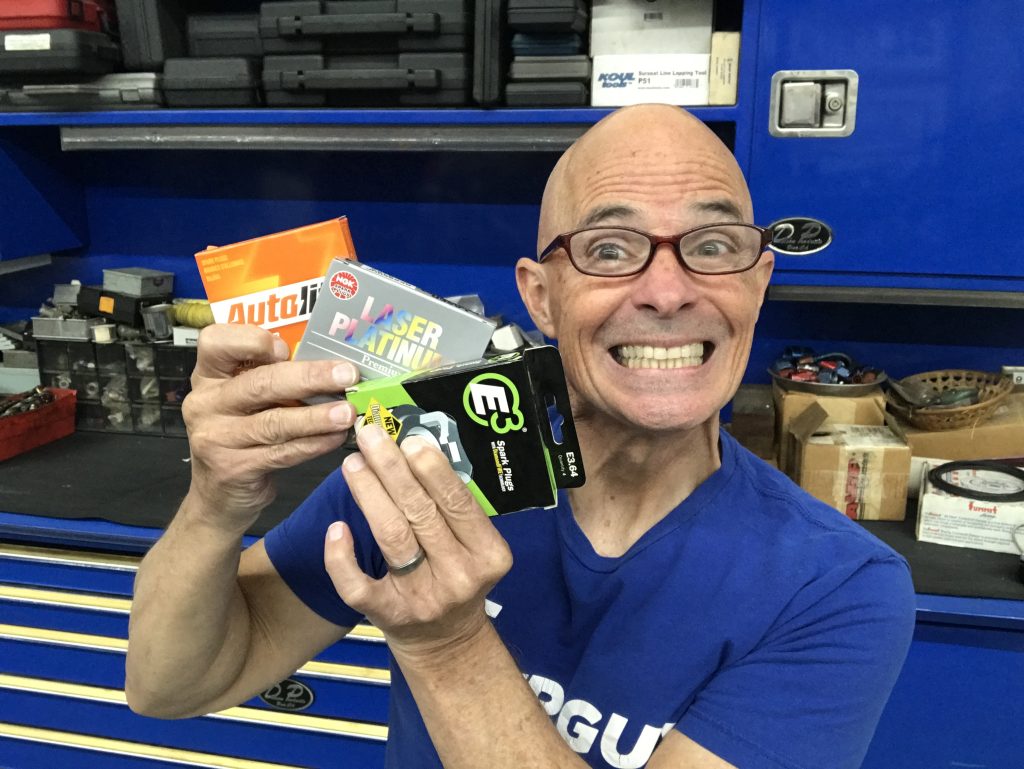
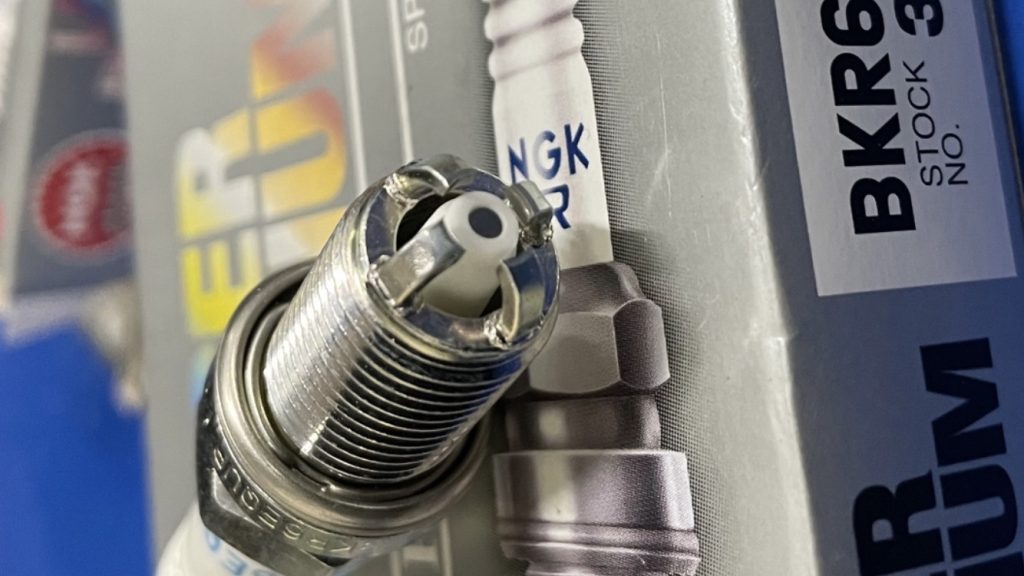
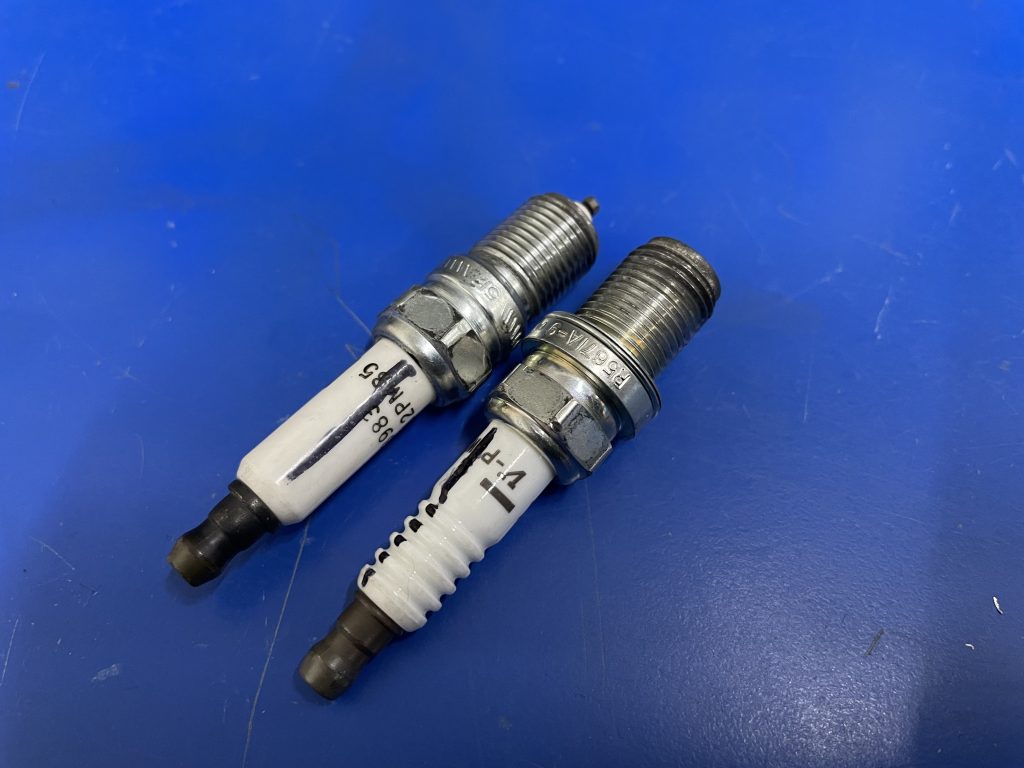
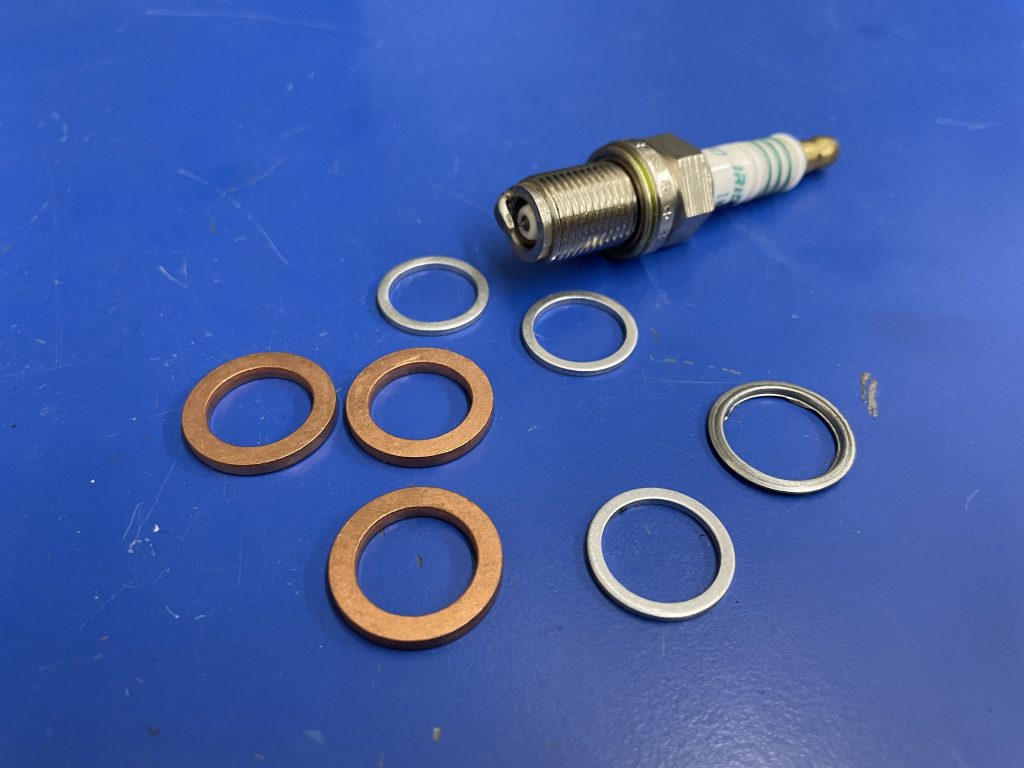
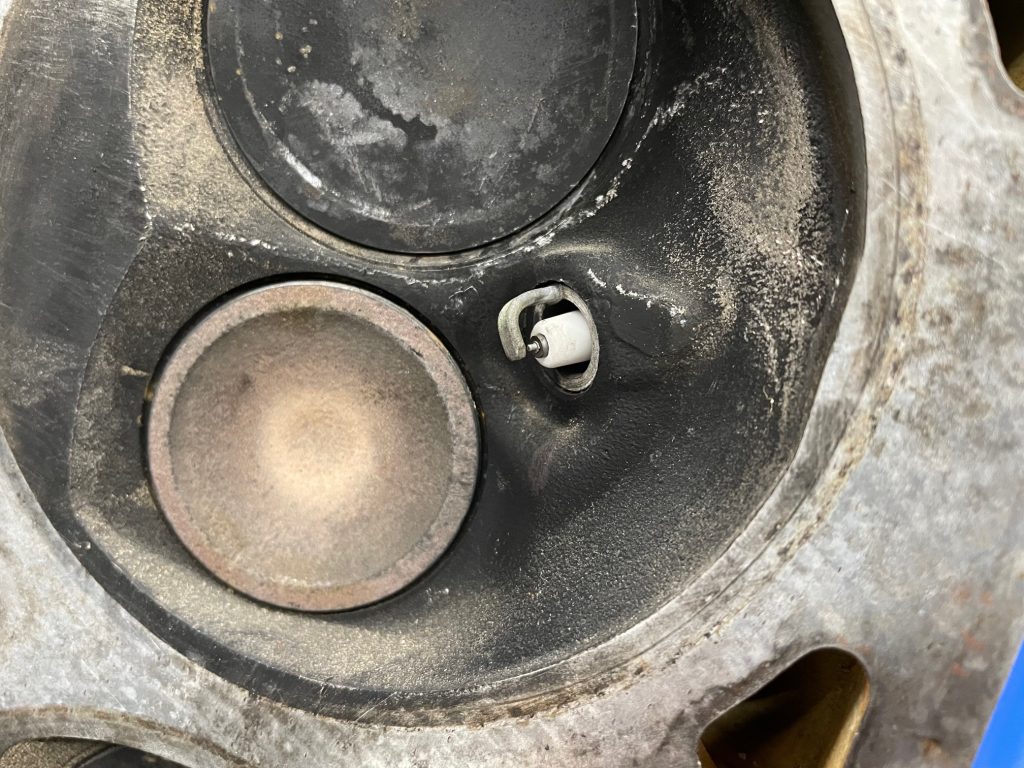
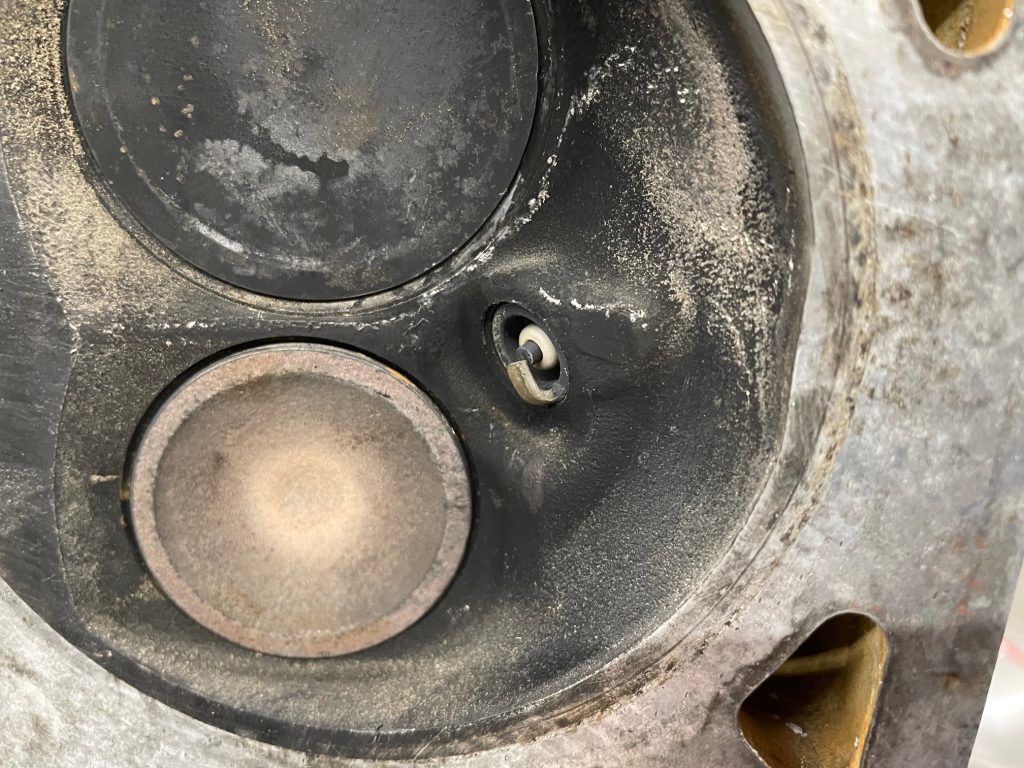
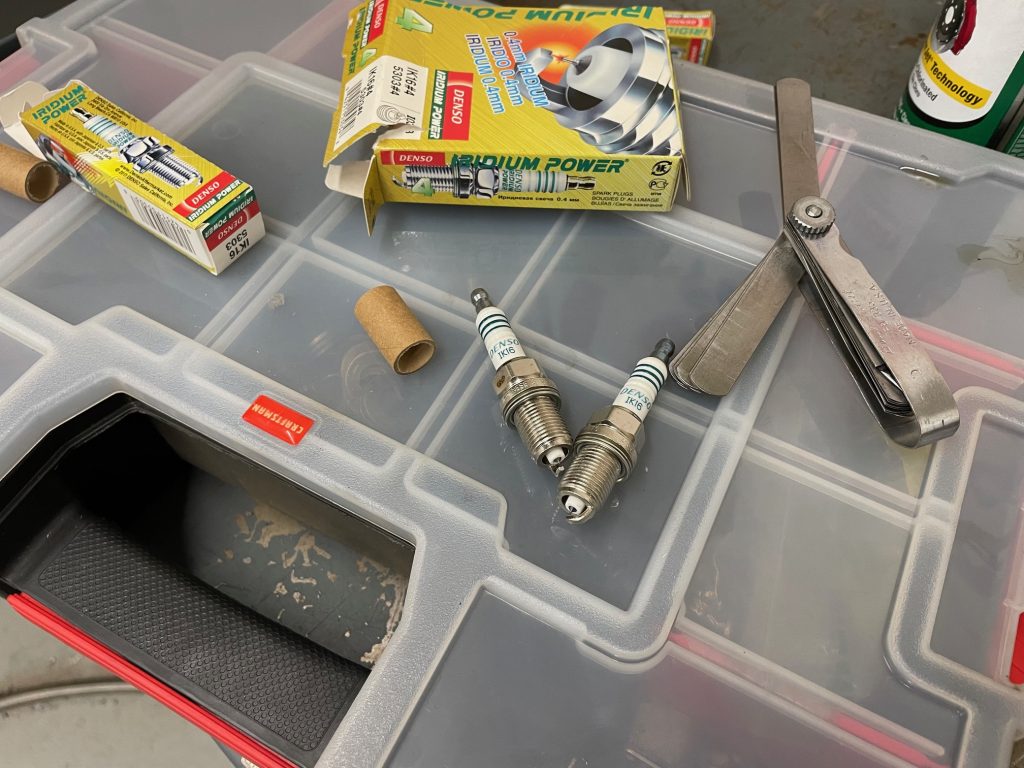
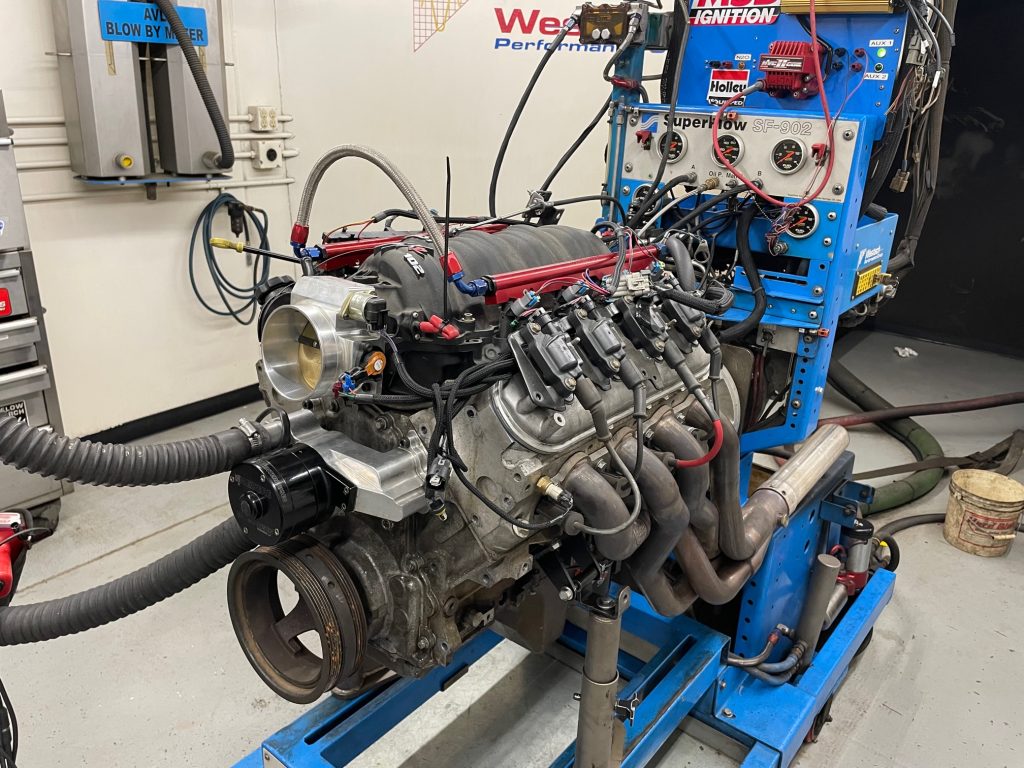
Perhaps that’s because you were using fuel injection and computer style ignition . Try that with a carb and see what you get. Computer system is designed to control the whole system and keeping everything the same, so you get what you got. If you change the fuel percentage and lock it in , then you would probably get major changes. I’ve seen guys trying to more fuel out of Carter, Rochester, junk GM carbs and using stock plugs, and missing at the top end. Then wondering what was wrong. Asking this ex parts guy what was wrong, I told them to get colder plugs, ( two steps down), or change to a Holley carb . Since they didn’t want to change carb, I hunted down some old plugs from some other racers. I J gaped them and no other changes, they ran thru the lights without missing. Now they could rejet the carb to run better.
100K on spark plugs.
I’ve ran the stock style iridium spark plugs over 100K miles with no problems. On my 2005 GMC with a stock L33 with stock ignition coils the ground electrode had cooked away, opening the gap to nearly .080 but I was not experiencing any significant misfire. I’ve routinely ran plugs 100K miles on all my vehicles, often with no significant plug wear, even on my 1995 Ford with a 351W. When I replaced the 100K mile plugs on my other GMC pickup with a LM7 Vin code T engine, it was a complete waste of time and money, the plugs looked great.