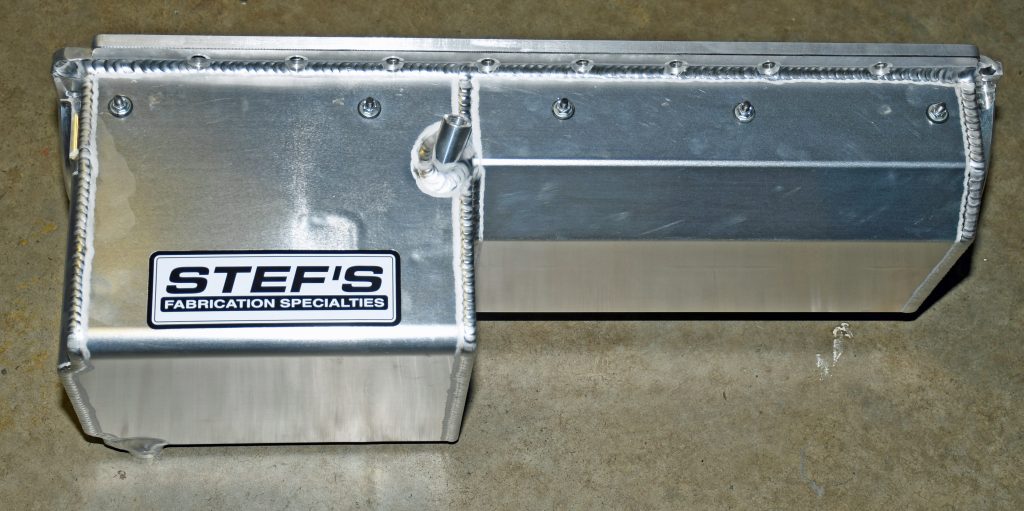
In drag racing, the most common oiling systems are wet sump arrangements. Virtually every Stocker and Super Stocker uses one, and so do plenty of Super Class cars and Competition Eliminator cars, along with countless bracket cars. And we’re not even taking into consideration the virtual plethora of fast street cars (not to mention any number of street-strip machines). They’re also used with certain exclusivity in production line cars.
After all, wet sump systems are relatively inexpensive, uncomplicated and, for the most part, do the job they were designed for. Unfortunately, wet sump oiling systems aren’t perfect. That’s why so many unlimited cars in all forms of racing incorporate rather expensive (and often equally complex) dry sump systems.
One of the biggest drawbacks in a wet sump oiling system is the physical control of the lubricant. When the car moves, the oil moves. That means when you hit the throttle, the oil rushes to the back wall of the oil pan and sometimes tries to climb up the back of the engine block. When you hit the brakes, the oil surges to the nose of the pan, often draining the sump in the process.
Drag racing amplifies the dilemma.
How? That’s easy. Each time you perform a burnout, the oil moves rearward. Then, as you hit the brakes, it moves abruptly forward. If you race in an index or break out category, there’s always the possibility of hitting the brakes hard at the big end of the track. The results are usually quite predictable: An empty or near empty sump (there’s reason for this, and we’ll get into it below) and an oil pressure gauge making an abrupt swing to the left.
The traditional way to control this oil migration is the installation of swinging trap doors and baffles inside the pan. They work more or less, but in many instances, they’re just a Band-Aid (particularly if the trap door configuration proves inefficient). When the Band-Aid doesn’t work, then one thing happens: The oil pressure gauge drops like a rock. Bearings run dry.
And eventually, your wallet becomes lighter—often much lighter.
So what’s the fix? A very well-designed pan is a huge part of the solution. But how does one get there? Instead of simply mimicking what worked (or works) in a dry sump, STEF’S Fabrication Specialties took a different path: They embarked upon a dedicated R&D program for wet sump systems. And they’ve been at it for decades. To be quite honest, the mechanical aspect of modern oil pan design is still considered by some as more of a black art than a science. Part of the reason is one can design and construct a rather crafty oil pan configuration, bolt the pan on a dyno (test) engine and with any kind of luck, see immediate gains.
But a dyno test is static. The engine doesn’t move. In a car, it does, moving with the vehicle as it accelerates, stops or turns. Depending upon the application, this creates an entirely new set of variables since the oil is moving too—a lot. At any given moment in a stock, unmodified engine, there might be one quart of oil stuck in the valvetrain and lifter valley, one quart in the filter, another quart thrashing around in the crankcase, and perhaps one quart glued to the crank and reciprocating assembly (the oil “rope effect”). Now, if you’ve been counting, in a common wet sump application, there could conceivably be less than one quart of oil in the crankcase or oil pan.
It’s easy to see, if you can control the oil, you can gain reliability. And with it, maybe some power.
According to STEF’S Joe Stefanacci, the purpose of the assortment of baffles, trap doors and internal ledges found in a modern high-performance pan is simple: They’re all designed to direct the returning oil to the area of the pickup.
Is there an advantage to having a full length, full depth oil pan in a wet sump application? According to the experts, most definitely yes. The further the floor of the pan is moved away from the spinning reciprocating assembly, the more power the engine will make. If the floor is close to the crank, it stands to reason, the ricocheting oil will bounce back toward the crank. Unfortunately, the use of a full depth pan is often restricted by the engine cradle or front suspension cross member in a door car application.
Many sportsman racers make every effort to open the area under the engine by heavily modifying the engine cradle. By accomplishing this, then the pan size can be increased, and horsepower goes up. In most Super Stock-style drag cars where engine cradle mods are common, it is still necessary to notch or slope the forward edge of the pan to allow for engine installation and removal. Also keep in mind that a number of vintage rear-steer vehicle applications require a tube inside the pan to accommodate the steering linkage. Obviously, in the case of a street driven car, some concessions must be made in the oil pan design in order to allow for cross member clearance.
One Way Valves
One place where STEF’S has re-thought the modern oil pan involves the swinging trap door arrangement that’s common in many aftermarket pans. Instead of using a swinging door, they’ve come up with a series of internal oil pan “surge baffles” to combat oil migration.
Those baffles or “valves” are a rubber composite arrangement and they work much like a two-stroke reed valve setup. As oil moves rearward in the pan toward the sump, the valves open. Oil can freely flow into the sump, but because the valves are designed to be one-way only, the oil cannot migrate forward. In testing, STEF’S discovered that the conventional trap doors do slow down the movement of oil from the rear of the pan, but a considerable amount of lubricant still manages to escape, theoretically by way of partially open doors. This research led to the development of this surge baffle system, which positively shuts off the flow of oil out of the sump area. This allows all of the oil to remain in the sump during braking, which in turn, allows the engine to maintain oil pressure.
In place of the traditional swinging trap door at the forward edge of the oil pan sump, STEF’S devised a system where five large one way surge baffles or “valves” are installed in place of the trap door. Under hard braking, the flexible valves remain closed. When the valves are seated, a positive seal is created, and there is no way for oil to move away from the sump. Under acceleration, the valves open, allowing oil to freely move into the sump area of the pan.
Essentially, this is a simple solution to an old problem. But the execution may have proven much more difficult than the brainstorm. STEF’S had to come up with baffles that were of the right mass to offset the weight of the oil. Too heavy and they might not react quickly enough. Too light and the forces of oil would overcome them. They also had to figure out a way to keep the rubber check valves or surge baffles positively in place. Finally, they had to work out an arrangement where the surge baffles could be positively seated.
How they accomplished this was to build an additional wall inside the sump. In the design, the new pan baffle arrangement took the place of the final swinging trap door baffle in the oil pan. A bulkhead of sorts was engineered, and five valves were affixed to the piece.
Windage Trays & Scrapers
Windage tray use, and the type of tray incorporated within the pan vary with the application. STEF’S has done away with solid (and louvered) windage trays in many of their oil pans. In their place either a special expanded metal, Teflon-coated, uni-directional screen or a stainless mesh tray is used. In many popular wet sump pan configurations, the tray is fitted to the passenger side of the oil pan. This special screen features openings that are shaped like small wipers. The oil is directed through the openings but it cannot come back out through the screen. As a result, any oil droplets or oil spheres that bounce toward the screen cannot return to beat on the rotating crankshaft assembly.
In some cases, these screens cover the full length of the kickout, but also cover slightly more than half of the pan ahead of the sump. STEF’S research has determined that the spinning crank forms a low-pressure area in the kickout. This low-pressure area (much of which is covered by the screen) literally vacuums the oil from the rotating mass. Because of this, there is often no need for an added crankshaft scraper assembly. What about the driver’s side of the pan where there is no screen or windage tray? This portion of the pan sees little if any oil turbulence, and is in effect, a high-pressure area in the sump.
Certain oil pans constructed by various manufacturers still make use of a crank scraper. Scrapers become more common when a large passenger side kickout cannot be included in the pan design or when the pan cannot be effectively built to take full advantage of high and low-pressure areas within the sump. Most often, those pans make use of a solid crankshaft wiper bolted to the oil pan or to the pan rail. You can, in some cases, find a pan built with the scraper integrated into the oil pan rail. This is only possible with short stroke engines. With very long stroke combinations (especially those with bulky aluminum rods), the demand for reciprocating component clearance eliminates the possibility of using a crankshaft scraper.
Depending upon the design, some scrapers must be hand fit to special engine combinations that incorporate large connecting rods or increased stroke cranks. In many cases, this hand fitting tends to be tedious. Some scraper designs require no additional hand fitting, but without a tight fit to the reciprocating components, the scraper can’t be very effective.
Kickout Or Not?
Kickouts work great. No question. But in some situations, a kickout just doesn’t work. Why not? In one word: Fit.
The writer’s BBC-powered Nova is a good example. The 2-1/4 inch tube headers I have from Lemons simply do not allow room for a kickout. As it turns out, STEF’S “Econo” pans are designed exactly for this type of application. They’re crafted without kickouts. To be perfectly honest, in some applications, there’s power in a kickout. There are, however a couple of other things that help make power inside the oil pan: Keep the oil as far from the crankshaft as possible and use a larger pan so that you provide room to increase the area for crankcase pressure to dissipate.
As you can see, there’s a lot to these oil pans. The STEF’S “Econo Series” oil pans have nothing to do with corner cutting. Instead, they’re high-quality pans that don’t necessarily have all of the latest bells and whistles. Instead, they’re designed to fit OEM chassis without cut out (modified) crossmembers. But in terms of fabrication quality, they’re right up there with the custom fabricated race examples offered by STEF’S. Certainly the STEF’S crew hasn’t followed the beaten path when it comes to oil pan design and manufacturer. The innovations are plenty, but as you can see, there’s also plenty of merit—particularly when it comes to engine longevity. For a closer look, check out the accompanying photos:
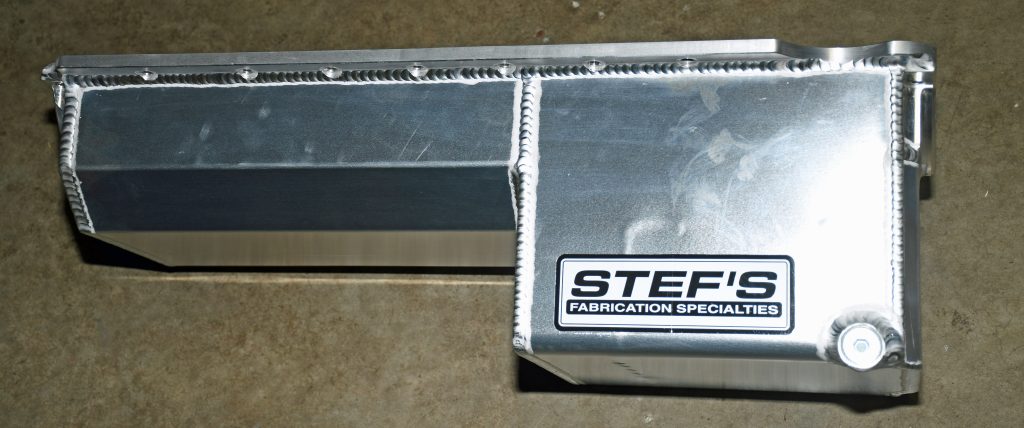
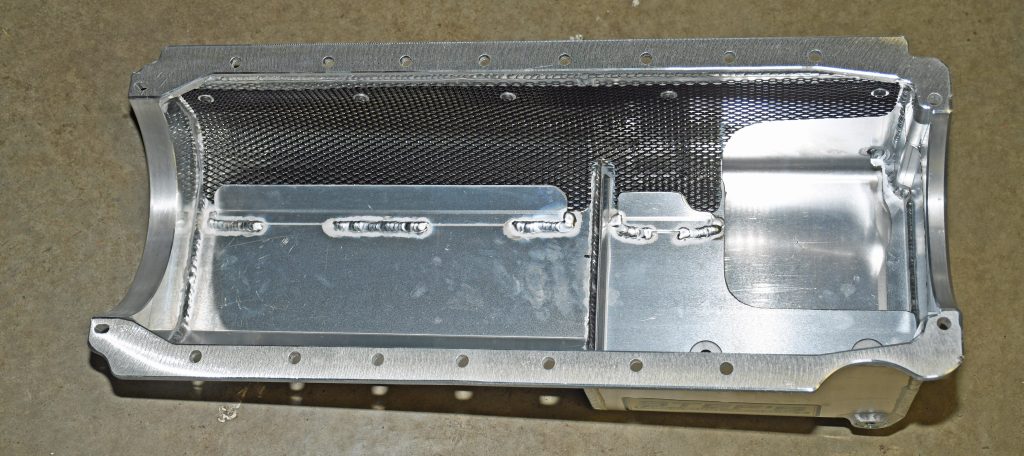
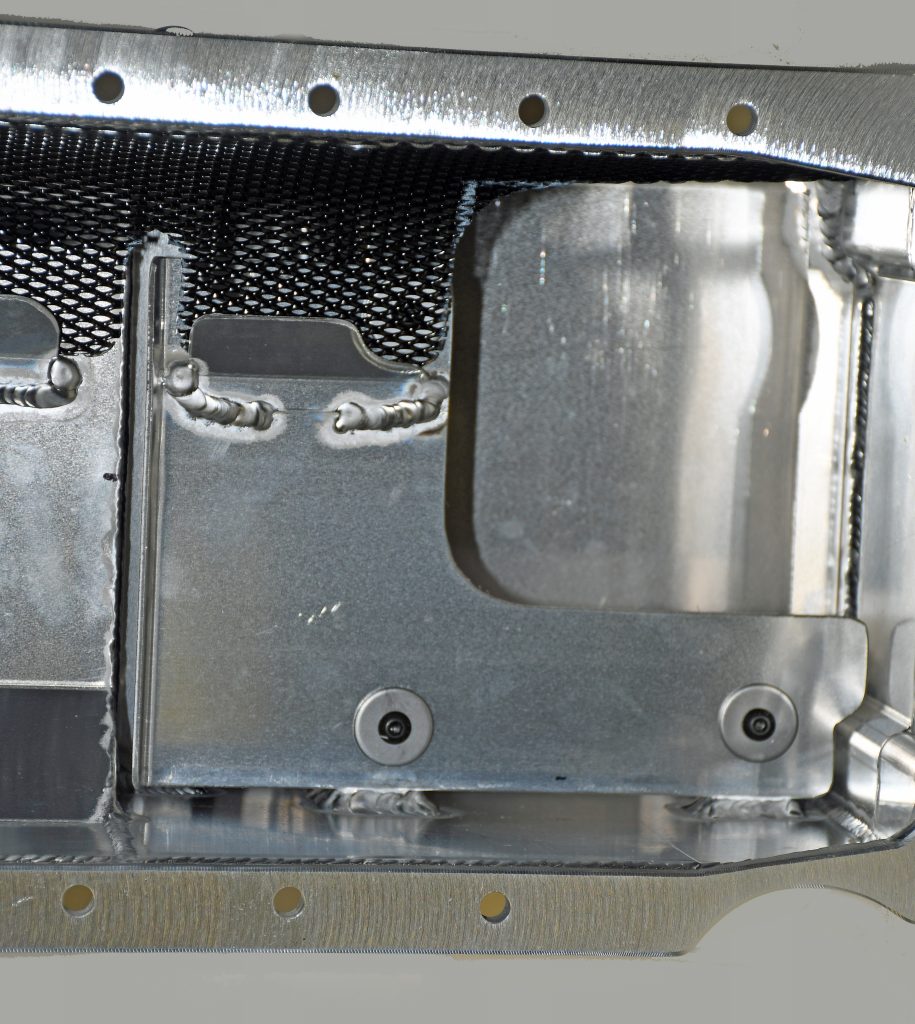
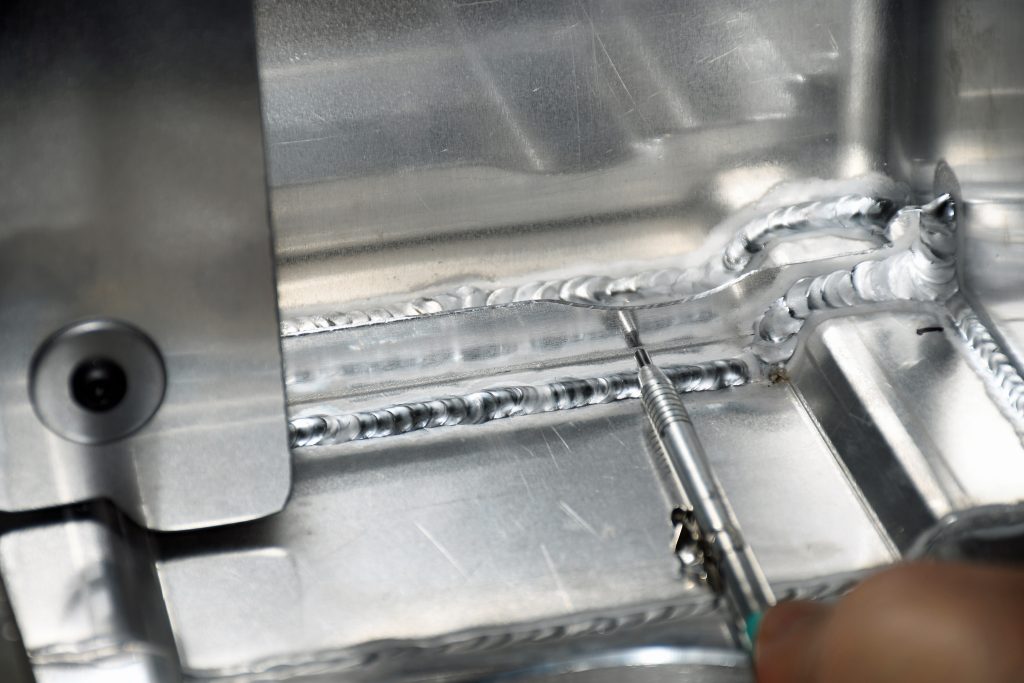
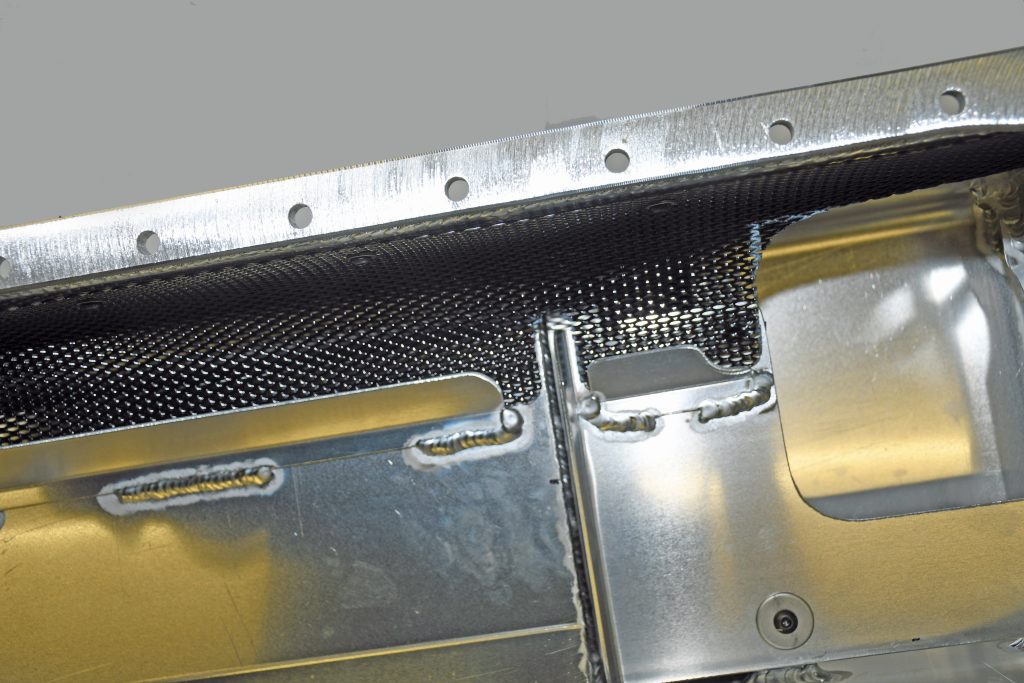
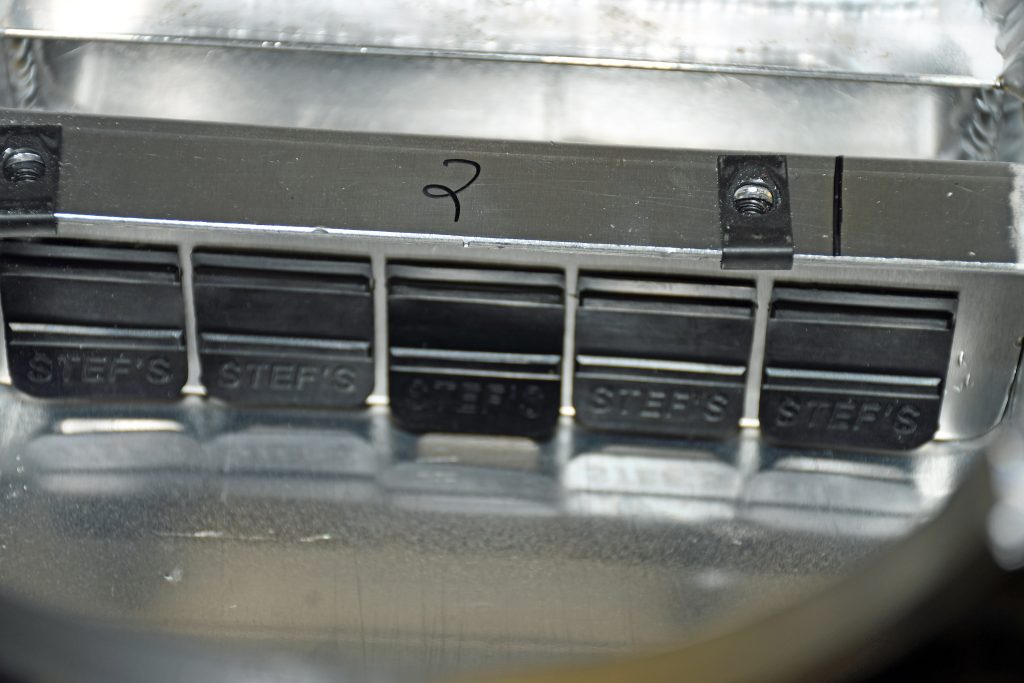
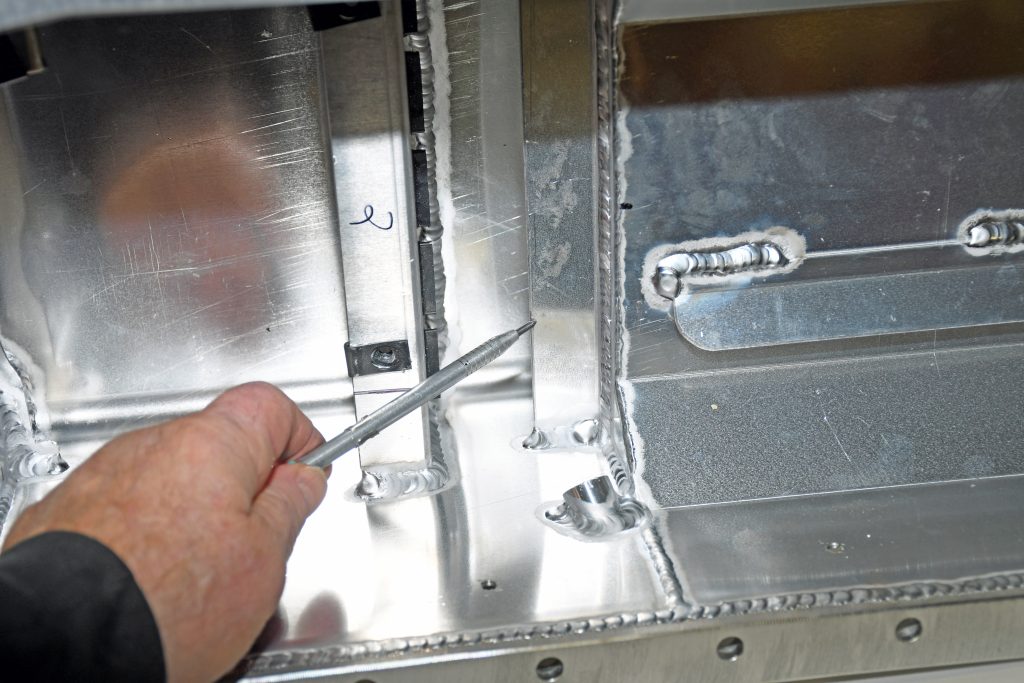
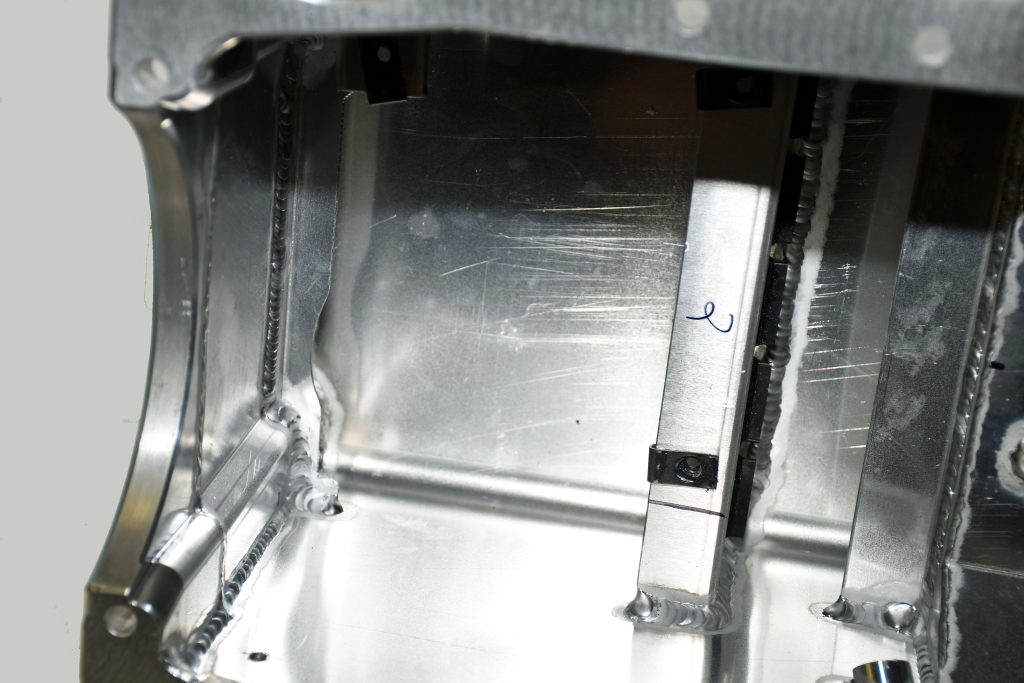
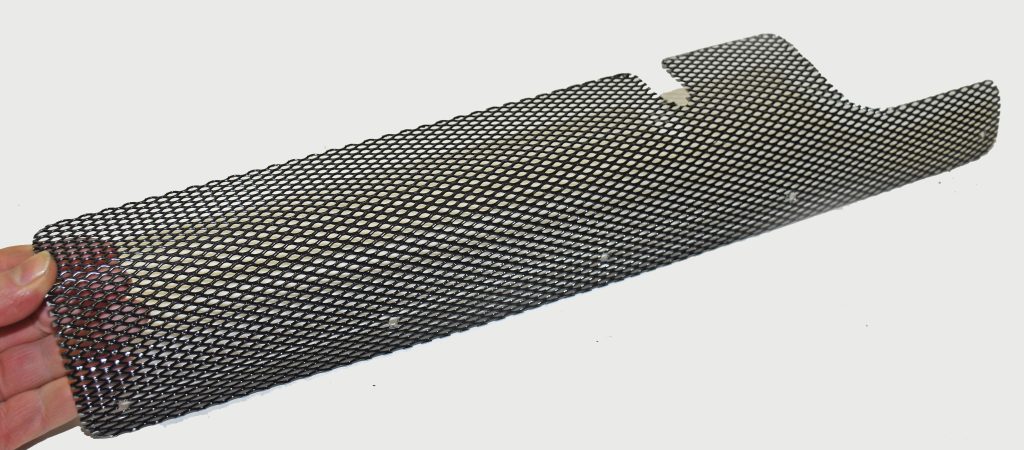
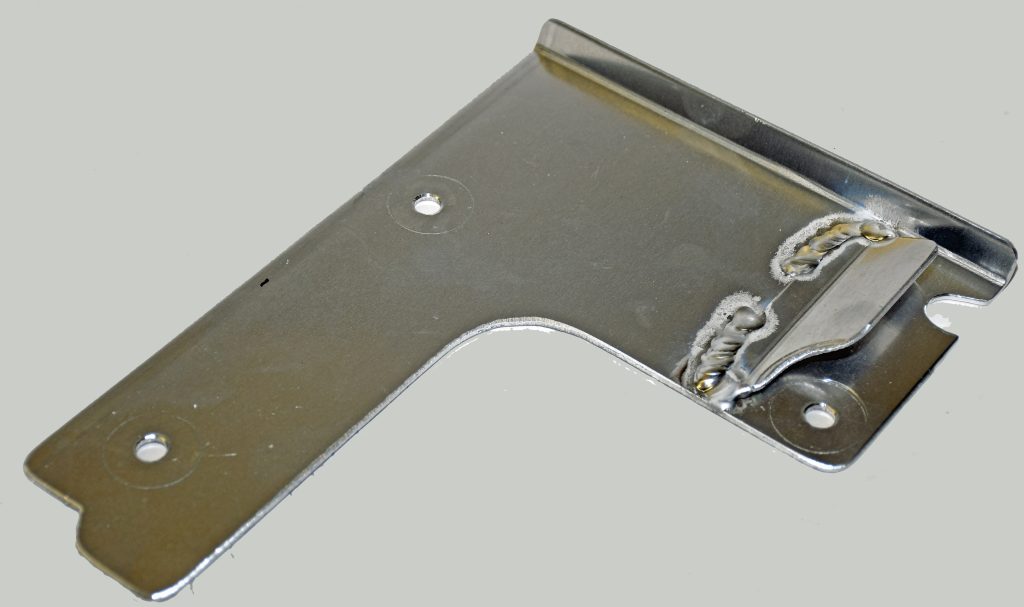
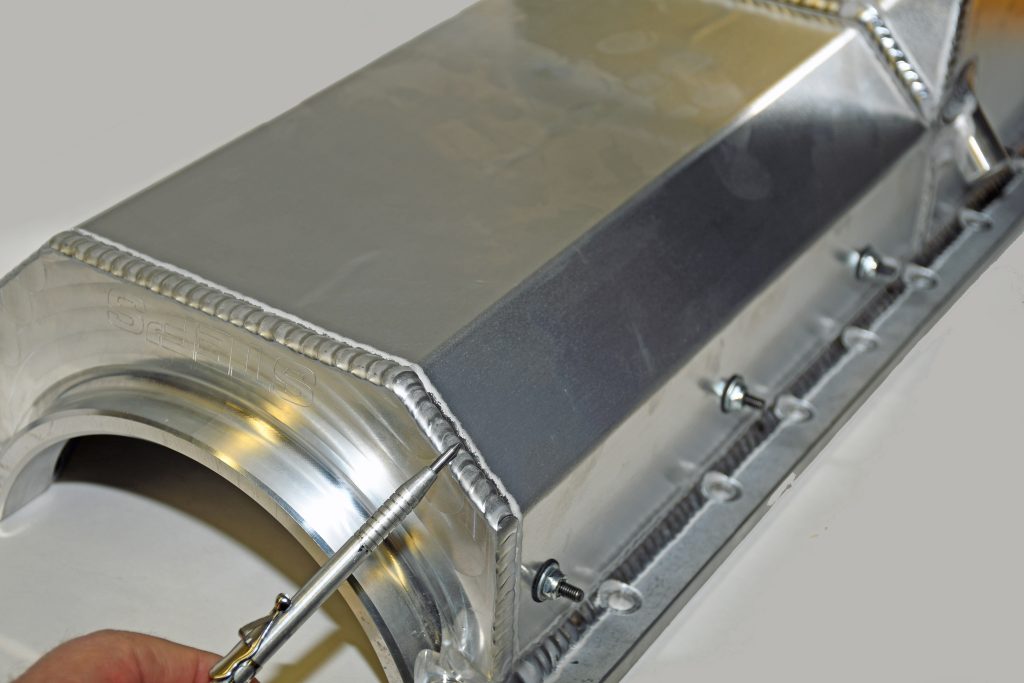

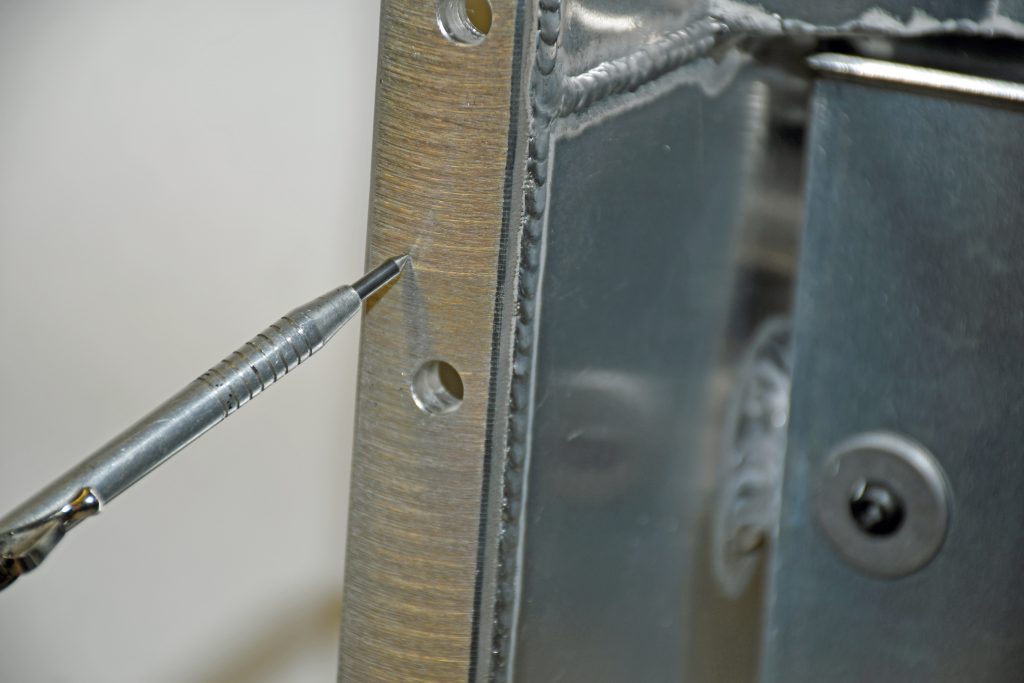
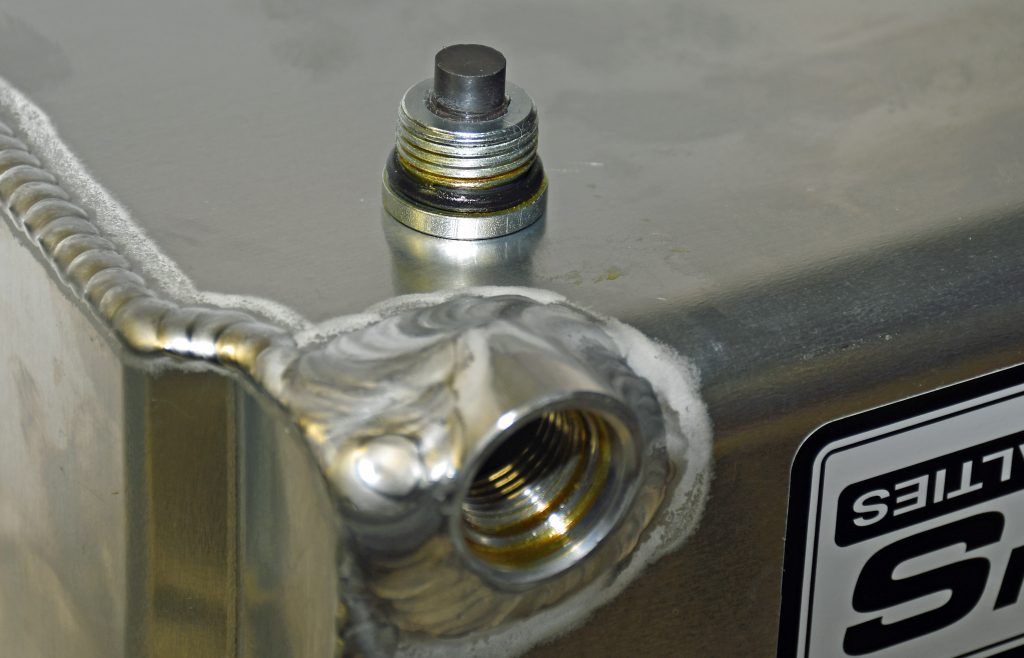
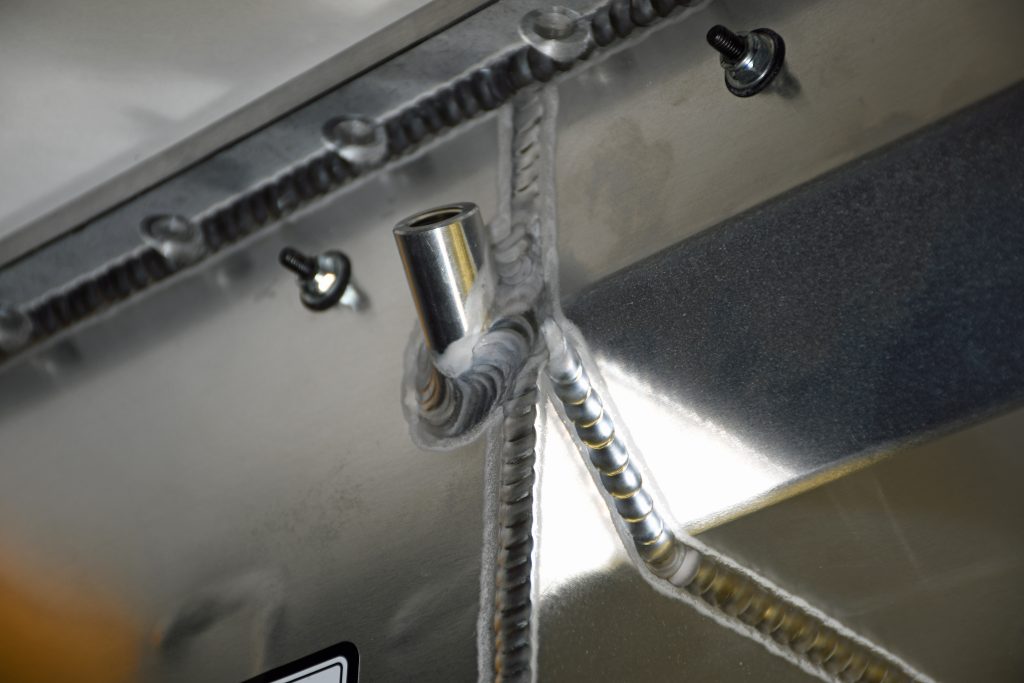
Hello good day I am interested in one of the oil pans for a big block 454 Chevy
Hello Rassie, you can see all of Stef’s oil pans for the Mark IV Big Block Chevy here.
How many quarts do the econo pans hold?
Hey Alan, it depends on the application. But many hold between 6 and 7 quarts.
What is the part number of the pan shown? Do you know what the rear sump dimensions are? Mainly the length and width
The part number is Stef’s 1041DE. (It’s currently not in stock and is a special order.)
…
This is a Chevy Mark IV style pan with a Stroker notch, without oil pump. The “D” stands for Dipstick provision; it does not include the dipstick. The “E” stands for Camaro (+ Chevelle & Nova) notch.
…
The pan has a depth of 8 inches at the sump. The sump measures approximately 10 X 8 inches.
…
And by the way, it’s a spectacular piece!
Hi I am interested in a bbc 43/4 stroke oil pan for dragster. It has aftermarket dart block with clearance for full length oil pan with kick out Motor has 1350 hp and turns 8000 rpm. My current problem is hard breaking I loose oil pressure down to zero . I also think I am loosing hp due to windage. Current pan holds 7 litres plus filter Can you recommend a pan that will solve my issues
The pan in your article and similar pans like the Stefs 1070 needs to be rethought! The baffles, doors, trays, etc are useless if the oil can’t get back to the sump! Most engines/chassis require a 3 degree lay back for correct driveline angles AND a level carb pad as most intakes such as edelbrock, Holley etc. reflect this. These front sump stefs pans like the 1070 do not.
2/3 of oil in the engine drain backs in the lifter valley drain over the shallow section of the pans. The pans have no taper from the shallow 2/3 section of the rear of pan and it holds the oil so it cannot return to the front sump, it then gets wipped in the crank. Acceleration amplifies this and you have oil starvation. IMO these style pans are for a show car cruiser that sees no hard acceleration.
currently have a professionally built engine with over 10,000 invested that is back apart for oil starvation . Oil pressure would drop off as soon as you dropped a gear. Added an extra quart of oil and that helped the initial hit but would drop oil pressure at about 4800 rpm and had to get out of the throttle. Pulled engine back apart and come to the conclusion of oil pan not doing its job. It was advertised as a bad ass wet sump pan to control oil but does not work. I have over a 600 dollar oil pan that I can not use. Should state in the advertisement that this is not a performance pan. I would like stefs to buy it back or trade me for something that works.
This is for the front sump pans like 1070, not an issue with the rear sump pans and in my post I assumed the pan in the article was a front sump.my comment is referring to front sump 1070 pan