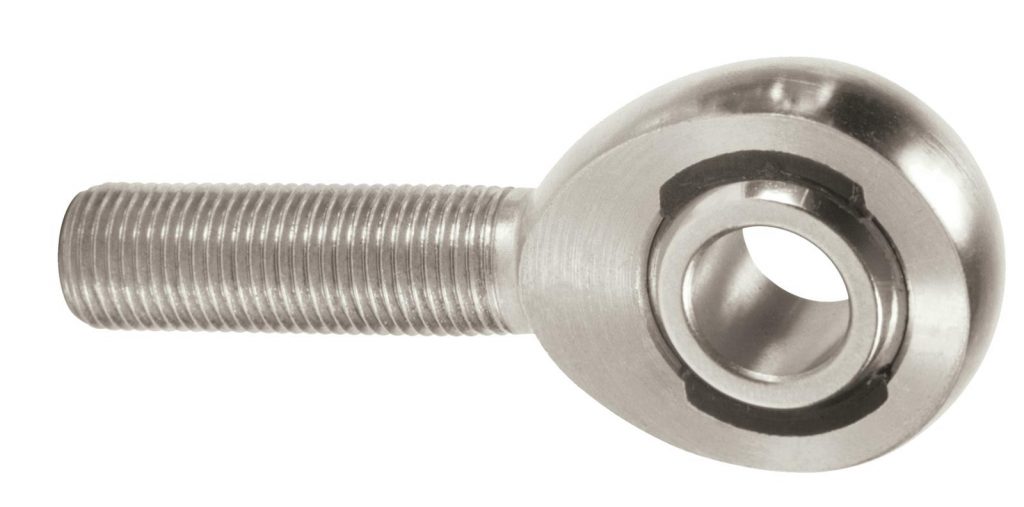
At first glance, a Heim joint rod end looks pretty simple, but there’s a ton to understand before you go about using them in your vehicle. So, we put together a little Heim joint 101 to help you pick the right rod ends for your project.
What is a Heim Joint?
A Heim Joint (also called a spherical Heim bearing rod end) is a pivot joint that, in an automotive context, is often used in custom off-road and race steering, aerodynamic, and suspension systems—basically anywhere you’d want linkage with some room for articulation and adjustability.
A Heim joint typically has a threaded shaft or bore on one end (though weldable Heim joints are also available) and a ball swivel Heim bearing on the other. The ball will be drilled with a pass-through to accept a bolt or some other form of mounting hardware. This creates a flexible joint that permits an off-angle installation and allows for a range of movement.
Available as a single piece or sometimes in Heim joint kits, you’ll typically see Heim joints on things like tie rods, traction bars, sway bars, 4-links, panhard bars, spoiler supports, and steering links on high performance race cars and off-road trucks and SUVs, which brings us to a good question…
Are Heim Joints Street Legal?
Without knowing each specific state law and vehicle application, that’s a tough one to answer with a definitive yes or no. While it is true that some state inspections have strict guidelines about vehicle suspension modification, other states have little to no inspection process at all. So the best way to be sure is to check your local state regulations before doing any significant suspension modifications to your vehicle.
But here’s something else to consider: Heim joints may not be ideal for your street-driven vehicle anyway. When used in a suspension system, they can introduce vibration into the cabin and contribute to a harsh ride. They also need to be checked and tightened to minimize play in the rod end. And depending on the type of Heim joint you buy, you might find they wear out quicker than, say, a traditional booted tie rod end—which means you could spend more time and money servicing or replacing them.
Why Use Heim Joints?
Many off-roaders and racers look to Heim joint kits because they’re durable and adjustable. (They’re also available in large sizes too, which definitely helps on rigs running oversize tires—or in situations where they may grind against rocks.)

Though it’s important to understand that, while a Heim joint can adapt to things like steering movement, chassis flex, and suspension articulation, they’re not immune to binding and breakage. So not only is it vital to ensure proper suspension geometry up front, you’ve got to make sure your Heim joints are properly adjusted as to mitigate play and slop in the system.
Heim Joints vs. Ball Joints vs. Tie Rod Ends
It’s easy to get confused here, because the terms tie rod ends, ball joints, and Heim joints are often used interchangeably—and they shouldn’t be. So let’s clear things up.
Even though they use a ball-swivel design similar to Heim joints, ball joints are typically found on your vehicle’s control arms and allow the front wheel spindles to pivot in a range of directions as the suspension travels. Tie rod ends are found in your steering system and connect the steering rack to the spindle, permitting the vehicle’s wheels to move side-to-side as the steering wheel is turned.
Heim joints simply refer to the rod end design and are not likely to be found in stock OE suspension or steering systems.
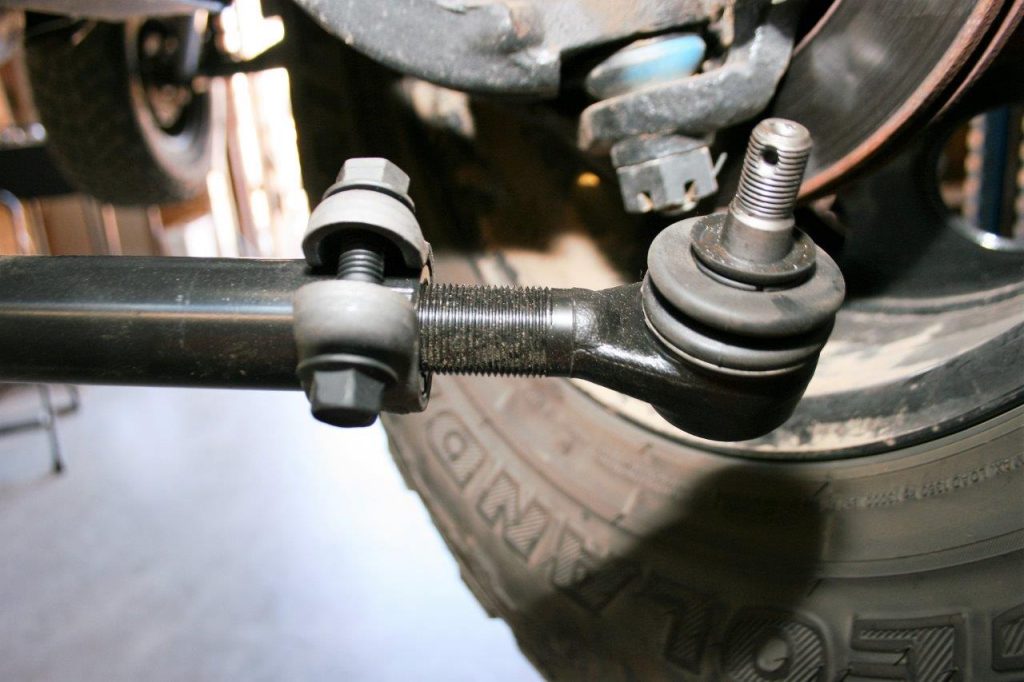
How to Measure & Install Heim Joints
For most applications, you order Heim joints based on the size and thread pitch. So it’s vital that you know exactly which size you’ll need.
Unless you’re using weldable Heim joints, the most important spec you should know for ordering Heim joints is the bore/stud size, which will determine the size of the rod end shank or bore you require. From there, you’ll need to determine the thread pitch of the bore or stud.
You have a few install options when it comes to Heim joints. The most popular may be threaded shank male rod ends. These install into a threaded bore, which means you’ll need to weld-in a threaded insert if you’re using hollow tubing or, if using a solid rod, you’ll need to drill and tap a threaded hole.
Then there are female rod ends. These feature a threaded bore receptacle that allows you to install them on a threaded rod—which means you may have to use a die to create one.
Lastly, you’ve got weld-in rod ends. These weldable Heim joints are really popular with the off-road crowd and for folks making a one-off custom setup. You simply weld the rod end housing to the rod itself.
Heim Joint Applications Outside of Suspension & Chassis
Given their ability to articulate, Heim joints are handy in more than just suspension and steering systems. For even more versatility, they come in a wide range of sizes, from large heavy duty applications like tie rods or other suspension components to smaller specialized roles like in, say, carburetor linkages and alternator brackets.
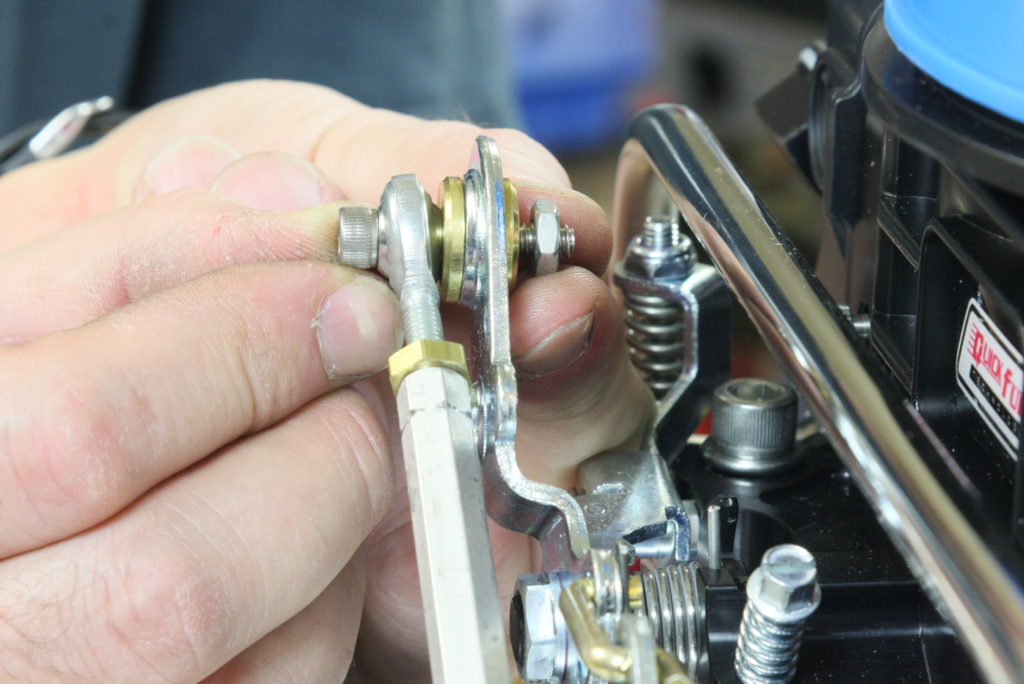
In these small Heim joint applications, the same advantages of running a spherical Heim bearing joint apply, namely in the realm of articulation and adjustability. For instance, having an adjustable Heim joint in throttle linkage can be beneficial, where a few turns of a rod end can have a dramatic effect on the position of a butterfly valve.
Heim joints are also popular for mechanical clutches, where the rotating joint can mitigate the negative impacts of chassis and body flex on the clutch linkage alignment.
You’ll also see Heim joints in aerodynamic applications, supporting things like front splitters, air dams, and rear spoilers. Again, adjustability is a huge benefit for race car drivers here.
Solid Ends, Flex Joints, Johnny Joints, Roto-Joints, and Other Rod End Types
It is absolutely worth mentioning that Heim joints aren’t your only rod end option.
For starters, there are solid rod ends, also called “rod eyes,” which boast a rigid center and offer no movement or sway. These rod ends can be very valuable for linkages or mechanisms where you want to reduce sideways motion.
When shopping for rod ends, you may also come across the term “flex joint.” That name is often used in reference to a rebuildable joint, which is an important distinction to make, because a Heim joint isn’t usually rebuildable. So, when a Heim joint wears out, your only option may be to replace the joint entirely. Depending on your application, that may not be a big deal but, specifically for off-roaders who are notoriously hard on their rod ends, having the ability to rebuild a joint can be very attractive alternative to a full-scale replacement joint. RideTech’s R-Joint XL is a good example of a rebuildable rod end.
And in applications where the joint will face a lot of rotation, specialized joints are available to handle it. For instance, UMI Performance makes Roto-Joint rod ends for specific components like control arms, panhard rods, and toe rods.
Finally, there are Rock Jock Johnny Joints. These rebuildable flex joints are practically tailor-made for the off-road crowd. They’ve got a spherical ball joint and a proprietary design that boasts impressive durability and articulation. They’re smooth and quiet, and incorporate a grease Zerk fitting for easy maintenance. Oh, and speaking of…
Rod End & Heim Joint Maintenance
Aside from regular cleaning and inspection, most Heim joints are almost maintenance free. We say almost here, because one of the most vital aspects of Heim joint use is ensuring proper adjustment. Even when used with a lock nut (jam nut), a Heim joint on a threaded shaft can slip, which introduces slop and vibration into the system—that can quickly lead to clunks, pops, shakes, and ultimately, catastrophic failure.
You’ll also want to periodically check your rod ends for gunk buildup and wipe them clean as often as you can. As with anything that relies on close bearing tolerances, even a tiny bit of grit can really exacerbate wear.
As mentioned earlier, some rod end designs feature a Zerk fitting to pack the bearing with grease. Packing a bearing with grease not only pushes vital lubricant into where it’s needed most, it creates a barrier to keep water and muck out of the joint.
What Rod End Should You Use?
While every vehicle and driving environment faces different needs, hopefully this article explained where different rod end designs can be beneficial, and why some many builders, racers, and off-roaders use Heim joints and similar rod ends on their vehicles.
The good news is that, unless you’re creating something like a true one-off custom suspension or steering system, there’s a good chance folks have experimented with Heim joints on your vehicle model. So do some internet sleuthing, ask around the racetrack or trailhead, and pose questions in forums—you’ll likely receive good rod end advice on your specific vehicle application and use case.
thanks for the information. It is very beneficial.
Very valuable information. Thank you.