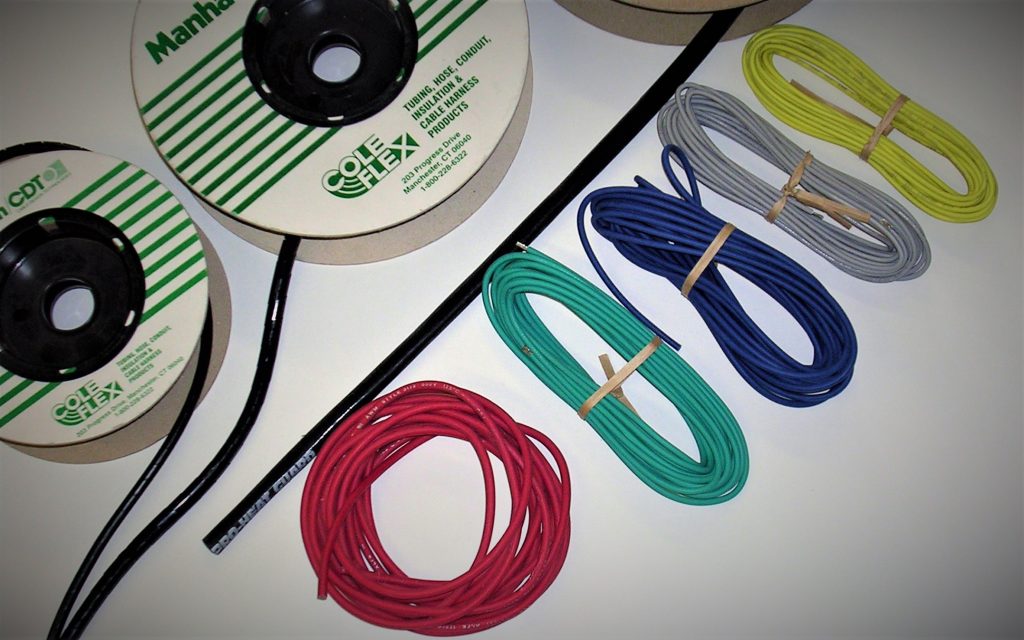
The wire you use to hook up electrical equipment in your car is important stuff.
How important?
We’d say it’s absolutely crucial. And if you don’t believe it, just ask the guy who has had to chase a dead short. It’s not in the definition of fun for most, and it gets even worse if you have to track it down while you’re stranded by the side of the road. Sure, a single piece of wire is seemingly dirt simple—but what type of wire do you really need?
That’s a good question.
If you ever take a look at the hulking wiring harness(es) hidden deep inside your modern daily driver, you’ll find a huge mix of wire shapes, sizes, and colors.
Modern Automotive Electrical Wire Construction
Electrical systems in new vehicles are complex. That’s no secret, but the vast majority of these harnesses have one thing in common: The individual wires inside the harnesses are manufactured with a pure copper core.
Compared to other materials that have a similar or even superior conducting capability, copper is relatively cheap (although with ever escalating metal costs today, you might not agree). Silver is likely the only pure metal that is equally suited to the job, and it does a better job of conducting than copper. But the stark reality is, pure silver is prohibitively expensive (check the price sometime, you’ll be “shocked”).
That leaves copper, and copper derivatives (silver coated copper wire, etc.) as the mainstay of the automotive electrical business. And that’s why copper has been the electrical wire material of choice ever since the dawn of time.
Both the aircraft industry and household construction have toyed with the use of aluminum conductors over the years (some with disastrous results).
Want to learn a good way to connect electrical wires? Check this out: The Lineman’s Splice: How to Make Reliable Electrical Connections in Your Vehicle’s Wiring Harness
Copper vs. Aluminum Wire
There’s seemingly good reason for trying to use aluminum: It’s cheaper and certainly lighter than copper, but on the other hand, it simply does not conduct electron flow as well as copper. When the size of aluminum wire is increased to compensate for the higher electrical resistance, it’s still a loser from the flow perspective.
There’s more too. In the aviation business, a couple of manufacturers have tried using aluminum battery cable. While this sounds like a perfect application, there’s definitely a downside to using aluminum battery cable.
You see, the type of aluminum suited to the manufacture of wire is, by nature, soft. And soft aluminum has a tendency to work harden when stressed beyond its elastic limit. This in turn causes it to become brittle and eventually crack (something you might get away with in a car, but something you really can’t live with in an airplane).
So what causes this? Ponder the terminal crimped to the end of the aluminum wire or cable: When crimped, the process physically disturbs the aluminum core of the wire. This begins the work hardening process.
More importantly, if aluminum core wire isn’t supported carefully, it can be subject to vibration. This vibration begins the work hardening process the minute the aircraft (or in our case, the car) is started. The grief associated with maintaining a good wire termination coupled with the vibration problems usually isn’t worth the trouble, particularly if the weight savings is measured in a few ounces.
Stranded or Solid Core?
OK. Aluminum is out. That leaves copper. But there’s certainly more than one variety of copper wire.
For example, the wire used in your house is thick and solid. This wire is tough to bend, which works fine for house construction. The electrician can fish and string stiff wire almost effortlessly. On the other hand, something like a cord for a toaster has a core that consists of finely stranded wire. It’s not difficult to bend the wire used for your toaster.
For the most part, copper is a very ductile material. This means that you can wrap a piece of solid 10 gauge wire around a very tight bend and it will lose very little of its structural integrity.
There’s a catch though: If you straighten the wire and then re-bend it several times, it too will work harden. In this bending and straightening scenario, the ductility eventually diminishes. Cracks will begin to appear on the surface of the wire. If the bending and straightening continues the cracks will increase in size and, you guessed it, the wire will eventually fail.
The wire on your toaster doesn’t fail. That’s because the wire is stranded, not solid. If you place 19 strands of 22 gauge wire into a bundle it will have roughly the same cross-sectional area as a piece of solid 10 gauge wire. Repeat the wrap test around a tight radius mentioned above. It won’t fracture. The reason is the reduction in size of the individual wire in the strand produces (approximately) a proportional reduction of stress.
As a result, stranded wire is not only good news for you toaster; it’s absolutely perfect for automotive wire. (Note: We’re not suggesting you salvage toaster wire for your car.)
Selecting the Right Wire Gauge
When it comes to stranded wire, the choices typically range between seven strand and 19 strand (in this instance, using a small 22 gauge wire). When it comes to small wire such as 22 gauge, the core can be made up with a total of seven strands of 30 gauge wire. If 10 strands are used instead of seven, then the strands are 43 gauge (basically, the larger the number of strands, the thinner they become in a given wire gauge). If you have a choice, pick the wire with more strands.
Protecting Against Corrosion
Back to the kitchen. Set out a nicely polished copper pot and don’t touch it for a month. You’ll need to dig out the metal polish pretty quickly, because in four weeks or so, that pot will look real rough.
You see copper is an “active” metal. What that means is that it readily reacts with oxygen in the air along with moisture and, of course, with airborne pollutants. Stranded wire is, for all intents and purposes in the same boat.
The reality is, there’s no practical way to completely seal the circulation of air (and moisture) between the respective strands in a wire bundle. Plastic wire insulators are not barriers for the protection of the wire from the environment, particularly when exposed to hydrocarbons (for example, gasoline, grease, oil, etc.).
Here’s the problem: The majority of automotive wire is not protected from the environment or from hydrocarbon contamination. As a result, it typically has a service life of something in the order of ten years (maximum). After that, deterioration sets in. How can you fix it? The wire can be plated prior to the stranding process.
Although some wire is silver-plated, a more common solution is to tin-plate the wire. Tin plating is a relatively simple task and it’s much more resistant to chemical “activity” than bare copper. If you buy wire manufactured for aviation purposes, it will be tin-plated.
When Henry Ford began mass-producing automobiles, plastic as we know it didn’t exist. Wires were typically covered with rubber that was extruded over a series of twisted strands of wire. The rubber-covered wire was, in turn, surfaced by a cotton braid. Finally, a coating of shellac compound covered the wire. This early form of wire covering not only proved brittle, it also had a tendency to attract fungi. Not good.
But with the dawn of the 1950s, a solution arrived: Plastic. Some forms of plastic wire coverings are still in use today (typically they are PVC plastic, or “Poly Vinyl Chloride”). In a military aircraft application, PVC wire coverings were typically reinforced with a layer or two of synthetic fiber over-braids (in some cases, the bare wire strands were first covered with the braid, then sealed with a PVC covering).
Plastic (PVC coverings included) is actually porous. As some of you know, chemicals eventually leak out of something like a plastic jug if you let it sit long enough. In the case of wire coverings, the reverse is true too: Contaminants eventually pass through the PVC jacket and attack the wire (and as expected, un-plated copper wire is especially susceptible).
One solution is a build the wire jacket from Teflon. Teflon stays flexible and soft at both extremes of it’s operation range. It sounds absolutely perfect, but there’s a big caveat attached when it comes to pure Teflon wire jacketing: It is prone to damage from abrasion. The aircraft industry solves this by wrapping Teflon coated wire with a PVC jacket. This is an expensive process (perhaps way too costly for a typical hot rod). The reason is the wire is first plated in silver or nickel, before the Teflon can be formed over the bundle. Worse, in the event of a fire, Teflon can give off toxic fumes.
Protection Against Heat
Is there another answer? There aren’t really a lot of options.
For example, you can use PVC insulated wire in most areas of a hot rod or race car. The exception might be the engine compartment. There are two types of PVC insulation readily available. One is rated to 80° Celsius (176° Fahrenheit) while the other is rated at 105° C (221° F and, FYI, water boils at 100° C).
Teflon, on the other hand, won’t melt at temperatures in the 400 to 500° F range (that’s why you see it used on “non stick” frying pans—your electric stovetop won’t reach that temperature). Wire bundles outside of the engine compartment can routinely see temperatures that range as high as 180° F. Unfortunately, engine compartment temperatures might be as high as 300° F (or more in localized areas heated by headers or exhaust manifolds). When you add the chemical mix commonly seen in cars (fuel, oil, brake fluid, solvents used for cleaning, etc.), it’s easy to see why the wire insulator can deteriorate quickly.
One answer could be something called “Tefzel.” This stuff is closely related to Teflon (the military has a spec for it: MIL Spec W-22759) but it doesn’t quite have the sheer temperature resistance. It has been known to be the cause of some aircraft service problems, particularly in regions of extreme heat, but it is more abrasion resistant than conventional Teflon. Tefzel is generally available in a range of gauge sizes and it can be found at aircraft avionics shops (these are the guys who handle aircraft instruments, radios, and electronics) and at some aircraft surplus outlets.
Protection Against Critters
Something else to ponder, particularly with new cars, is soy-based wire insulation. It is widely used today. Sounds like an eco-friendly product, at least at first glance. But many have discovered a problem: it tastes good to rodents. There’s evidence both ways (rodents love the stuff or they don’t care). But today it’s not uncommon to see cars lined up at dealerships awaiting wire harness repairs. And rodents don’t differentiate. They’re equally comfortable chewing up imports as well as domestics. Ask me how I know.
Wraps, Tubing, Looms, Sleeves & Covers
Wire doesn’t have to withstand heat or abrasion alone. It can be protected with a quality wire wrap. The most common covering is “flex tubing.” This cable organizer is basically, a form of corrugated, split tubing manufactured from plastic (polyethylene). Typically, it’s available in varying sizes ranging from 1/4 inch ID to two inches ID.
For most applications, this form of tubing offers good protection for wiring harnesses, cables, tubing, and hoses. It’s lightweight, has excellent flexibility and provides protection from abrasion, puncture, vibration, and friction. It also protects against heat (but only up to 200° F), sunlight, water, snow, ice, and automotive fluids. That’s why it’s commonly used in production cars. The dilemma with split loom is that it is, for the most part, ugly.
Another good option is spiral wrap (often called “spi-wrap” by insiders). Spiral wrap is commonly used in aircraft applications (avionics, wiring runs, etc.). It’s manufactured from a semi-rigid form of plastic, and the idea is to provide protection against abrasion, without completely encasing the wiring. The elastic memory of the material holds wires and hoses in neat, tight bundles and protects them from abrasion (it’s also great for protecting braided AN hoses from chafing or abrading adjacent parts).
If the wire is entombed in a solid protective sleeve, there’s a good chance it will degrade from the inside out from trapped moisture. Spi-wrap allows the wire to “breathe” and it also allows the harness to make relatively tight bends. With the flexibility of spiral wrap, you can break out one or more wires at any point in the bundle.
While there are some varied colors available from various manufacturers, the most common is black or translucent white. The black material has better UV resistance for continuous outdoor exposure. The most common sizes range from 1/8 inch to 3/4 inch in 1/8 inch increments, although with a bit of searching you can find the stuff in sizes ranging up to 1-1/2 inches OD.
Unaffected by direct sunlight, saltwater, fuels, oils, and detergents, most spiral wraps operate over a -105° F to 215° F temperature range and meet military specs MIL-I-631D, and MIL-P-26692. It looks good (at least to us). And it does the job of protecting the wiring in a sometimes-hostile environment. By the way, some electronics stores sell the stuff, and so do aircraft avionics shops. We should also point out there are some Teflon-based spi-wraps available that can operate at temperatures ranging from -450° F to +500° F. These spiral wraps are commonly used on laser or other industrial cutting equipment that is exposed to sparks.
Wire Heat Shielding
If heat is an issue with electrical wiring, look no further than some of the high quality ignition wire sleeving that is available today. For example, MSD’s Pro-Heat Guard is an extremely tough sleeve material that consists of a thick glass woven core that resists temperatures up to 1,000° F. A silicone rubber coating surrounds the core adding protection against abrasion and heat. The sleeve is manufactured with a 3/8 inch inner diameter so it easily slides over most spark plug wires. That means it can easily slide over vulnerable wire bundles found inside your engine compartment (starter wiring is a good example). You can also seal the ends of the heat sleeve with the shrink sleeves. Simply slide the sleeve over the wire and boot and apply heat to shrink the sleeve until a tight seal is formed.
Another heat protection product is Bentley-Harris “ConvoShield” (Federal Mogul is the parent company). If you open the hood of a new car, you’ll often see a silver cover shielding on susceptible sections of wiring harness. This sleeving is composed of a nylon copolymer base substrate and a highly reflective coating, that protection for wires, cables, and hoses in applications that have heat source temperatures as high as 500° C (1,000° F). The reflective surface of ConvoShield is extremely resistant to several automotive fluids and is (obviously) resistant to heat distortion. Tests have shown this stuff can withstand 1,000° F radiant heat for one hour without distortion when placed one inch away from a heat source. FYI, electronics companies routinely sell various Bentley-Harris products, and if you search the web, you’ll find several companies selling it mail order.
The Best Choice(s) for Wiring Your Ride
When comes to making a wiring material choice, the best bet is finely (multiple) stranded copper core wire (remember too, the more strands in the core, the better). If you’re bucks-up then use a nickel-plated or silver-plated wire. For a more affordable route, use copper core wire with tin plating.
Heat is the enemy of wire with a PVC insulator. Teflon and Tefzel don’t mind heat, but they don’t really appreciate abrasion.
If you use a Teflon coated wire, be careful when it comes to abrasion.
Coverings such as spi-wrap can prolong wire life considerably. So does adequate support for runs of wiring. In the end, good quality, more expensive wire lasts longer and provides a superior service life (no secret).
Check out the photos below for a closer look.
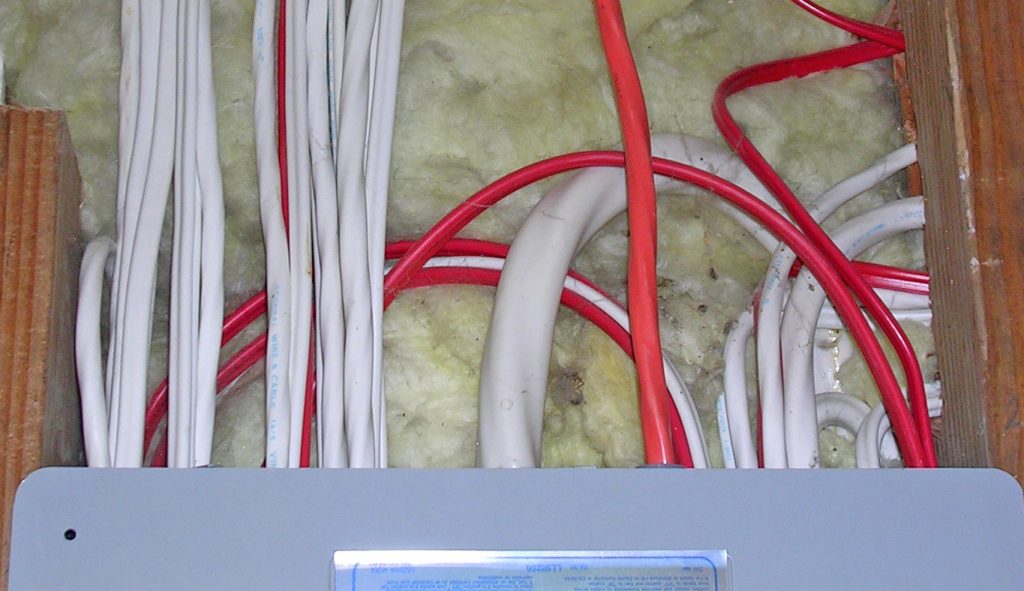
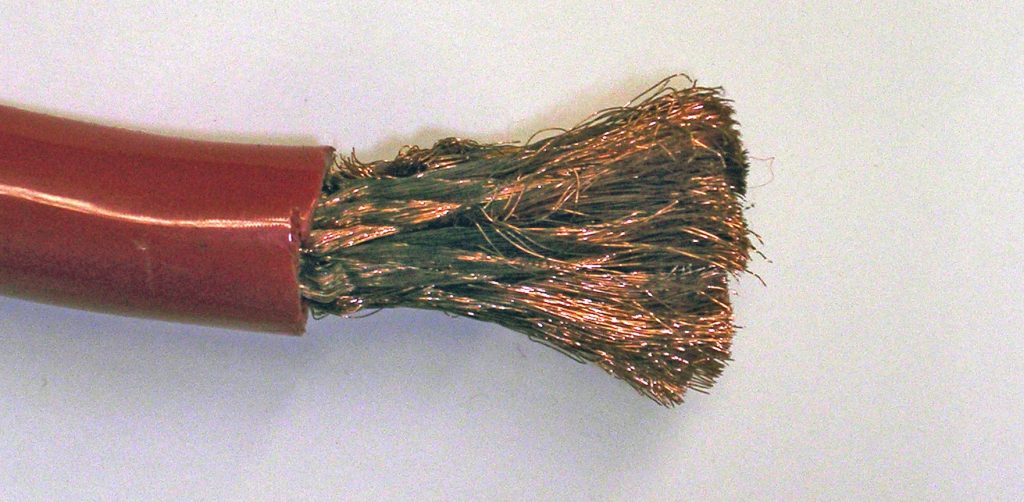
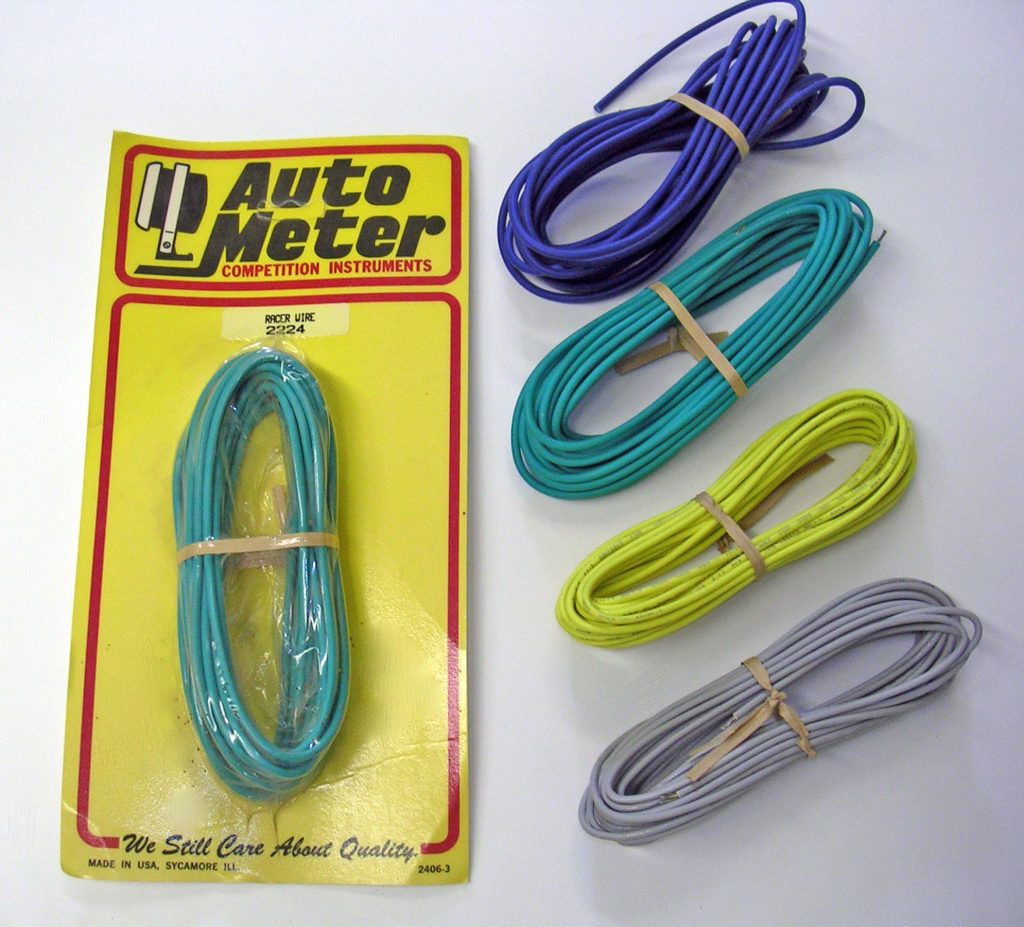
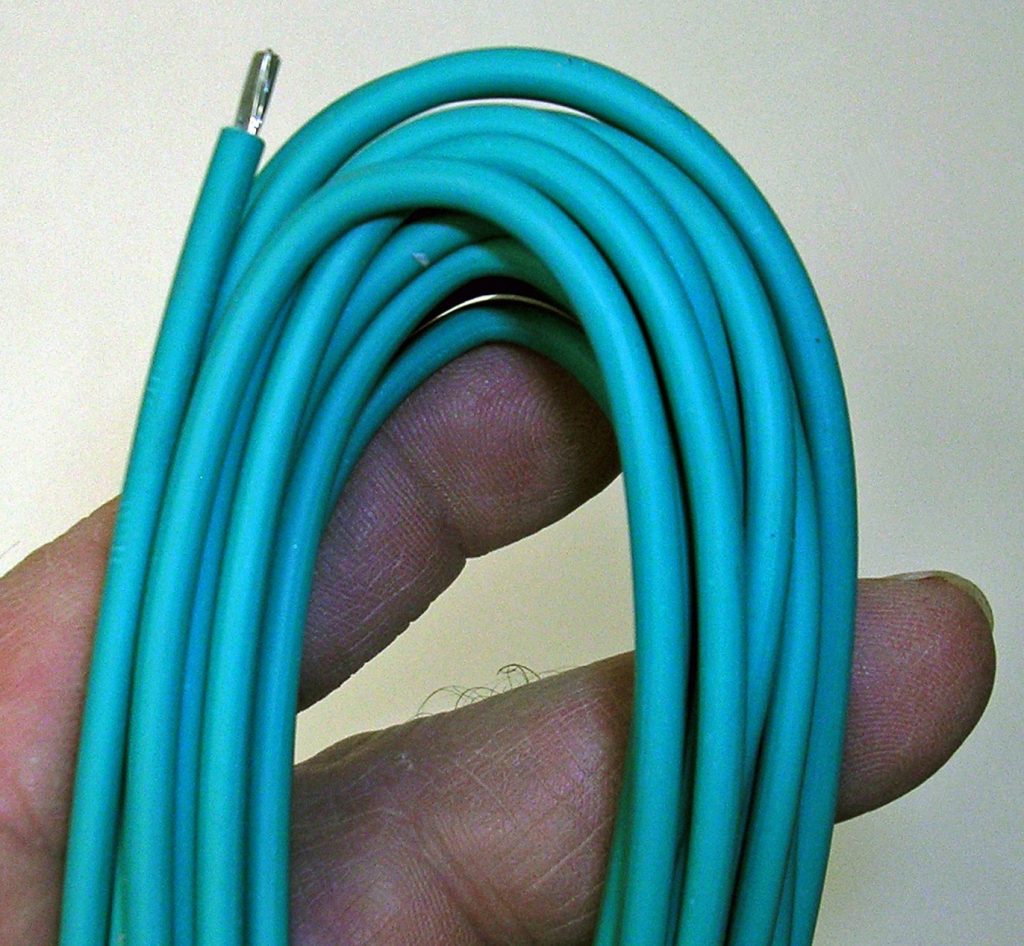


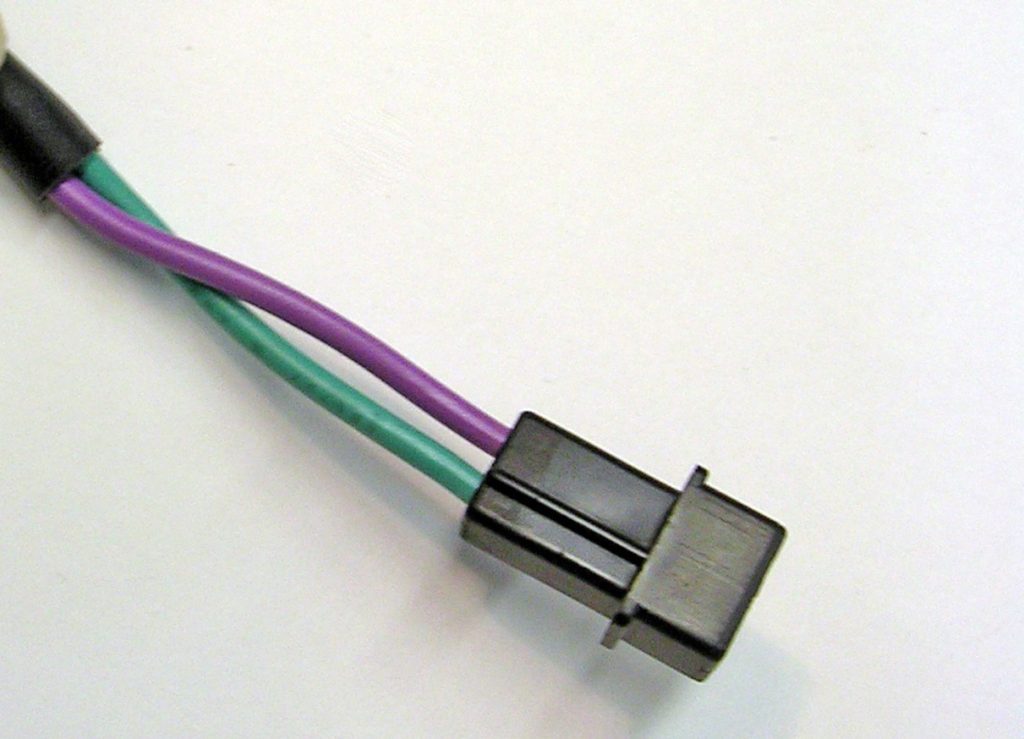
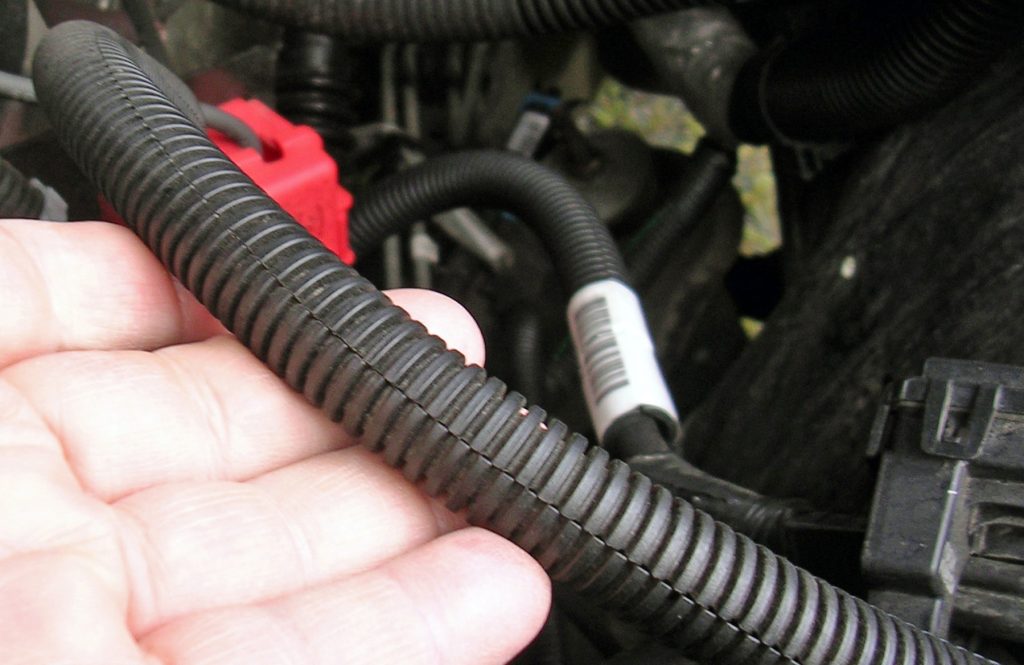
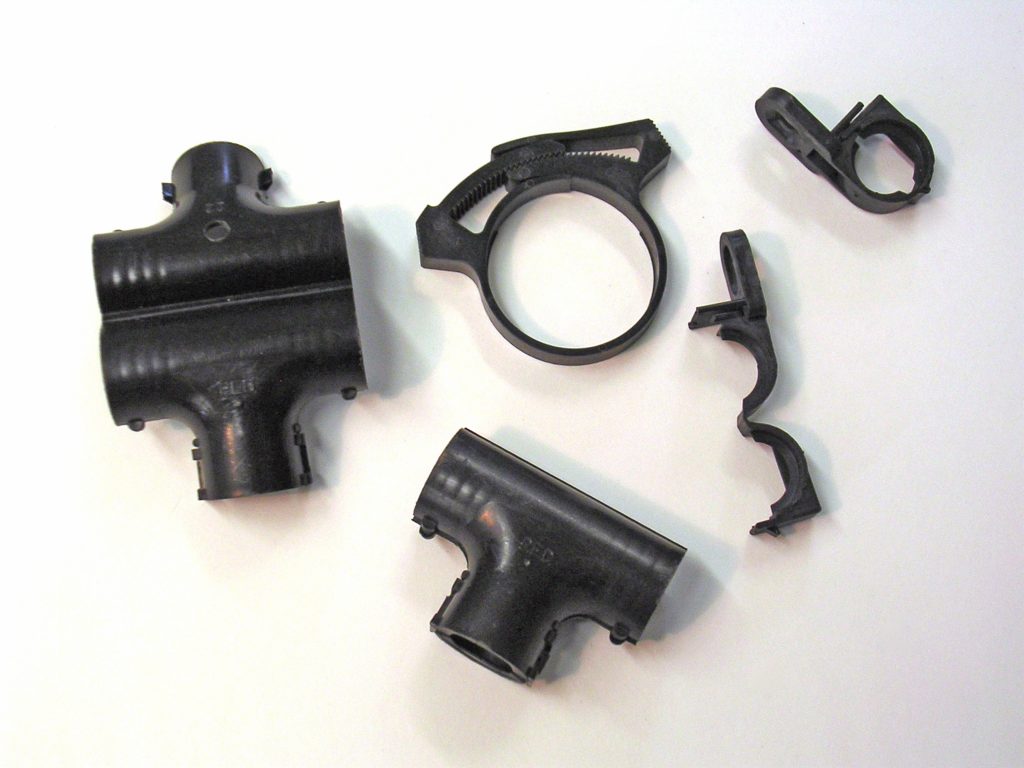

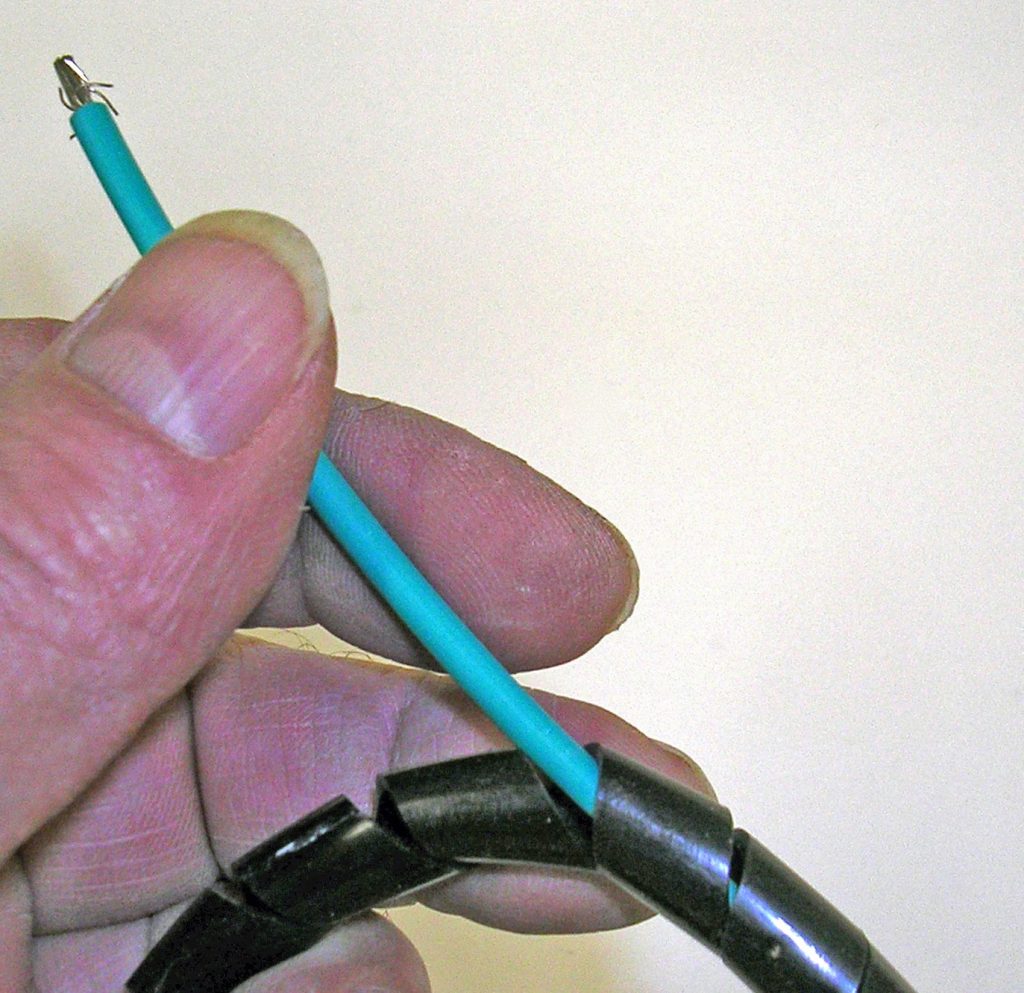
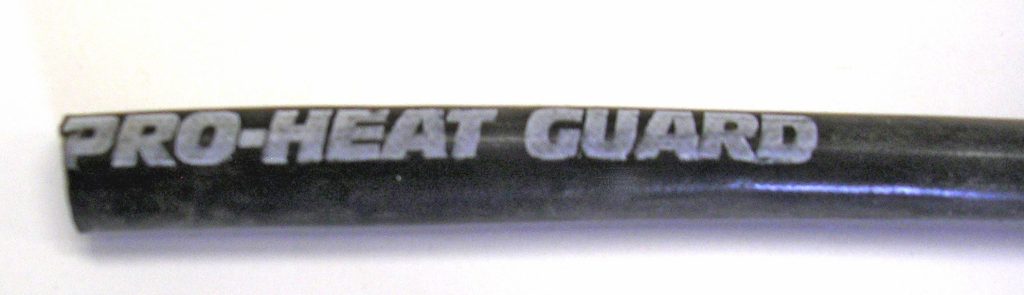
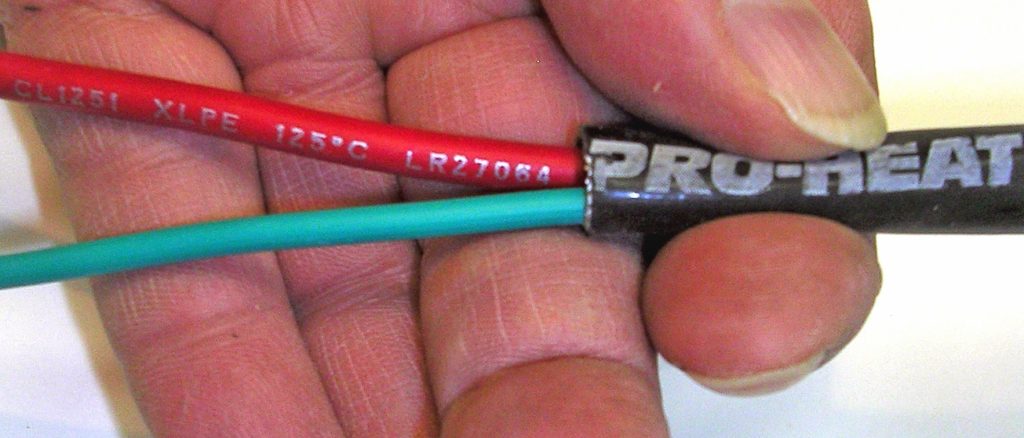
Awesome amount of information. I enjoy reading this information. Never get to old to learn and keep up with the new technology.
Keep up the good work