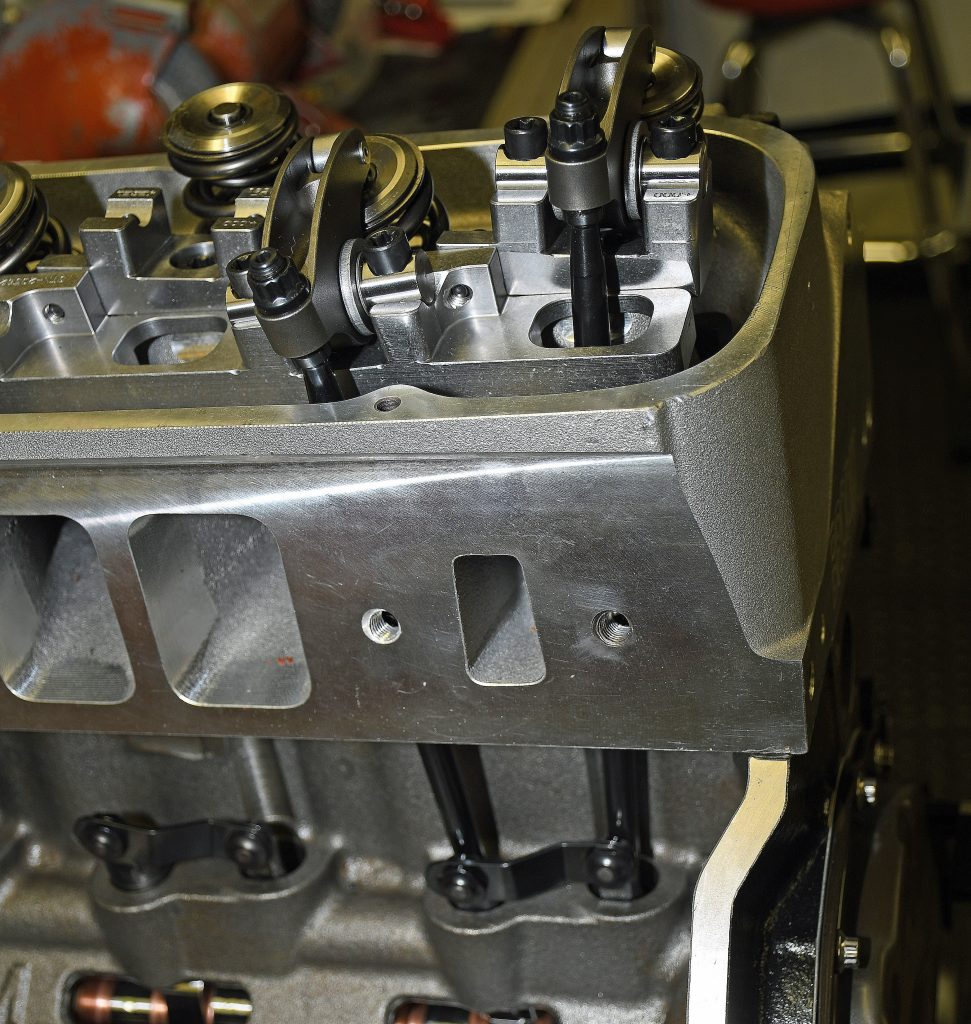
Pity the poor pushrod.
The loads it must encounter are sizable. How sizable? Consider one of the writer’s engines—a simple 565 cubic inch, pump gas big block Chevy. It’s equipped with a set of 1-5/8 inch diameter PAC valve springs (PAC-1224-16). They’re installed with a seat pressure of 250 pounds while the open pressure is 810 pounds. Factor in a rocker arm ratio of 1.7:1 and you’ll find each pushrod in this engine must endure 1,377 pounds of pressure to open a valve.
Also keep in mind the springs used as an example here are small compared to what you might find in a modern drag race application. In those cases, spring open pressures can exceed 1,400 pounds and rocker ratios can be 2:1 or more.
Nonetheless, each valve opens once per cycle in a four stroke engine (once every other revolution), so for every 2,000 RPM, each valve opens 1,000 times. Factor in a rev limit of somewhere in excess of 6,500 RPM and you can see the forces the pushrod is absorbing are colossal. Essentially, all of that load is transmitted through a rather small ball or cup on each end of the pushrod.
Pushrod Weight vs. Strength
Years ago, weight was king when it came to pushrods. The lighter the better. As expected with flyweight pushrods, they weren’t exactly structurally sound. What happened was pushrods were deflecting. Pushrods were bending. Pushrods were breaking.
And the valvetrain was experiencing a phenomena called “loft.” Basically, tappets were taking flight and becoming airborne while traveling over the nose of the camshaft.
As the folks from Trend Pushrods point out: “The actual movement of the valve was far removed from that suggested by the camshaft’s profile.” But that’s certainly not all. Trend notes: “While transferring the motion created by the cam profile, pushrods are exposed to extreme vibration and shock from the opening and closing of the valve against extreme spring pressure. Certainly, these forces are present in a stock engine, but when the camshaft profile becomes more aggressive, valve spring pressure must also increase if higher peak engine speeds are to be realized. Thus, the strain endured by the pushrod is exponential to the aggressiveness of the cam grind, the weight of the valve, the pressure of the valve spring, and the engine speeds among other factors. Inventing a new pushrod, Trend was the first to recognize that column deflection, harmonics, and compression of the pushrod would cause the net valve action to be significantly different from the travel created by the tappet.”
Much of this was discovered by Spintron inventor, Bob Fox. Not only would Fox invent the Spintron (with the late Randy Dorton), he also instigated a change in the way pushrods would be viewed and built. The Spintron invention showed the way:
Flyweight was out. Structural integrity was in.
Trend’s Spintron research on pushrods found that double tapering the profile of pushrods—where the center is dimensionally larger than either of the ends—provides a way to increase diameter without taking up valuable space in a cylinder head. The reason space is an issue is because ports have become larger, and those ports encroach upon pushrod room. A tapered pushrod allows for fit in the limited space, but offers more strength than a small diameter example.
Understanding Pushrod Movement & Harmonics
Something else to consider is this: As the lifter rises and the rocker arm moves through its arc, the pushrod is actually moving in different directions simultaneously. This is one of the things that creates the deflection we mentioned earlier.
Trend found that a tapered pushrod is far superior at combatting this deflection. But that’s not all: The Spintron testing also determined harmonics prove to be an issue with pushrods of all sorts. This becomes particularly important when the harmonics have an effect upon the valve spring. It can become devastating. But as it turns out, tapered pushrods tend to dampen many of those harmonics before they’re transferred to the spring.
Tapered Pushrods
Over the years, Bob Fox and company (Trend Performance), eventually arrived at the one piece, 7/16 inch double taper pushrod. According to Trend: “Available from 6.000 to 11.550 inches long, and in increments of 0.025 inch, these 4130 chrome molybdenum pushrods are case-hardened to a value of Rockwell Rc60 and are used extensively in drag and oval track racing at all levels.”
When it comes to those tapered pushrods (like the examples shown in the photos below), Trend actually builds them in 3/8 inch or 7/16 inch diameter with wall thickness dimensions of 0.080, 0.135, and 0.165 inch. They also catalog a huge 1/2 inch diameter example with an equally large 0.200 inch wall. All of these pushrods are manufactured with 5/16 inch ball/ball ends. The ball ends are machined to a tolerance of plus or minus 0.001 inch. When complete, the pushrods are black oxide finished and the part number and specs are laser-etched on the body.
Trend Pushrod Construction
It’s interesting to note the chrome molybdenum tubing used in these pushrods is custom-made to Trend’s specifications. They order material in large batches of 50,000 to 100,000 feet and each batch is carefully examined for specification compliance prior to pushrod production. Trend incorporates strict procedures when it comes to cutting, forming, and machining the steel tubes (and bars for fuel car applications—but that’s obviously beyond our scope here).
They also go through a unique heat treatment process. When it comes to the exact details of that heat treatment process (temperature coupled with the time required for quenching and tempering, along with specific cryogenic processes) it’s top secret, proprietary information.
But what isn’t secret is the fact Trend actually built special tooling and fixtures for the heat-treating procedure. They came up with unique racks fabricated from round bar stainless steel to handle countless heating cycles in the furnace without degradation. The racks are laid out so that the pushrods are positioned vertically to within three degrees.
Prior to heat treatment, the pushrods are straight, but as stresses are relieved during the process, they warp—but the dilemma is, the warping is never consistent. Trend tells us each pushrod is warped in its own unique way. As a result, each and every pushrod must be assessed and straightened. Some of the pushrods are straightened by hand and others are straightened by automatic straightening machines that calculate the process by way of computer analysis.
Respect the Pushrod
As you can see, there’s a lot more to pushrods than first meets the eye. And there’s much more to the story—we’ve simply scratched the surface here. Basically, pushrods are subjected to considerable (amplified) spring pressures, considerable harmonics, considerable movement changes (deflection), and more.
But though they’re not the most exotic pieces in your engine, they could end up being some of the most important.
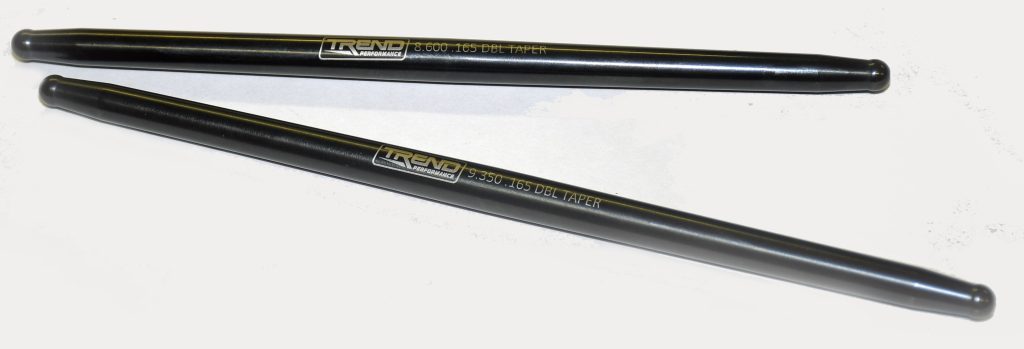
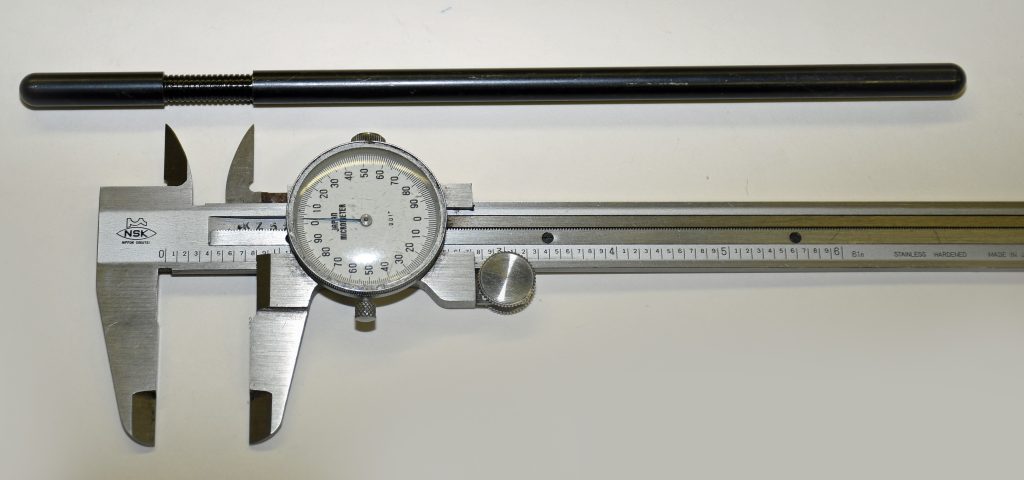
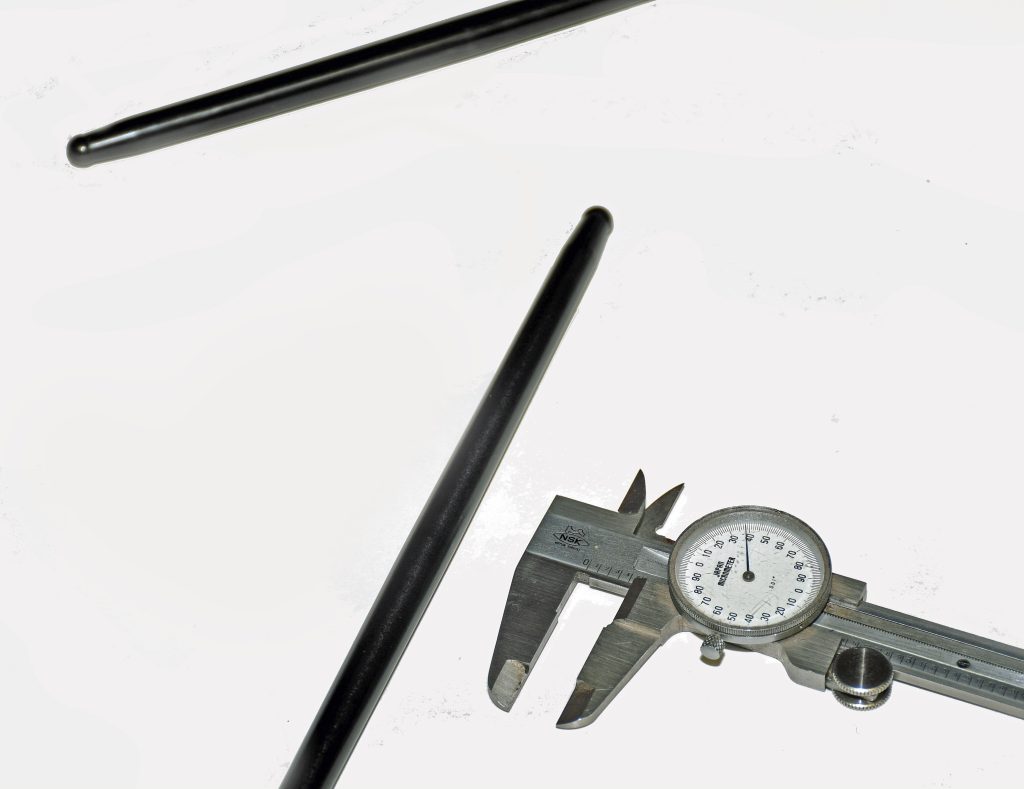
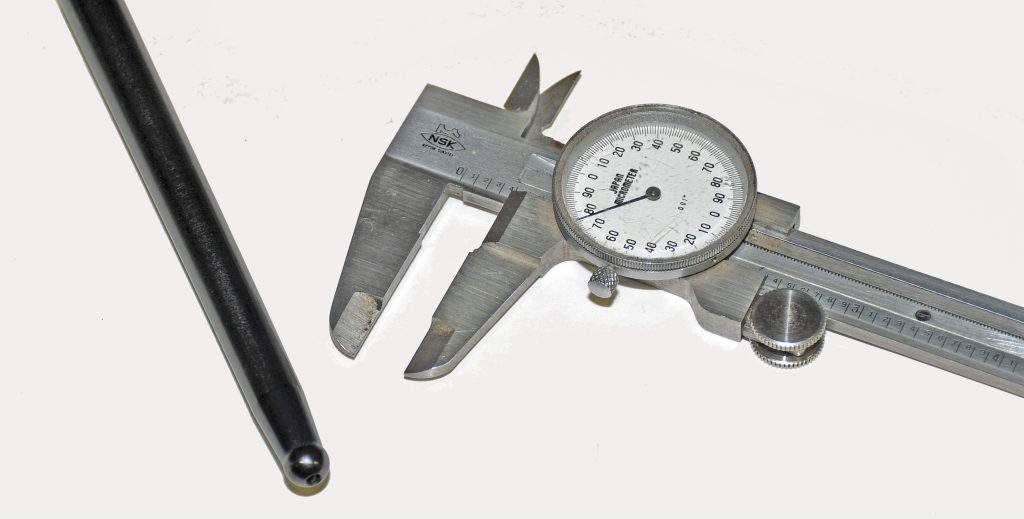
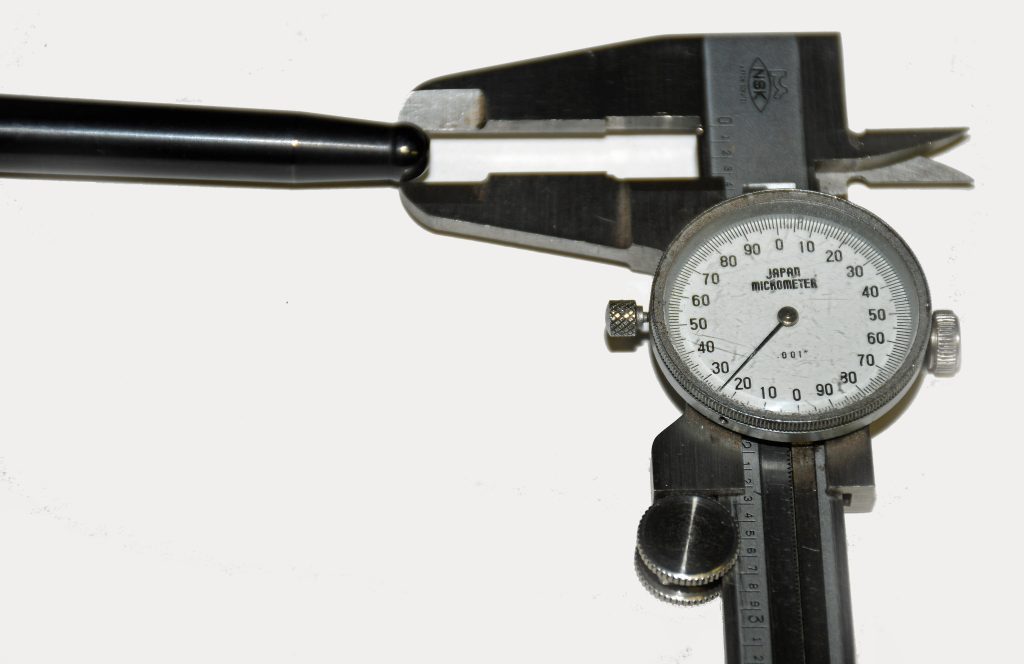
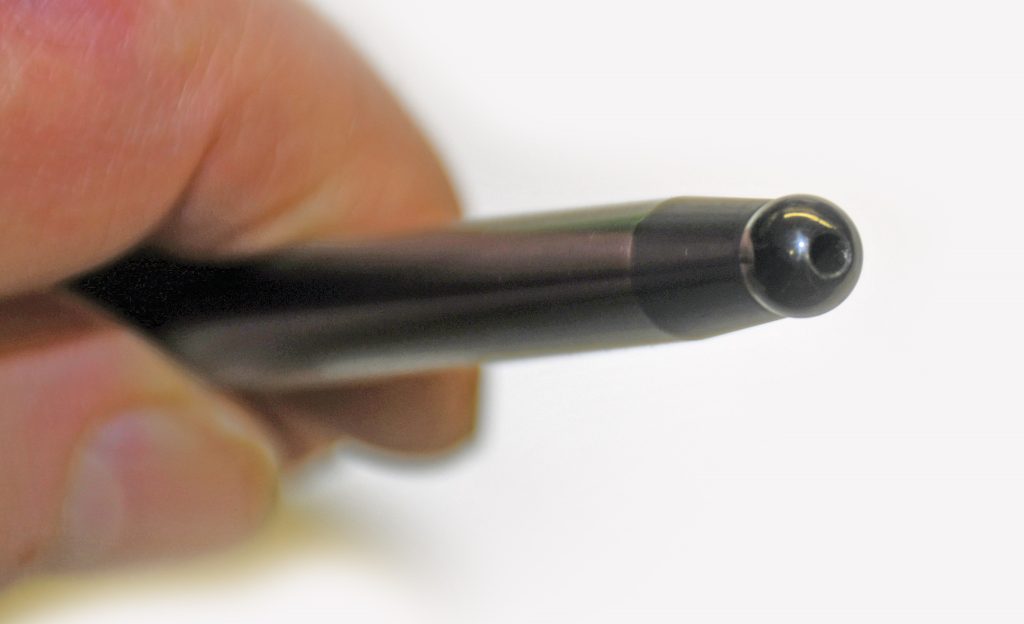
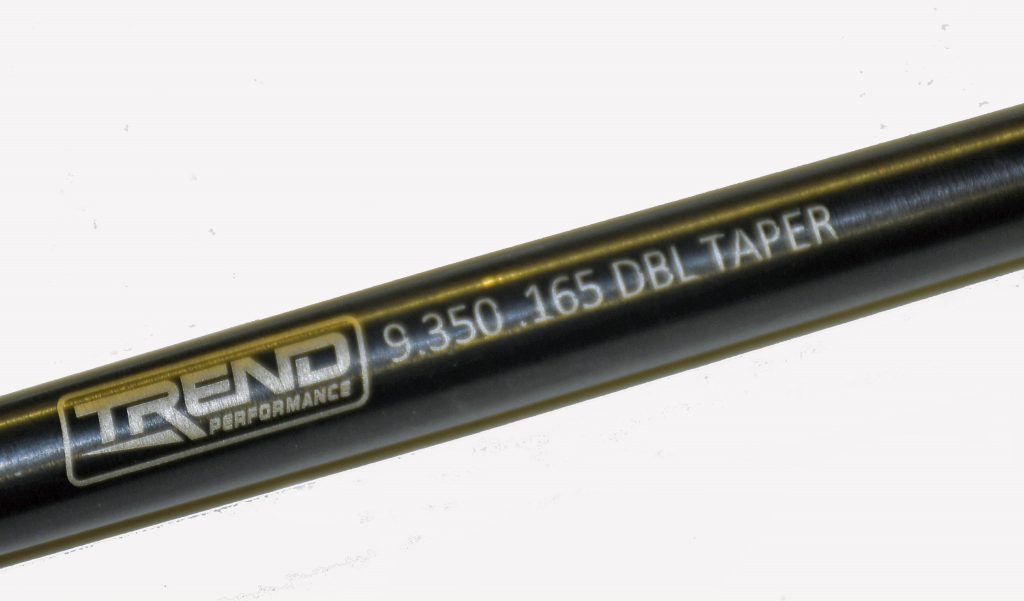
Appreciate the information, which opens the door on valve train dynamics,
please continue.