There are plenty of automotive uses for a hacksaw in the garage or workshop, including cutting sheet metal, bolts and screws, metal tubing, rubber hoses, and so on.
But with so many different hacksaw types and blades out there, how do you pick the best one for the job at hand?
The basic hacksaw is made up of a metal frame (most of which are adjustable) incorporating a handle and of course, a replaceable hacksaw blade.
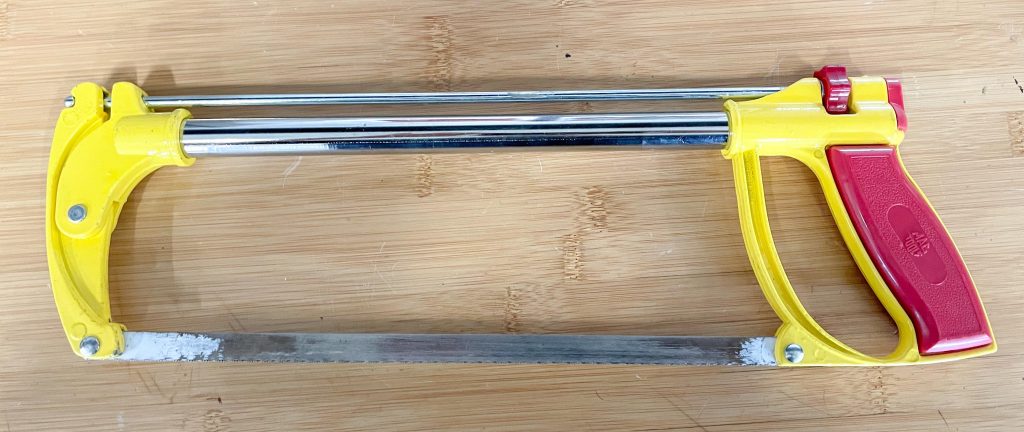
Better quality hacksaws are built with a protected handle. This means your hand is positioned inside the handle. This prevents your skin from coming in contact with the blade or the material you’re cutting. It’s also a very helpful safety feature should the blade ever break.
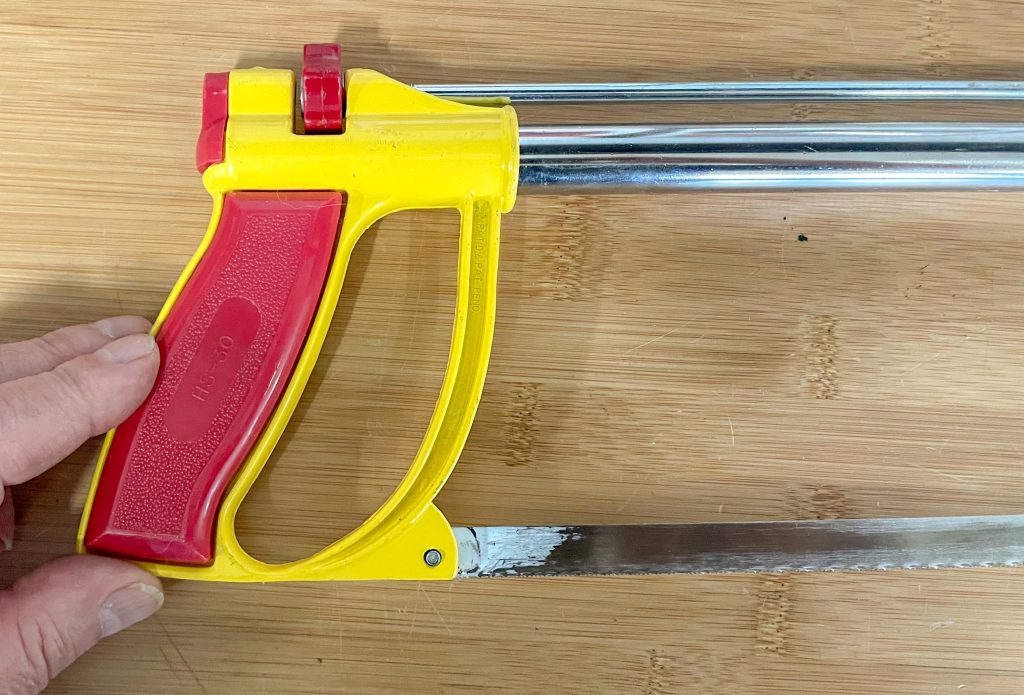
Hacksaw blades are manufactured of hard tempered steel. Typically, the blade may be all hardened or flexible. The flexible blade is designed so that only the teeth of the blade are hardened. Meanwhile, an all-hardened blade is designed so that the complete blade has been tempered.
The pitch (aka the number of teeth per inch) is normally 14, 18, 24, or 32 teeth per inch.
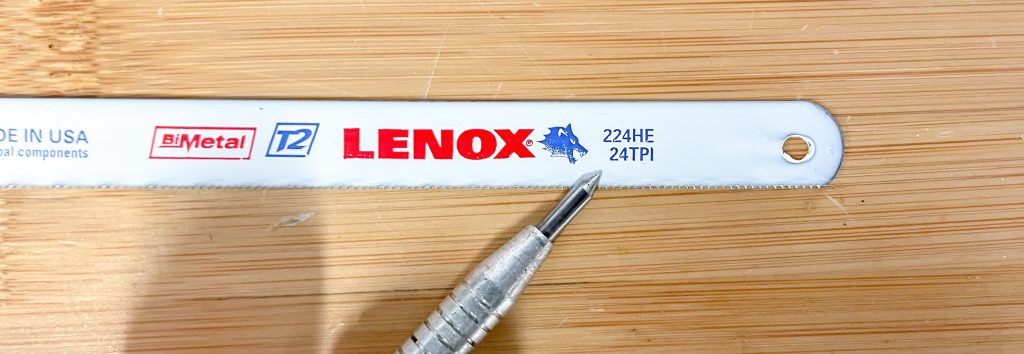
The part number (or portion of the part number) of the blade will often coincide with the number of teeth per inch. For example, a part number with a 1024 in it equals 24 teeth per inch. A 1018 works out to 18 teeth per inch.
Due to the fact hacksaw blades are hardened, they cannot be re-sharpened. Obviously, once the blade becomes dull, it must be tossed.
How to Choose the Right Hacksaw Blade
A hacksaw blade must be selected for the task at hand.
When cutting hard (or thin) materials select a blade with more teeth per inch (for example, a blade with 32 teeth per inch).
In contrast, when cutting soft material such as aluminum or brass, select a blade with fewer teeth per inch (for example, a blade with 14 teeth per inch).

When shopping for hacksaw blades you’ll often encounter “bi-metal” examples. So…what are they?
Essentially, bi-metal blades are manufactured with high-speed teeth that are electron-beam-welded to a tough, yet flexible die steel backing. Bi-metal construction allows blades to bend and flex without breaking or shattering.
Most folks will tell you these are their go-to blades for hacksaws.
Whatever blade you select (type or tooth count), it’s a good idea to ensure that at least two teeth of the blade contact the material you’re cutting. This is particularly important when cutting something round like a bolt or a piece of tubing.
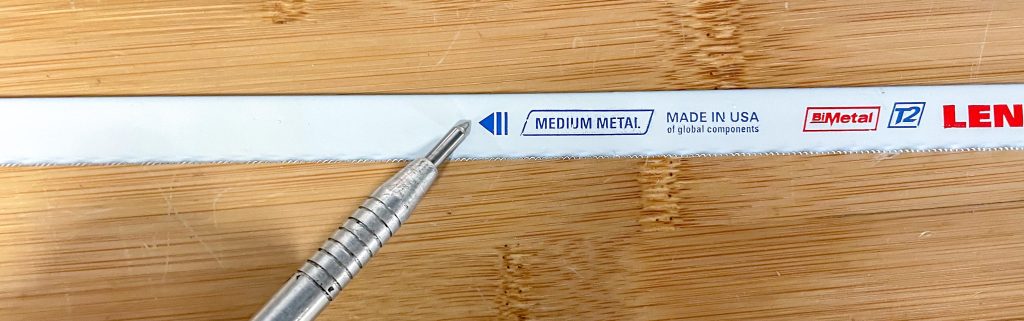
Hacksaw blades can either have a wave tooth pattern (this is for fine tooth examples) or a coarse blade. In either case, the teeth of the blade are alternately pushed away from sides of the blade. This small departure in tooth angle is necessary so that the slot cut by the teeth will be ever-so-slightly wider than the blade.
The prevents the blade from getting stuck in the material as you’re making a cut. Carpenter’s saws are designed in much the same manner. As the hacksaw blade teeth become dull from use, the teeth will narrow a wee bit. As a result, the slot the blade creates will become narrower.
That’s why a dull blade will usually get stuck in the material you’re cutting. The end result is often a broken saw blade.
Why do Hacksaw Blades Break?
Speaking of broken blades, typically, blades break for the following reasons:
- Excess pressure applied to the blade
- Excessive blade tension
- Insufficient blade tension
- Operator is twisting the hacksaw while in use
- Tooth count is incorrect for material (usually too coarse)
Good Hacksaw Cutting Techniques
Much like a file, a hacksaw only cuts on the forward stroke. It’s a good idea to start the cut with the material in the center of the blade. In use, try to use even pressure on the frame, but downward pressure should only be applied on the forward stroke.
Do not apply pressure on the return stroke. In fact, it’s good practice to lightly lift the blade on the return stroke.
You should use a maximum of 50 forward strokes per minute when cutting.
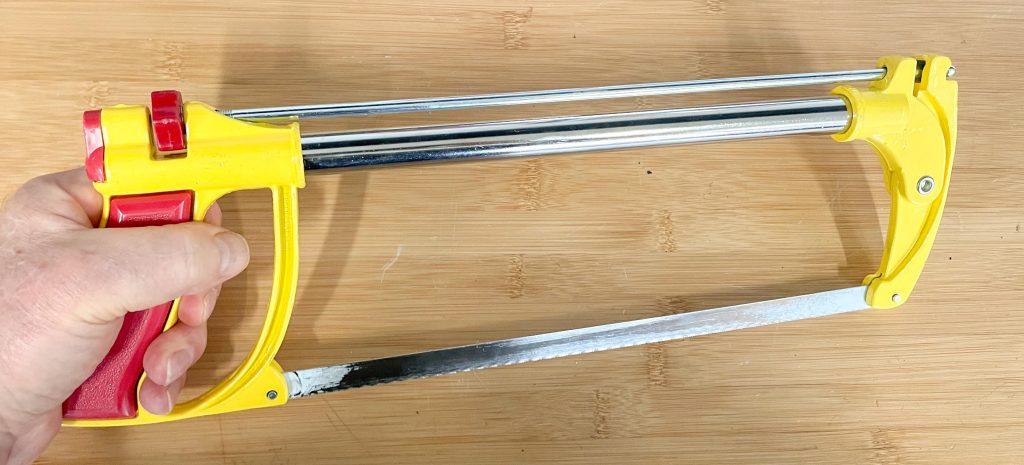
A light amount of oil or cutting fluid can be applied to the blade or the material or to both. This will assist in making the cut. Keep the saw blade moving in a straight line. If you keep the pressure constant and cut in a straight line, you can avoid twisting the blade and at the same time, keep the blade from becoming pinched.
As you can well imagine, there are all sorts of different hacksaws and blades out there, ranging from midget saws to compact models all the way up to regular 12 inch options. Need to start cutting some metal? Find plenty of hacksaws at SummitRacing.com.
Comments