Chevy blocks of all kinds are a dime a dozen because they can be found everywhere. However, what if you’re building a rare Z/28 Camaro with the coveted 302 block casting that has been bored to 0.040 or 0.060 inch oversize and has no further to go? It would certainly be worth the investment as a rare casting to sleeve the block. The same can be said for any rare block casting, especially where there are matching numbers, or a very limited number were made to begin with.
Dave Akard of Burbank Speed & Machine is saving a damaged Chevy 327 block in need of sleeving to make it better than new. It becomes better than new because it is a seasoned iron block which will have new sleeves. He will save this block with Melling cast-iron cylinder sleeves, which are available from Summit Racing Equipment. You can buy cylinder sleeves one at a time or all eight, depending upon the extent of your needs.
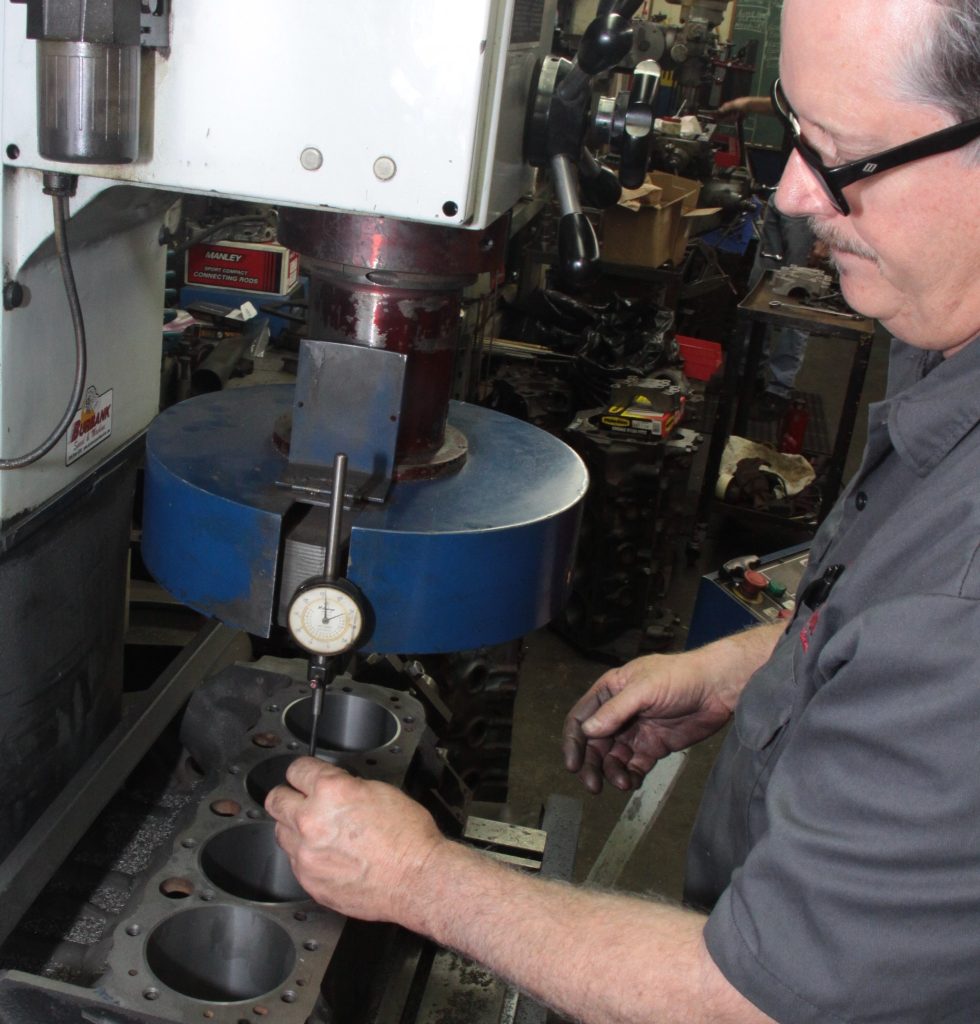
Dave suggests the decision to sleeve a block depends upon value and little else. Sleeving can cost upwards of $200 per cylinder depending upon your locale and the cost of doing business there. When sleeving becomes cost prohibitive, a new Chevrolet Performance block makes more economic sense.
Melling sleeves are centrifugal cast-iron engineered to tolerances down to one half of one thousandth of an inch on modern CNC equipment for precision accuracy. The centerless outside diameter grinding process means perfectly round bores and the iron used offers a Brinell hardness of 241 to 293, which machines easily with strength and durability similar to that of ductile iron. The average tensile strength of these cylinder sleeves (45,000 to 50,000 psi) is considerably greater than standard OEM-style ductile iron sleeves. Not only do these sleeves perform well for damaged or oversize bores, they also offer strength.
Dave tells us there are different approaches to installing cylinder sleeves in a worn block. Some machine shops put cylinder sleeves into a deep freeze to shrink them down to where they’re easier to press into the block. Dave bores out each cylinder to where the sleeves can be pressed into the block with an interference fit. He leaves a lip at the bottom of the cylinder, which prevents movement.
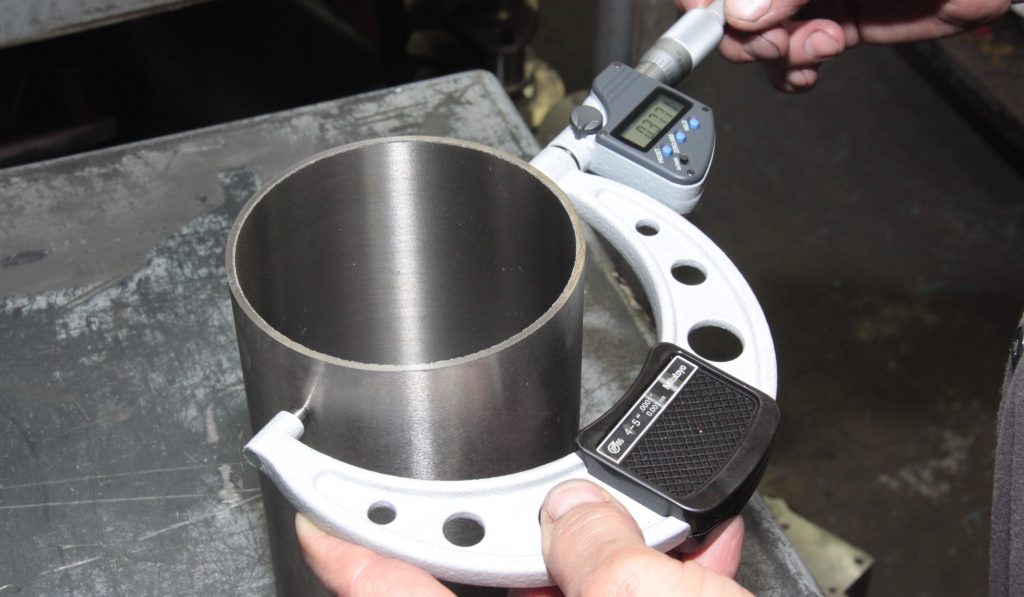
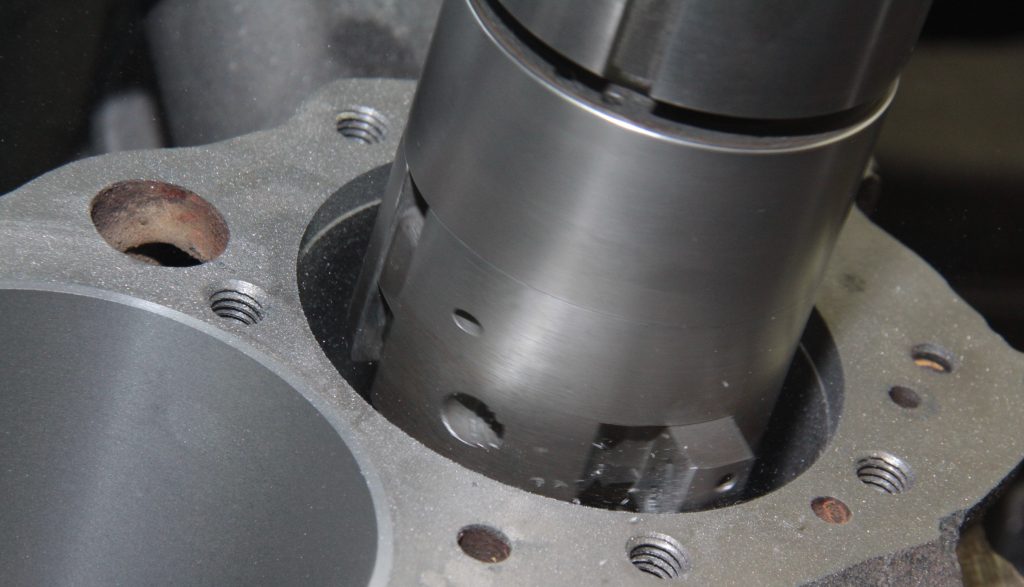
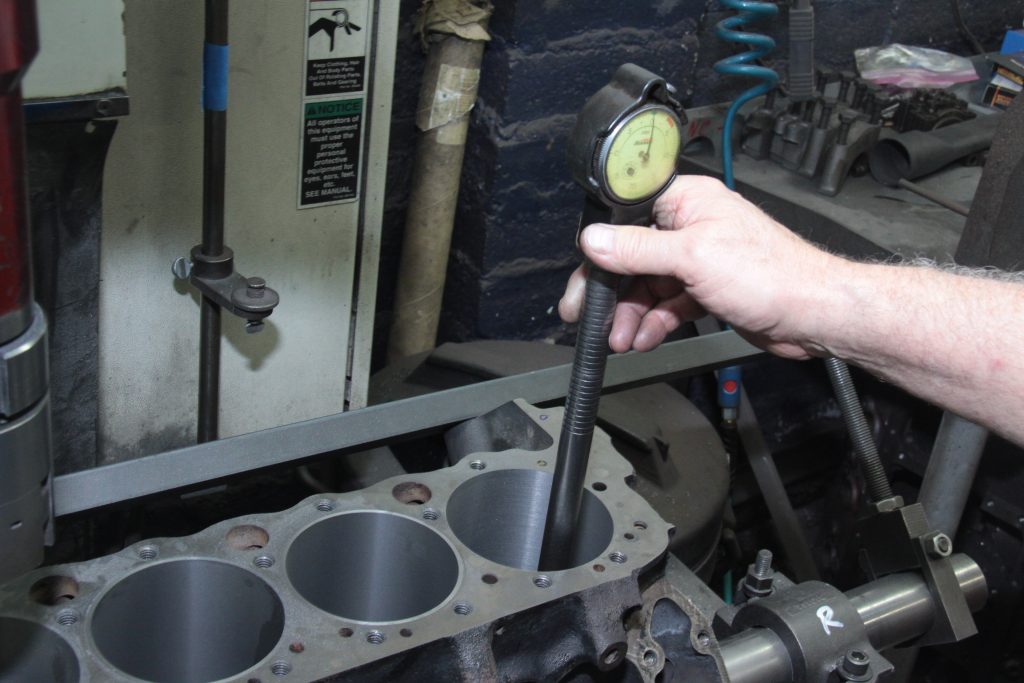
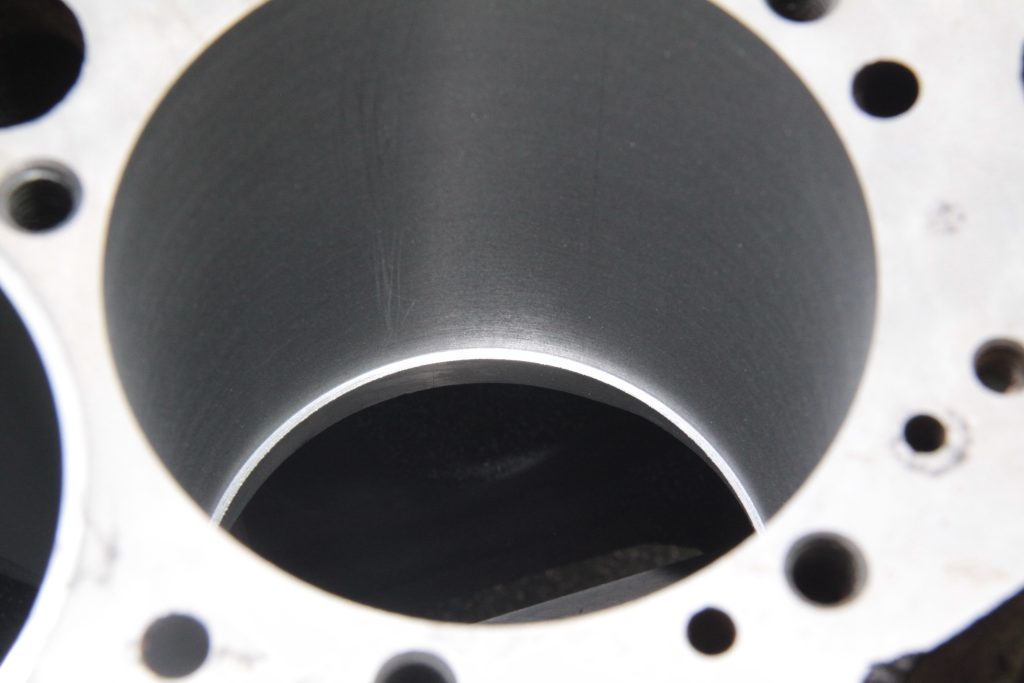
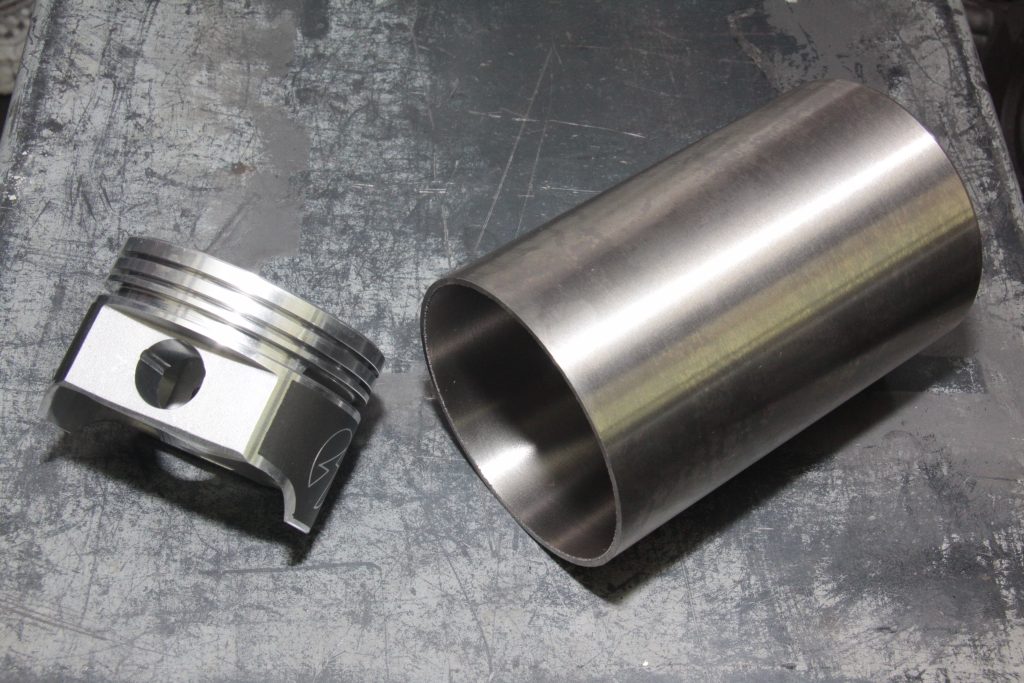
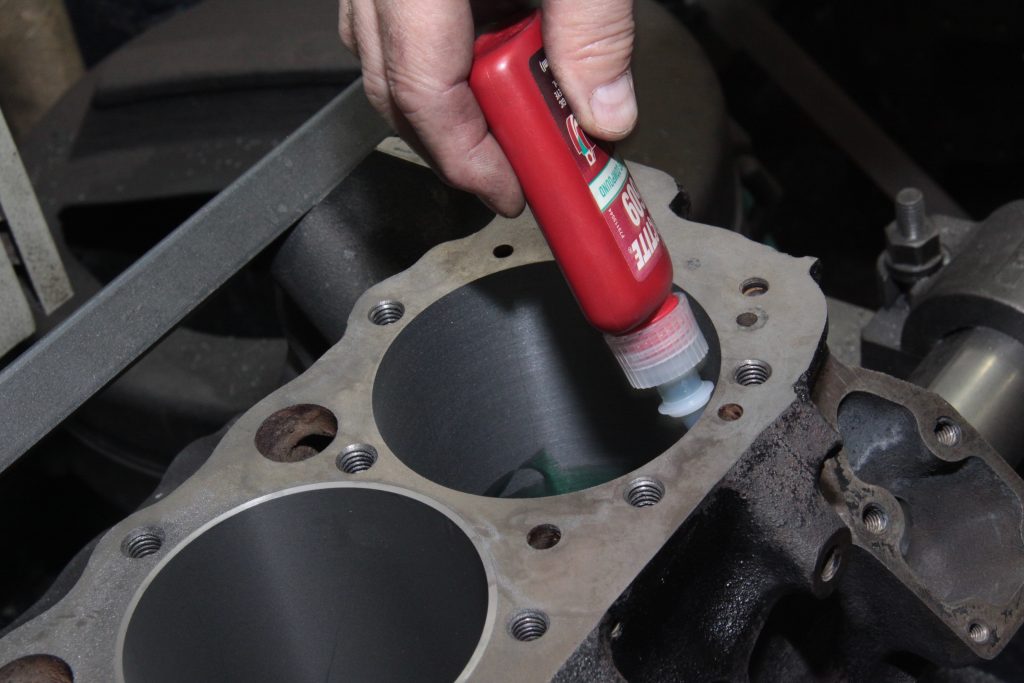
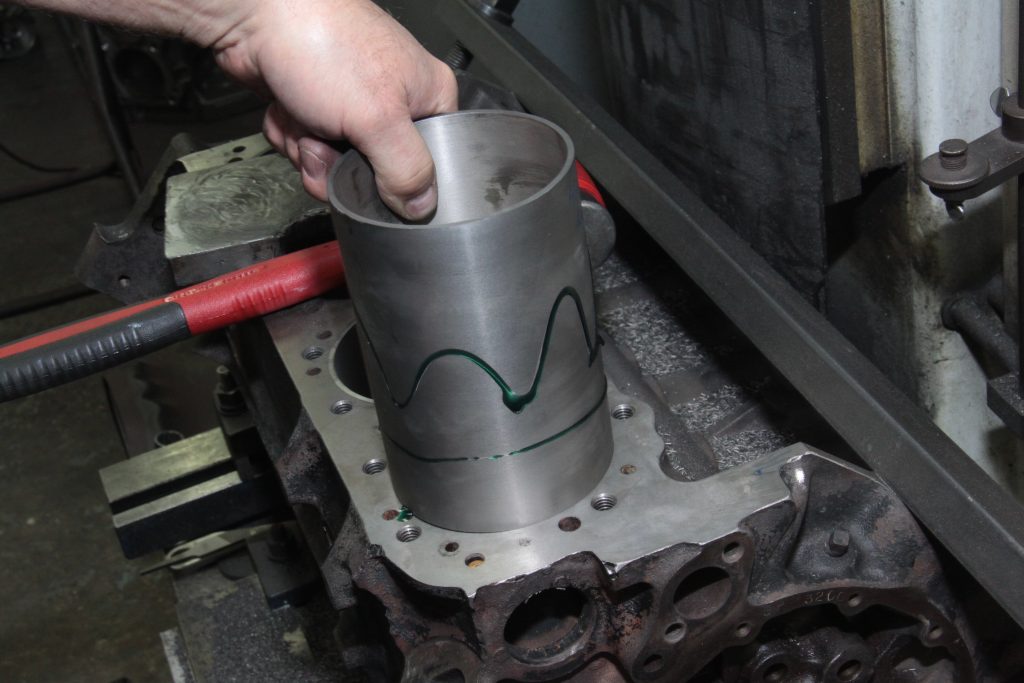
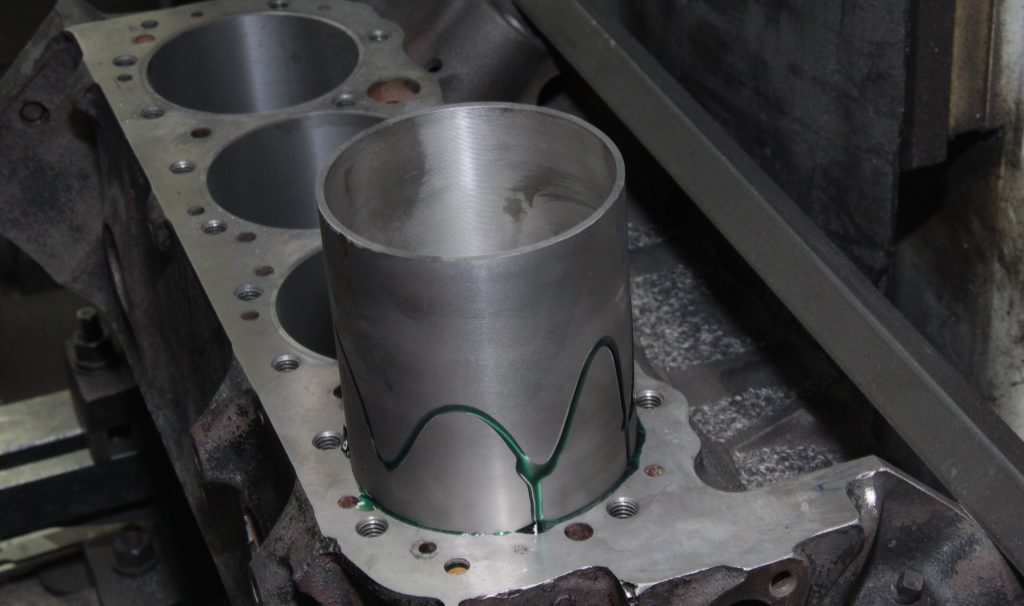
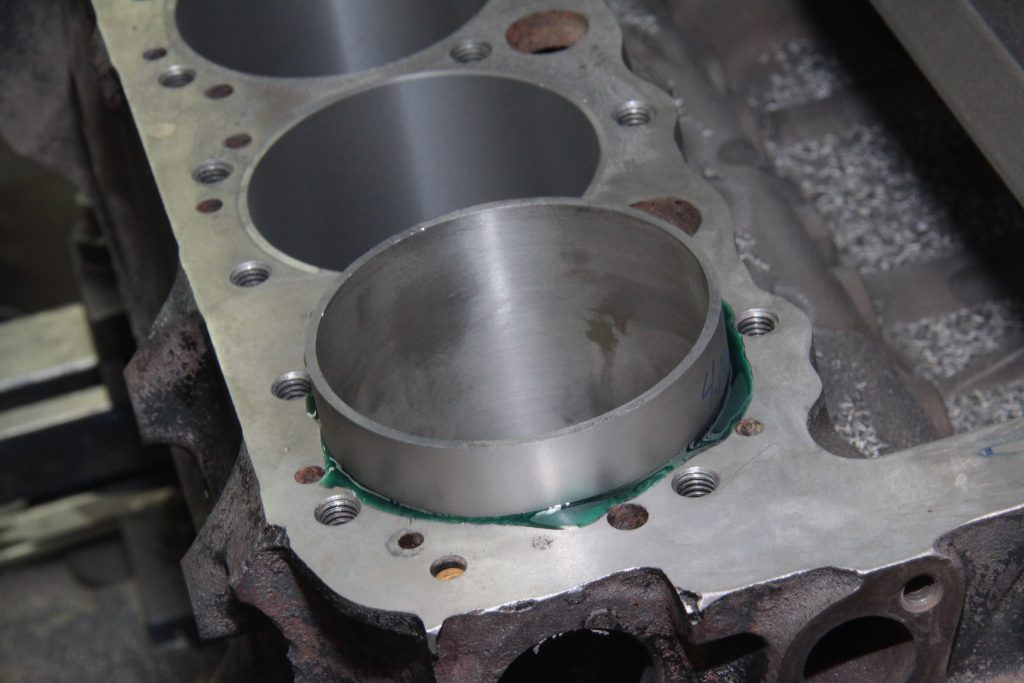
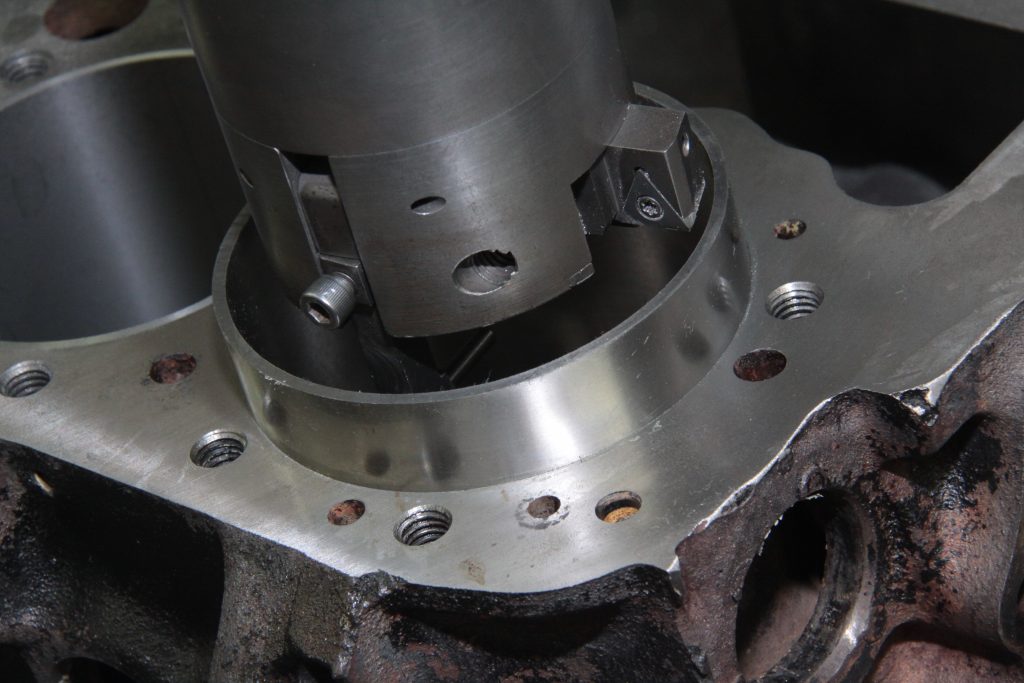
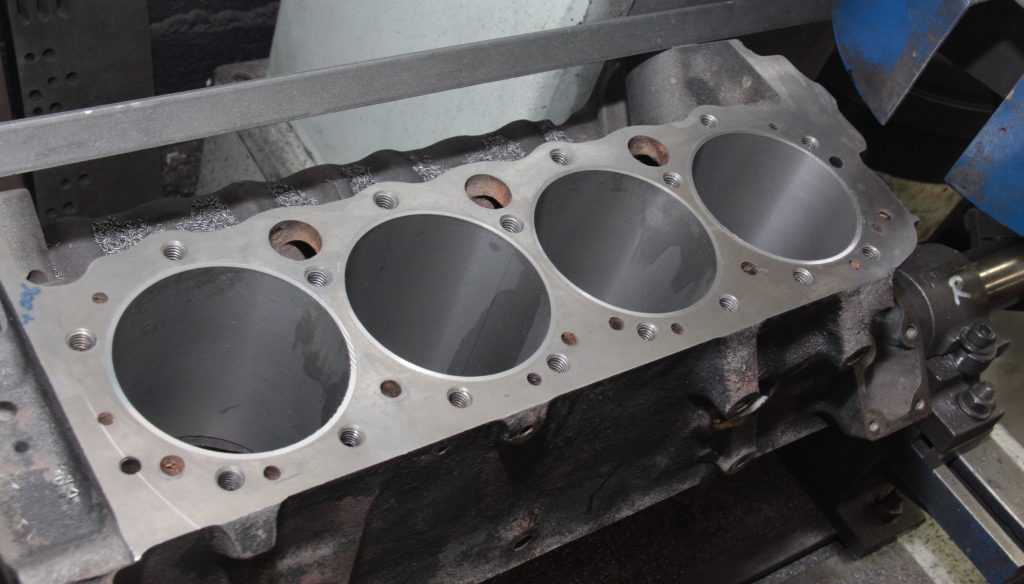
Great article…..! I have a Chev Firenza CanAm, one of a 100 built in South Africa for homologation. It used the DZ302 and Muncie M21 gearbox. There are many articles on it… Please read up!..1100kg with a DZ302. One of the quickest cars of the time…. My numbers matching DZ block however is already 0.060″ overbore, and obviously I would need to sleeve the block sometime in the future. My question comes in with respect to the original cylinder wall thickness left after boring for a sleeve. I have heard many horror stories about the block cracking between cylinder and head bolt holes when the heads are torqued……?
Thanks
Justin