I’ve got a Chevelle with a 468ci big-block with a pretty big cam, Edelbrock Performer RPM intake, a Holley 750cfm HP carburetor, and an HEI ignition. The engine idles way rich and will force me out of the shop if I idle it inside for more than a minute or so.
I’m not much on carburetors and a couple of friends have told me to change the power valve to a lower setting. They say that if the engine idles at a low enough vacuum that the power valve will open and make the engine run rich. Problem is, I tried that and it didn’t help. What am I doing wrong?
M.S.
We don’t have a ton of details here to help us dial in your situation but we can offer some suggestions, in hopes that one (or more) of them may solve your problem. You are definitely not alone here, as this is a common issue. Let’s start by resolving that pesky urban myth about power valves.
The power valve on a Holley carburetor employs a technique that dates back to the earliest carburetors. The idea is to allow the carburetor to run smaller jets in the primary metering block during light load driving such as in town where the throttle is open enough to trigger the main metering circuit but still has some manifold vacuum–let’s say around 10 inches or so. This generally requires only around 15 to 20 percent throttle opening to initiate fuel flow through the main metering circuit.
The power valve opens when the manifold vacuum drops below the valve’s rated opening point. Holley power valves are rated in inches of mercury (″Hg) stamped on the valve. Inches of mercury is the rating displayed on a normal vacuum gauge. The most common Holley power valve is one that opens at 6.5 ″Hg. This value is low enough to keep the valve closed under mild throttle opening. For example, if your engine is cruising at light load at 10-12 ″Hg then the power valve will be closed. The power valve will only open if you open the throttle hard enough to lower the manifold vacuum to 6.5 ″Hg or lower.
Engines with big camshafts with lots of overlap often idle at reduced vacuum levels of 8 inches or less. Then if we add the load from an automatic trans in gear, it’s possible you could hit that 6.5 ″Hg opening point. Here’s why that doesn’t make a difference to idle quality.
As we mentioned earlier, the power valve is tied into the main metering circuit, so if the valve opens it merely opens into the main metering circuit that delivers fuel to the boosters. At idle, there should never be any fuel coming out of the boosters. If that occurs it’s usually an indication of an excessively high float level. But back to the point, the power valve can open all it wants, but it will not deliver fuel to the engine at idle.
In your case, this is why changing the power valve opening point to below the idle vacuum level did not improve your rich idle condition.
Now let’s address where you could have problems.
Let’s start by looking at some simple carburetor operating conditions. First thing to do is, with the engine turned off, slowly count the number of turns it takes to lightly bottom out each idle mixture screw. We often see idle mixture screws wildly different from side to side. It sounds like you may have a Holley carburetor with four idle mixture adjustment screws. Count the number of turns out from the seated point for all four screws. If they are not the same, set them at 1-1/2 turns out (counterclockwise) from fully closed.
If the engine idles better, then carefully turn all four of them in (clockwise is leaner) about 1/16th of a turn and evaluate the change on your vacuum gauge. We’ve found that these minor adjustments allow you to sneak up on an ideal position for all four screws. Positive changes add vacuum, so shoot for the highest vacuum reading attainable with the engine in Park or Neutral. Then turn each screw in (lean) about roughly 1/32-inch. This will make the engine just a touch leaner at idle but still retain high manifold vacuum. Work carefully and slowly to achieve the best results.
Before we go further, another way to improve idle quality is with sufficient ignition timing. You didn’t mention how much initial timing you have but this should be no less than 12 to 14 degrees. Much depends upon camshaft overlap. But 12 to 14 degrees of initial timing is typical for an engine with a big camshaft. Of course, excessive timing can also cause problems so it should not exceed 20 degrees.
Let’s say that you find that one of the idle mixture screws has no effect on idle quality. Sometimes that might be because the idle air bleed hole in the top of the venturi is blocked or plugged with dirt. A quick shot of carb cleaner down the hole might repair the problem. On a Holley carb there are two air bleed holes for each venturi. The idle air bleed is the one located on the outboard side. Shoot some carb cleaner down through this hole and see if that repairs the problem. If the idle mixture screw still does not respond, then the carb may need to be disassembled and cleaned.
If we assume that all four of your mixture screws are responsive but the engine still idles very rich and that it idles in gear around 9 inches or less of manifold vacuum, then there is still another way to repair the problem.
We can’t go into a ton of details as this involves a long description of how the idle circuit works. But the short version is that there is an idle transfer slot located next to the throttle plate on all four corners of your carb. Big camshafts with lots of overlap require a larger throttle opening to allow enough air into the engine to idle properly. When adding idle speed with the curb idle speed adjustment on the primary throttle linkage, this moves the throttle plate enough to expose a large portion of that idle transfer slot. Stock throttle settings generally barely uncover this slot. This transfer slot is designed to introduce additional fuel into the engine from the idle circuit to compensate for more air entering the engine during light throttle application before the main metering circuit takes over.
By cranking open the idle speed screw to compensate for a long-duration camshaft, this exposes the transfer slot and adds more idle circuit fuel into the engine. This transfer slot fuel is not controlled by the idle mixture screws. This is the critical point. Transfer slot fuel is metered by a small restriction in the carb called the idle feed restrictor.
The solution for your problem is to drill small holes in the primary and perhaps the secondary throttle plates to allow additional air into the engine. This should make the engine idle faster, which will allow you to turn the idle speed screw counter clockwise which will close off some of the idle transfer slot. This will take some experimentation by drilling a small hole in all four throttle plates and then testing the idle speed and then removing the carb again and drilling slightly larger holes until the curb idle position almost completely closes off the idle transfer slot. A 1/32-inch of idle transfer slot exposed is acceptable.
In the past, we’ve started with 3/32-inch holes drilled in the throttle plates and then increased the size until the throttle position is back to where it’s exposed very little of the transfer slot. This may take five or six or attempts or more with 1/32-inch increases in drill size. This may sound tedious (and it is exactly that), but this will allow you to sneak up on the right size holes. If you drill too large too quickly, the idle speed will be too high even with the primary throttle blades fully closed. Then you will have to either braze the holes closed or replace the throttle blades and start over. So the message here is to work slowly and carefully.
There are a few other tricks you can try but space prevents us from getting into these as this answer is already quite long. This procedure should allow you to set the idle speed at the desired rpm while then allowing you to lean out the idle mixture screws—which should make the idle mixture much more tolerable.
A leaner idle mixture will also make your engine happier and, as a side result, your engine oil won’t turn black quite as quickly.
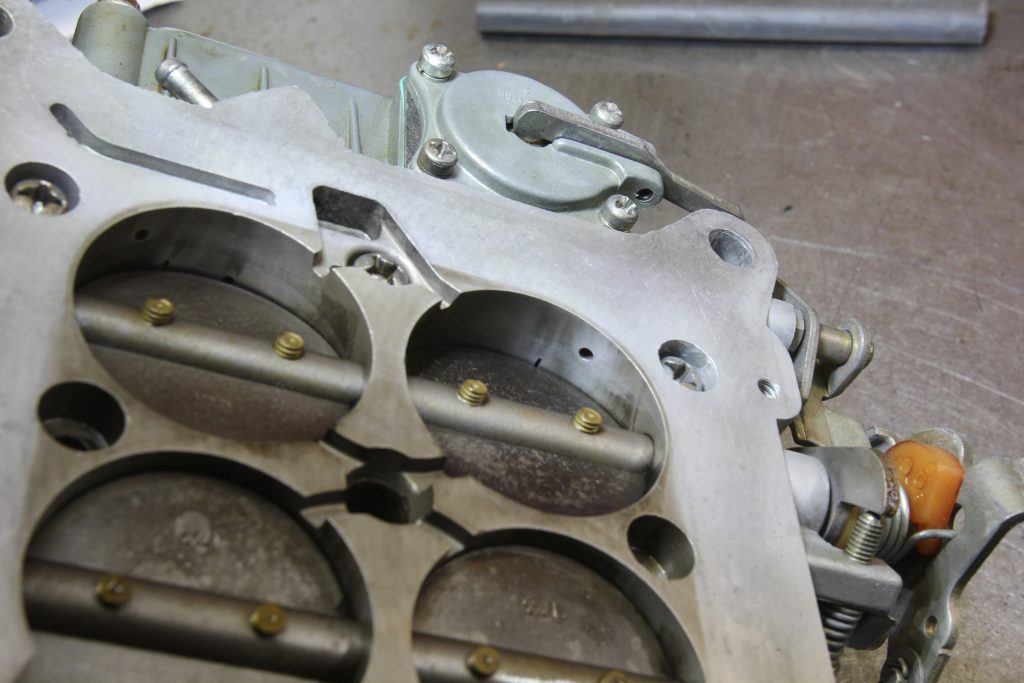
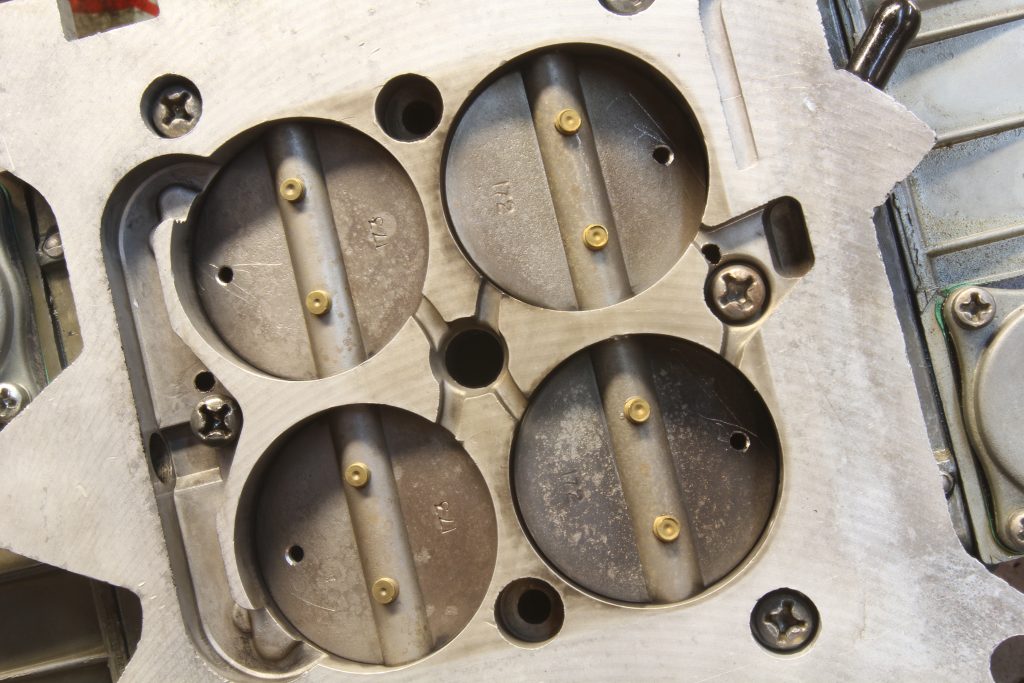
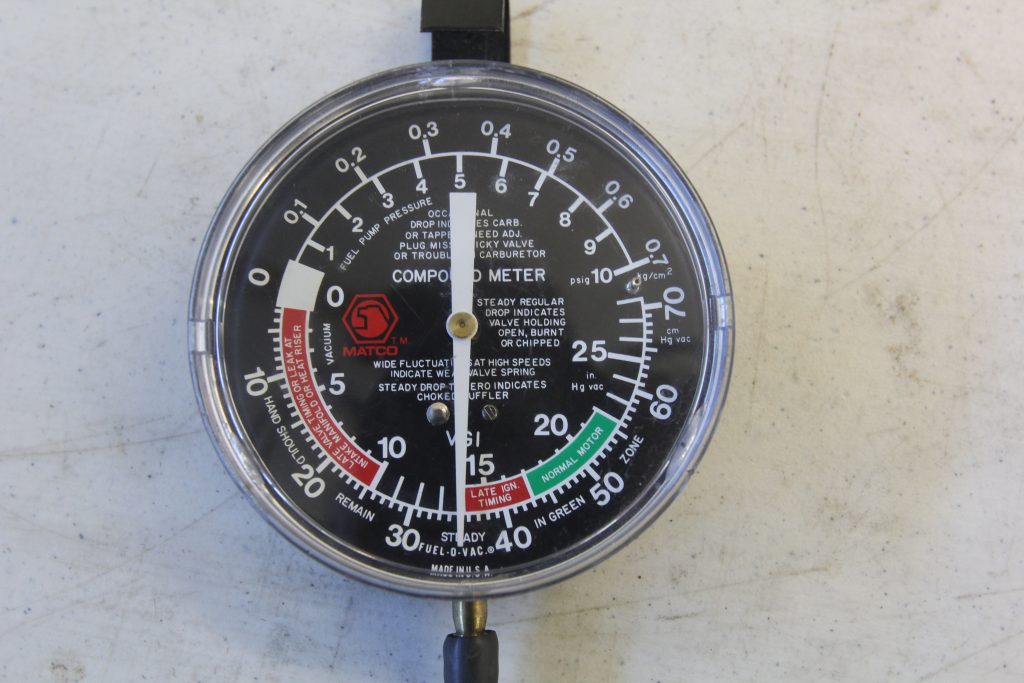
[…] I’ve got a Chevelle with a 468ci big-block with a pretty big cam, Edelbrock Performer RPM intake, a Holley 750cfm HP carburetor, and an HEI ignition. The engine idles way […] Read full article at http://www.onallcylinders.com […]
Good info. BBC are notoriously rich idlers and drilling the holes does work.
Unless your are a multimillionaire follow the advice on drilling the holes, cuz if you don’t, it gets real expensive buying new throttle plates. And then you have to seat them properly when changing them or you have created another problem.
Very interesting, however, now the same problem, but on a SBC, Edelbrock carb, Edelbrock Performer manifold, mild performance cam, long tube headers, TrickFlow heads, MSD race dizzy, MSD 6A ignition and coil, manual trans. Same symptoms;very rich at idle, poor idle quality. Have tried winding the idle mixture screws all the way in, then backing out 1½ turns, but to no avail.
Rik – send me a note at my email address with moredetail and let’s see if we can figure this out.
It sounds like a vacuum leak…
lanejsmith@yahoo.com
Very interesting and informative. How does this procedure work/compare to a small block Chevy?
In my experience it would be the same. It is just more common in the big blocks because of the additional displacement. I had a 350 with a 750 vac secondary carb that I had to work the holes in the throttle plates & set the secondary idle position to get it to idle right.
Hey Ben: I had same issues running rich at idle on a 454 with thumper camshaft and 750 Holley. After pulling carb I found the primary butterfly open so far that the transition slots were dumping fuel at idle. The secondary butterfly was completely shut so I adjusted the secondary open just enough to add airflow. Worked great!