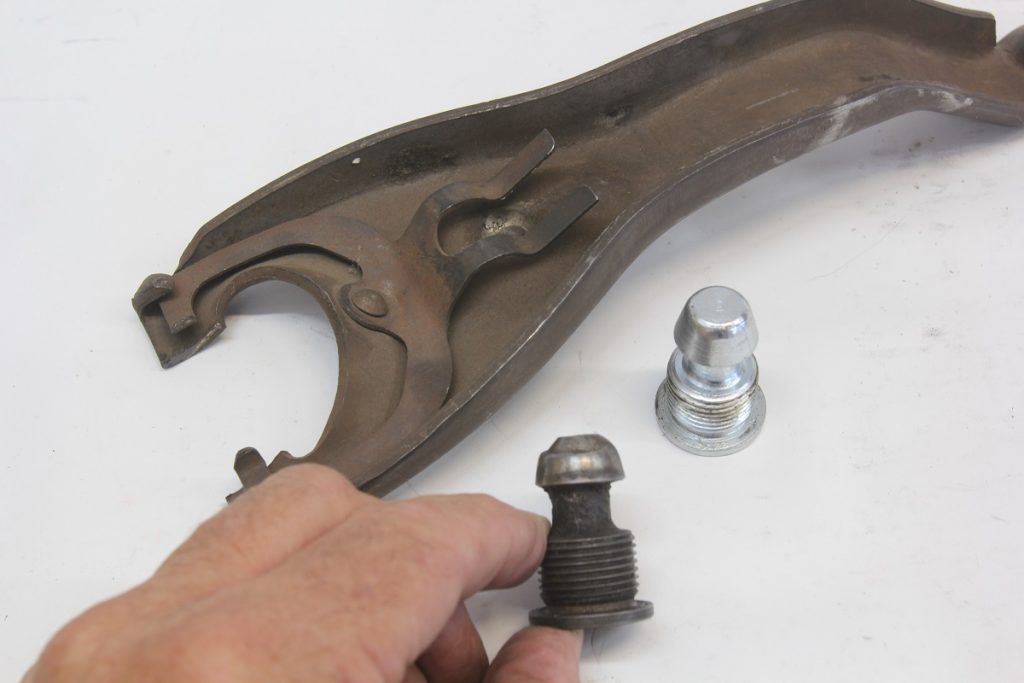
Does a hydraulic system make the clutch pedal effort easier than a mechanical linkage? A friend of mine says the effort will be the same because all the force is from the pressure plate that has to hold the clutch. Is that true? The clutch pedal in my ‘71 Chevy truck is very stiff and I’d like to fix that. Thanks. — M.S.
…
Jeff Smith: This is a great question that — like most of the answers in this column — isn’t answered easily or quickly.
Let’s start with a simple approach to the question of whether a hydraulic system will fix your problem. It’s a common misconception that a hydraulic system will reduce the pedal effort.
However, in your case it may be true because there is likely a problem with your mechanical system that is creating the higher effort.
When we asked Fred Taylor at McLeod Racing your question, he told us that hydraulic systems do not offer substantial improvements over a simple mechanical system.
Your friend’s reason is actually pretty close. The load required to press in the clutch pedal is based almost entire on the load created by the pressure plate.
Many enthusiasts equate newer cars with having very light clutch pedal effort and attribute that to the hydraulics. But the reality is that these lighter clutch pedal efforts are mainly based on a lighter duty pressure plate.
Both mechanical and hydraulic systems use a form of leverage to reduce pedal effort, and hydraulics are not necessarily going to make that easier. As Taylor told us — the easiest way to reduce the pedal effort is to go with a softer pressure plate.
But let’s look at why your existing clutch system is so stiff.
Since the truck is almost 50 years old, it’s entirely possible that the linkage system is original and therefore likely worn out. Our experience with early Chevelle mechanical linkage is that the pins connected to the cross shaft wear badly, which will cause them to bind.
But more importantly, the one component that never gets changed when a clutch is serviced is the ball stud inside the bellhousing. This is the ball that is bolted to the bellhousing and is where the release bearing pivots. On most drivelines, it can only be changed by removing the transmission. We’ve seen many original ball studs that are severely worn. The normal wear pattern on this ball stud tends to push the release arm at an angle that drastically increases the effort required to release the clutch. If you disconnect the linkage from the release arm, you may be able to feel this by moving the arm manually. The best way is to visually inspect it, but we can all but guarantee that it’s badly worn — as is the release arm.
The simple solution is a replacement ball stud and release arm and to put a small amount of grease on the contact nose of the ball stud and release arm. This simple exercise can radically reduce the pedal effort. These parts are not expensive, but will require removing the transmission in order to change them. It would be a wide idea to replace the release (throw-out) bearing at the same time.
Taylor offered some numbers to support pedal effort requirements. A performance clutch pressure plate might require 500 pounds of force to release the load on the clutch. But the effort you put on the pedal is far less than that because of the mechanical leverage.
We measured a set of ’66 Chevelle clutch linkage pieces because we had them available. The ratio generated by the clutch pedal is 4:1.
Next, the Z-bar linkage also produces a small leverage advantage of 2.1:1 and then the release arm lever also offers a lever ratio of 2:1. Let’s use a force generated by your leg of 30 lbs.
The formula would be:
Force applied by your leg x pedal ratio x Z-bar ratio x release arm ratio = total force on the release bearing.
So if we apply 30 lbs. of force on the pedal: 30 x 4 x 2.1 x 2 = 504 lbs. of force applied to the release bearing on the clutch fingers. A stock pressure plate requires far less load than this, but performance clutches are often in the 500 lbs. of force area.
One thing to keep in mind is that a diaphragm clutch doesn’t operate quite the same way as the older, three-finger spring clutches like a Long or Borg & Beck.
With a three-finger clutch, as you depress the fingers, the fingers compress the springs. As the spring is compressed, the load increases and the pedal gets harder to push.
A diaphragm clutch uses what is called a Bellville spring. At first, as the Bellville spring is compressed, the load will increase. But at the release point, the spring runs over center and most of the load falls away. This makes a diaphragm clutch pedal much easier to hold down in traffic compared to a three-finger clutch.
Before we move to the hydraulic side, let’s throw in a related situation we’ve run into. We’ve had situations where a car sits for a long time — years — without moving the clutch. Then when the car is started, the clutch won’t release. If the car has been stored in a high humidity area, the clutch disc can rust and literally stick to the flywheel so that when the pedal is depressed, the clutch continues to spin, but the transmission can’t engage.
The quick fix is to release the clutch with the engine off and rock the car back and forth to hopefully release the clutch. If the system is apart, the best solution is to lightly sand the flywheel and pressure plate as well as the disc to give both surfaces a fresh place to start.
Moving to the hydraulic system, the leverage is a combination of mechanical pedal ratio and hydraulic leverage.
According to Taylor, the pedal ratio multiplies the force applied at the pedal at roughly a 6:1 ratio and sometimes more. Then with the McLeod design, (other systems will vary) the force created by the master cylinder is doubled by the hydraulic release bearing. We won’t get into all the math, but essentially the pedal effort remains very much the same between the mechanical and hydraulic systems, so there is not major pedal effort improvement with hydraulics.
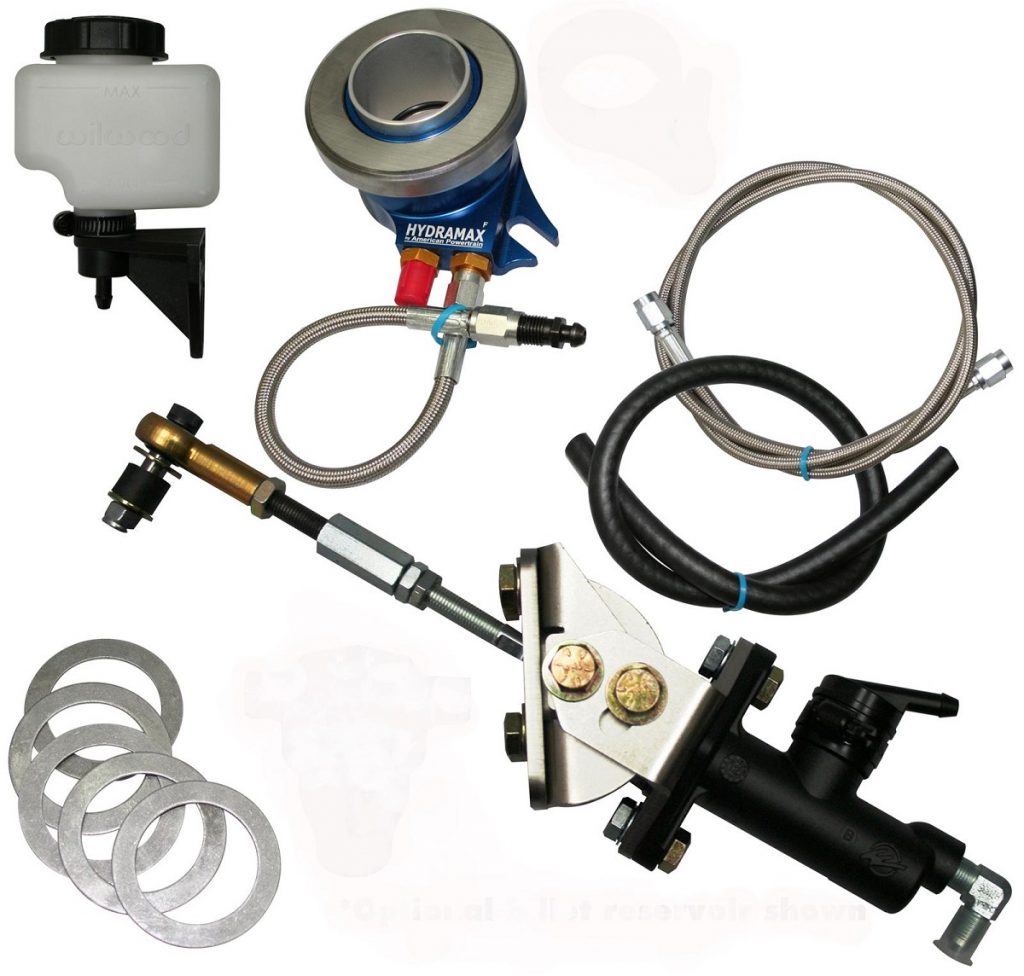
All good info. Another factor at play in hydraulically operated Belville/Diaphragm clutch is clutch plate facing wear. As the clutch plate linings become thinner the geometry of the diaphragm pivot point changes to the extent that it never reaches over center. Thus the pedal effort is high throughout it’s travel. A clutch in this state usually engages near the top of the pedal travel.
Love your tech articles. I was wondering what you would suggest for a “mild” HP plan for a 1989 302, in an F150.
It’s bone stock, like 180 HP or so?
So headers and perhaps FiTech? Ignition?
I don’t want a lumpy cam, and I’m not going to drag race. I would like some grunt without losing the “driveability”.
Thanks in advance for your guidance.
thank you for explaining this, I’m trying to figure out if I want a hydraulic clutch & throughout bearing or just hydraulic clutch pedal. and I’ would like to know if this system is discrete
/separate from the hydraulic brake system?
71 429 CJ top loader, mcloud 12” 3 finger clutch,American power train kit with wilwood puller slave. Pedal effort slightly better than stock Z bar. Wondered about modern drive lines fulcrum style pedal rod? Would it take the load off?
Does the hydrolic clutch shift the same as mechanical,My 66 nova is auto ,like to change it to muncie 4 speed, But when street racing I like to power shift, You know put it to the floor don,t let off and just pound it through the gears, Don,t know if the hydrolic would be fast enough, Thanks
Mechanical for me, hydraulic clutches suck, with mechanical you can hold the gas pedal on the floor and shift for super fast shifting, speed shifting, can’t do that with hydraulic. They feel like stepping on a marshmallow. My m-21 muncie will shift circles around the ZF in my 1990 ZR-1.
I will take mechanical linkage any day over hydraulic. With mechanical you can feel the pressure plate, a must for drag racing and speed shifting. My 1973 455 HO Firebird will shift circles around my 1990 ZR-1. I can hold the gas pedal on the floor and shift with the firebird, the vette can’t do it near as fast. For daily driving hydraulic is fine and seems lighter than the firebird, but I have a very strong pressure plate in it.
Worthless article. Lack of quality information. Should show pedal force vs pressure plate static force graph or numbers. Saying performance pp is generally 500 lb makes no sense. Pp ranges 1500-3200 static force