I just bought a big-block 454 engine from a friend and I want to put it in my ’69 Camaro with a 4-speed trans. The engine was rebuilt a long time ago with 10.5:1 forged pistons and rectangle port iron heads. The engine has an older, solid lifter cam it in but my friend couldn’t remember the specs. All he could tell me was that it was a big cam. I live in Northern California and I’m worried the iron heads might make the engine detonate with our weak 91 octane gas. Short of pulling the timing way back or buying a set of aluminum heads, is there anything I can do?
L.M.
Jeff Smith: Detonation is a fickle thing and can be caused by a slew of different variables. Most enthusiasts concentrate mostly on static compression ratio as the root cause but there are plenty of other suspects. Let’s start with first looking at the phenomenon of detonation. The most popular definition is uncontrolled combustion that results in an excessive spike in cylinder pressure. This spike tends to rattle the piston causing that all-too-familiar noise that has been described as eight rocks rattling around in a Folger’s coffee can. This generally occurs when the remaining fuel/air mixture in the cylinder spontaneously lights off toward the end of the combustion cycle. This occurs only after the spark plug has initiated the combustion process. Another, much more dangerous process is something called pre-ignition. This is when ignition initiates before the spark plug fires. This is far more dangerous situation that usually leads to catastrophic engine damage.
One contributor that many seem to focus on is the contention that iron heads retain more heat in the combustion chamber and therefore are more susceptible to detonation than aluminum heads. The closest I’ve done to test that situation was a comparison of iron to aluminum heads on a small-block Chevy to see if there was any difference in power. That test was inconclusive because the combustion chambers were not identical. The aluminum cylinder heads featured CNC machining versus as-cast iron chambers. Otherwise, everything else in the engine was the same and we discovered the aluminum heads made more power. My feeling was that the CNC-machined chamber contributed to better combustion, but this test also pointed out that it’s difficult to see improved power with iron heads, so that would point to the notion that iron really doesn’t measurably increase the cylinder pressure.
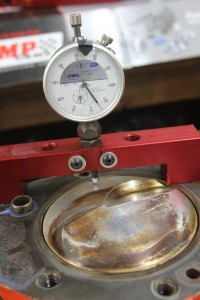
There are other factors that certainly do contribute. Most performance V8 engines utilize wedge chambers (as opposed to hemispherical) which use the quench or flat area between the piston and the head to contribute to mixture activity. The tighter this quench area becomes (moving the piston closer to the head), the more the mixture motion in the chamber is enhanced and this has been shown in many tests to greatly contribute to reducing the ignition timing required for maximum power. This is a significant point that can’t be over-emphasized and yet is often ignored. A piston-to-head clearance of less than 0.040-inch for a typical steel connecting rod engine is a good place to start to improve combustion efficiency. So my recommendation would be to consider removing the heads and at least measuring the piston-to-head clearance. Sometimes using a thinner head gasket will improve this situation.
It’s worth noting too that combustion chamber shape is a major contributor to improving combustion efficiency. This goes beyond just smaller, tighter chambers but the latest chambers with a heart shape that tends to push the combustion event toward the exhaust valve has been shown to improve power and reduce ignition timing requirements. Ignition timing is perhaps the simplest gauge for combustion efficiency. Late model engines such as the LS family typically operate with barely 28 to 32 degrees of ignition timing. Yet it wasn’t all that long ago that a high performance small-block Chevy or Rat motor demanded 40-plus degrees to complete the combustion process. Ponder that difference for a moment as the difference is huge. This means with less ignition timing, the combustion event is occurring much more quickly and yet we typically see these late model engines as less detonation sensitive mainly because of this more efficient combustion process.
Inlet air temperature is another major contributor to detonation sensitivity. Tim Wusz works for Rockett Brand racing gasoline and he recently told me about an OE performance test many years ago in which they compared inlet air temperature to octane requirements. The testing evaluated several engines operating with inlet air temperatures that varied between 100 and 200 degrees F. What they found was that for every 25 degrees reduction of inlet air temperature, the octane requirement was reduced by one full point. As an example, when they reduced the inlet air temperature from 150 to 100 degrees F, the engine was able to run on two full octane points lower grade gasoline—moving for example from 93 to 91 octane. The opposite also holds true that as the inlet air temperature rises, the octane requirement also increases.
This might at first seem surprising. Cooler air is denser, which contributes to creating high cylinder pressures yet this higher cylinder pressure is less detonation sensitive. Conversely, when an engine gets hot, it will be much more prone to rattle because the combustion chambers have probably created hot spots that tend to initiate combustion and create that pressure spike in the cylinder. This leads us to the obvious point that a hotter engine will also tend to be more detonation sensitive so coolant temperature is another contributing factor.
There are probably a dozen more contributors, one final point is worth examining but is often overlooked. An engine achieves peak volumetric efficiency (VE) around peak torque. This is where cylinder pressure is the highest. By this time, maximum ignition timing as also been achieved. Before and after peak torque, the engine may benefit from greater ignition timing, but also will probably be most prone to detonate at peak torque. Now that electronic ignition curves have become easy to create, you might think about a curve where if the engine tends to detonate around peak torque, removing a degree or two of timing around that point could produce positive results. In the past with mechanical advance mechanisms, a non-linear curve could be achieved but it required expensive retard mechanisms. With digital ignition curves, an irregular curve is as easy as picking out points on a plot. As an example, MSD offers its Pro-Data+ software that can be employed with several different ignition control boxes for most engines.
This answer has been somewhat less specific to the original question but this is mainly due to the wide variety of situations that create detonation. And we haven’t even spoken about water injection, detonation sensors, or electronic controls that can be used to push the engine to make more power while controlling detonation. We’ll save that discussion for another time.
Great article. Thanks
[…] The key to making this a successful venture would to become fanatical about preventing detonation. […]
Run it if it pings pull heads cc combustion chamber to see what you have for sure but I would get little bigger chamber to get compression down to 9.5 max but that’s just me lol
Good article. I am in the process of planning this out, my ideal goal is 9.5:1 compression with the heart shaped chambered AFR Renegade heads I should be capable of running regular grade 87 octane with a proper timing curve.
I just have to wait and see what the guy says when I ship him my dist to have him recurve it on his sun machine. I just wished I could find what pistons blueprint is using in their 306 short block as that will help me decide as they are running 9.5:1 compression with what they claim to be 60cc heads so with 58cc heads I will be pushing 9.75:1 which I think is too much for me but still with in the 8.50:1 to 10.50:1 compression ratio recommendation. Just don’t want too high as this is my every day truck and I want to run regular grade fuel.
Another thing this article didn’t touch on was air/fuel ratio, running a richer fuel mixture will result in a cooler combustion and will help stop detonation. Timing is another thing that helps as too much timing will cause more heat as well. Problem that stock ford engines have they get horrible gas mileage till you pin the ignition to have no more than 32 to 36 degrees of total advance. Why once I get the compression ratio figured out and get the final specs I will have my cardone new production distributor recurved on the timing curve to work with my setup to get my engine to run on as low as octane fuel as possible.